ウエハ大型化することと、不良になるチップを減らすことが低価格化に必須となる。しかし、ここでも課題がある。
シリコンでは直径30センチのウエハが主流だが、SiCでは直径15センチのものが最新である。
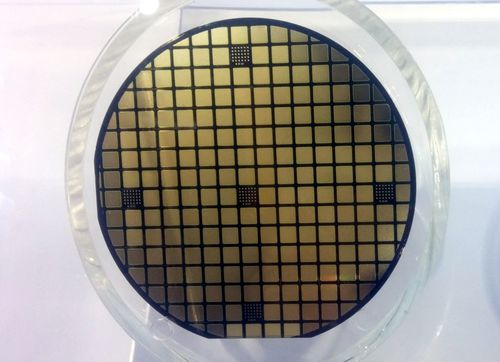
さらに、SiCは結晶に欠陥が多く、SiCからトランジスタを作った際、その欠陥のある場所のトランジスタは不良になってしまう。
また、SiCに素子を作りこんでいく工程は、シリコンよりも高温になる。原理上、SiCの半導体はシリコンよりも高コストにならざるを得ない。
現状、採用例はある程度コストをかけられるもの、SiC採用のメリットが大きいものに限られる。
一方で、SiCは同じ面積でシリコンよりも大電流を流せるため、同じ性能の半導体を小さく作れる。
そうすると1枚のウエハからより多くのチップを作れる。そこで、高コストを取り戻せる可能性がある。
低コスト化を進めていけば、単位面積当たりの価格でシリコンに追いつくに至らなくても、チップ1個の値段においては、シリコンに追いついていく可能性もないわけではないのだ。
そうなれば、鉄道車両や高級品向けであったSiCは、ハイブリッド車や身近な製品にも広がることになり、電気の世界の省エネは一気にに加速していくことになる。
SiCウエハでは米国のクリーが、SiC素子ではドイツのインフィニオン・テクノロジーズの勢力も強い。そのため、日本が圧倒的強者であるわけではない。
また、海外ではコストが高くてもSiC適用に積極的であるようだ。
しかし、日本でも昭和電工がSiCウエハで有力であり、ローム、三菱電機、東芝などがSiCデバイスを作る。鉄道車両では述べてきたとおり実用化が進んでいるし、ハイブリッドカーなど自動車への適用の研究も進む。
SiCによる省エネの拡大では、日本の産業界も活躍していくだろう。