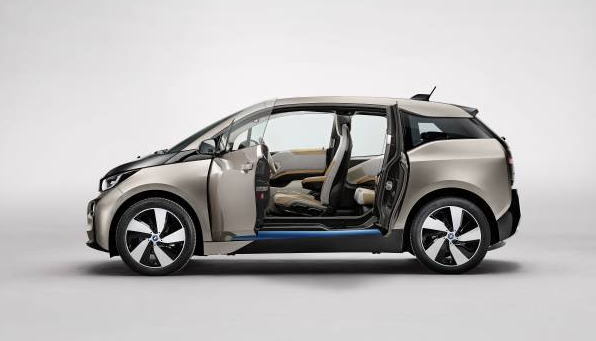
今回はBMWの電動駆動車両(EV)系列「iシリーズ」の中でもベーシックな4人乗りの「i3」を取り上げる。昨今の日本のクルマづくりとは対局にある発想、設計、そして動質が集積されていることを紹介しておきたいからだ。
i3を皮切りに立ち上げた「新動力システム搭載車両」の生産・市販開始にあたって、BMWは、その車体構造の主素材の1つとなるカーボンファイバーそのものから自分たちの手で製造することにした。そこで、同じドイツで炭素系素材メーカーを傘下に持つSGLグループとのジョイントベンチャーを立ち上げ、アメリカ・ワシントン州のモーゼスレイクに工場を建設している。その初期投資額は7200万ユーロとのこと。
常識的には、カーボンファイバーの素材そのもの、つまり糸や織物・組物は専門メーカーから購入して、そこから成形を始める。
この素材分野、特に「糸」に関しては東レ、東邦テナックス、三菱レイヨンの日本企業が世界シェアの過半を占めている。BMWがその「常識」を覆し、素材をつくる工場まで建設したはなぜなのか。カーボンファイバーのさらに原素材となる糸──それを「炭焼き」と同じように無酸素雰囲気の中で焼成することで炭素分子がつながった糸となる──は日本企業から購入している、とのことではあるのだが。
カーボンファイバーを主材にした車体(ボディ)の製造プロセスを紹介する写真を見て、さらに実車を観察して、C(カーボン)FRP(炭素繊維強化プラスチック)の車体を「量産」するという新しい挑戦にあたって「素材からつくる」ことを選んだBMWの発想と論理がやっと少し見えてきた。