CFRP製の義足をはいた犬(タイで。この記事とは関係ありません)〔AFPBB News〕
2年ほど前、イタリアのスポーツカーメーカー、ランボルギーニと共同研究するための部品製造工場として監査に合格したウチダという町工場が埼玉県入間郡にある。
国内大手2社に続いて監査に合格したため業界の話題をさらった。同社は、東武東上線ふじみ野駅からタクシーで10分ほどの関越自動車道沿いに社屋を構える。
工場と事務所が連なる社屋に足を踏み入れると、所沢ナンバーのカーボン製のスポーツカー「NSX」が出迎える。
取材で通された応接室に並ぶ椅子はレーシングカーの座席のようなデザインが施されている。同社社長の内田敏一さん(48歳)のスポーツカーへの情熱は筋金入りであることは言うまでもない。
スポーツカーから福祉器具開発へ
ウチダは2輪レースやスポーツカーの部品、電動無人ヘリコプターのプロペラなど、世界屈指の企業が認める炭素繊維強化プラスチック(CFRP = Carbon Fiber Reinforced Plastics)というカーボン成形技術を有する。
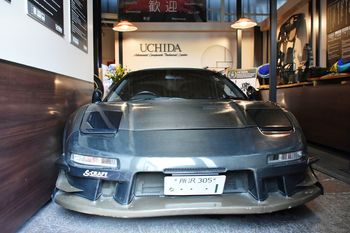
CFRPは、オートクレーブという巨大な圧力釜のような装置で炭素繊維と樹脂を加圧、加熱して硬化させて成型した高精度な素材のことで、鉄よりも強くて軽い。
ゴルフクラブのシャフトや釣竿にはじまり、最近では航空機や自動車への応用で各社がしのぎを削る。
1999年当時、専務だった内田さんはCFRPの特性に着目した。CFRP開発の設備投資に対し、父親であり経営責任者である会長からは合意がえられず、会長が最も信頼を寄せる工場長を粘り強く説得し、オートクレーブ導入を押し切った。
「別のカーボンを使ったバイクや自動車の部品の製造だけでも事業は順調でした。ただ、そういう時こそ次の一手を打たないといけません」
「この頃の年間売上高は1億8000万円。その4割を設備投資に充てることにはなったのですが、そのリスクは新しい技術の導入に伴うものだと考えました」
内田社長はこのように話し、「オートクレーブを使った成型技術を学べる教科書も参考書もなく、大手企業のノウハウに素人が手探りで挑むようなものでした」と明かす。