本来のトヨタ生産方式を説くために始めた本コラム「本流トヨタ方式」は、現在「自働化」のお話を進めていて、今回はその7回目になります。
先回は、大野耐一氏がトヨタ(当時は「トヨタ自動車工業」)の機械工場で、「人の仕事と機械の仕事の分離」の改善を進め、「着・着工程」と言われる究極の姿を実現させた経緯をお話ししました。その改善によって、工場では最高で17台の機械を1人で受け持つことが可能になり、生産性は約10倍になったのです。
今回は、その大改革の実態をもう少し丁寧にお話ししたいと思います。有名な「ニの字ライン」はどのような考えで生まれたのか、そして、それが半世紀経った今、どんな曲がり角に来ているのかというお話です。
1950年、トヨタの工場で本格的な改革に着手した大野耐一氏の目には、トヨタの倒産の危機の元凶が、徒弟制度に基づいた職人集団任せのモノづくりにあり、それが「生産性の悪さ」と「膨大な在庫」を生んだと映っていたに違いありません。この体験が「作り過ぎのムダが一番悪い」という言葉になって今に伝わっています。
トヨタ再建のために1950年に新社長に就任した石田退三氏は、繊維産業独特の激しい好・不況の波をくぐり抜けてきた筋金入りの経営者でした。「在庫は借金と同じだ。少なければ少ない程良い」が口癖だったといいます。石田社長と大野氏の改革の方向は、完全に一致していたのでした。
作り方で生産性も在庫も変わる
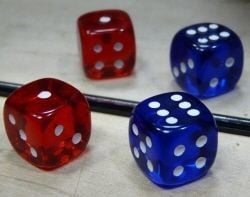
この時からトヨタの中でどのような改革が行われていったのかを説明します。皆さんがイメージしやすいように、金属の立方体に「目」を入れてサイコロを作る工程に例えてお話しします。
サイコロは、「目」の割り振りは、上を1にすると下が6、東を5にすると西が2、北が3、南が4、と決められています(写真1)。
この「目」は束ねて加工した方が効率的なので、図1にあるような4種類の専用加工機を使って凹形状に加工するとします。
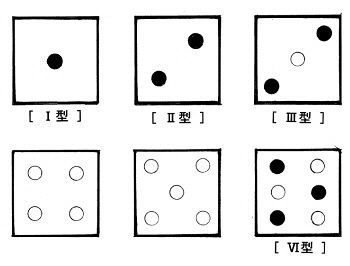
図の中の「●」が加工する部位を表し、それぞれの「目」は下のやり方で生産するとします。
1の目:[I型]
2の目:[II型]
3の目:[I型]⇒[III型]
4の目:[II型]⇒ 90度回転の[II型]
5の目:[I型]⇒[III型]⇒ 90度回転の[III型]
6の目:[VI型]⇒ 180度回転の[VI型]