日本と韓国の海外自動車工場を観察すると、生産の立ち上げやオペレーションの考え方にかなりの違いが見られる。一言でいうと、堅実なものづくり重視の日本と、スピードと規模重視の韓国という構図である。
例えば、現代-起亜自動車。10年足らずの海外生産の歴史にもかかわらず、すでに設備能力ベースで260万台の生産能力を築いた。そのうち、最も急速な伸びを見せている生産拠点は、中国やインドなどの急成長市場の新興国である(中国では100万台、インドでは60万台の生産能力に達している)。
金融危機に端を発した世界的な自動車市場の縮小によって、日本のメーカーは軒並み打撃を受けているが、現代-起亜自動車の場合、影響がそれほど大きくなかった。
その要因としては、よく知られているように大幅なウォン安の恩恵が大きい。加えて、新興国においてスピーディーな量産体制を構築したことと、高い市場シェアを獲得していることも見逃せない。
スピードと量産性を最優先する北京現代の工場
具体的に中国の現地法人、北京現代汽車のケースを見よう。
工場は生産開始から3年目の2005年に30万台の生産能力を確保した。これは異例のスピードの拡張である。実生産台数も、3年目にして24万台近くと、急速に増やした(下図参照)。スピード重視(より速く)、量産性重視(より多く)は、現代自動車のものづくり文化をそのまま表している。
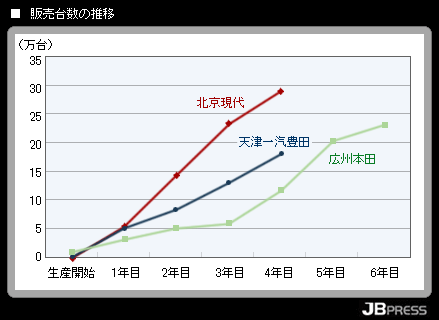
ものづくりの考え方も日本の自動車メーカーと大きく異なる。
例えば現代は、前工程にトラブルがあっても後工程を止めないために、工程間在庫(バッファー)を多めに持つ傾向がある。工程間在庫を最小限に抑えて、問題を顕在化することに重点を置く日本メーカーとは対照的な考え方である。
どちらかと言えば、現代は、「時間当たり生産台数(Unit Per Hour)」を増やすことを、「台数当たり生産工数(Hour Per Vehicle)」を減らすことよりも優先しているように見える。それゆえ、生産台数を上げるためならば、台数当たりの作業工数の増加もいとわない。
自動化に対する考え方も、日本企業とはかなり異なる。現代は、自動化が可能ならできる限り自動化するという考え方が強い。実際に現代北京工場の自動化率は、韓国国内工場と同じく高い。
中国の日系合弁工場は、20万台以上の量産工場でさえ、日本工場よりも自動化を抑えている。例を挙げれば、北京現代工場のスポット溶接はほぼ100%の自動化率を誇るが、日系の中国量産工場ではその半分程度である。
現代ではヒトより機械の方が信頼できるという考え方が強く、現場労働者を巻き込んだ問題発見・解決や、細かい改善の積み重ねというのは不得意である。そのため、品質問題の発見は検査員、その処置は管理者やそのスタッフというように分業方式となっている。
さらに現代は、部品の大胆なモジュール化も特徴的だ。運転席回りのコックピット、フロントエンド、シャシーなどをモジュール化し、外注している。しかもこれらは1社(現代モービス)にまとめて発注している。これは、他にはあまり例のないやり方である。