多くの企業は、製品の設計だけではなく、不具合や欠陥を見つけるためにシミュレーションを使用してきた。現在では、製品開発と販売を終えた後でも、シミュレーションを活用するエンジニアが増えている。その利活用をさらに促進する新たなソリューションが、ANSYSの提唱する「デジタルツイン」となる。一般的に「デジタルツイン」は、デジタル上の製品レプリカを意味するが、ANSYSのデジタルツインは単に製品を複製した仮想データではなく、「デジタルツイン」をリアルタイムで動作させることで、製品性能をかつてない方法で可視化し、保守コストの低減や予測保守による製品の信頼性を高めることが出来る。
現場レベルで実際の活用が始まるデジタルツイン
ANSYSのエンジニアリング(工学)シミュレーションは、製品の大幅な性能向上や開発コストの削減、製品の市場投入期間の大幅な短縮などに貢献してきた。そのシミュレーションをさらに有効に活用する新たな取り組みが「デジタルツイン」になる。「デジタルツイン」では、物理空間にある現実の機器や設備の稼働状況、環境情報などをリアルタイムで収集し、仮想空間上に機器や設備を再現する。そして、これらのデジタル情報(モデル)を用いてシミュレーションを実施する仕組みだ。その結果、設計の改善や環境に応じた動作指示、さらには故障予測などを可能にするため、効率的な設計開発や運用管理コストの最適化などが期待されている。アンシス・ジャパン株式会社マーケティング部の柴田克久部長は、デジタルツインの活用について、次のように話す。
「デジタルツインのツインが意味する仮想モデルは、単なるプロトタイプではなく、実際に稼働している機器と瓜二つの双子のような存在だと考えています。IoTや最先端のセンサーテクノロジーを組み合わせることで、仮想空間にあるシミュレーションモデルが、実機と同じように理想的な相似モデルを実現するのです」
機器に取り付けられた各種のセンサーからリアルタイムでデータを収集できるIoT技術の進化は、実環境に存在し動作している製品とシミュレーションの統合を可能にする。例えば、現場で稼働しているポンプにセンサーを取り付け、その稼働状況をリアルタイムでシミュレーションモデルと連動させることで、エンジニアが現場に出向かなくても、診断や予測が可能な「デジタルツイン」で評価できるようになる。
最近では、機械学習やディープラーニングといったAIを用いてデータを統計的に分析し、異常値を検出するという取り組みもみられるが、AIではなぜそれが起こるのかといった原因を知ることは難しいだろう。デジタルツインであれば、現実の世界にある実機から測定したデータを用いてシミュレーションを行うので、どのような状況下で異常値が生じるのかということを分析できる。
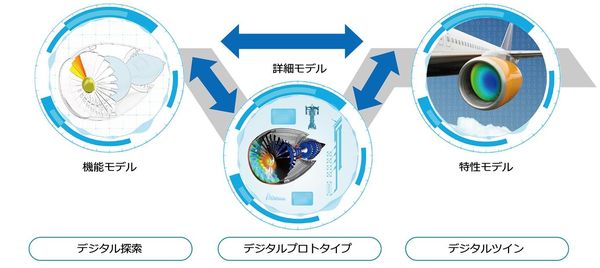
シミュレーションを超えるデジタルツインの革新性
「デジタルツイン」の実現は、運用・保守の最適化だけではなく、新製品の開発プロセスの大幅な迅速化も図ることが可能になり、企業にとって価値創造における革新的な時代の幕開けをもたらす。ANSYSシミュレーションのプラットフォームを使用すると、エンジニアは起こりうるすべての入力と動作条件を仮想環境で評価できるようになる。システム全体をモデル化して、実際の機器に取り付けたライブセンサーからデータを組込み、デジタルツインで問題を仮想的に再現することで、リアルタイムに近い環境を作成できるのだ。「デジタルツイン」を離れた場所で操作できるようになれば、原因の特定と分析が迅速になり、故障や異常が発生したときにも、修正処理の提案と検証が容易になる。
さらに、シミュレーションにより、目に見えない気体の流れや熱の分布、あるいは計測できない機器内部の温度や構造的な欠陥を把握することが可能になり、異常が検出された場合にシステムモデルからデータを取得し、オンプレミスのデータセンターやクラウドに送信することも出来る。よって、保守担当のエンジニアが瞬時に状況を確認したり、実際に装置を使って試すことなくシミュレーションを用いて安全に対応方法を試すことが可能になる。つまり、「デジタルツイン」を使用すれば、風力発電や海洋探査機といった、遠隔地に置かれた製品について、現地に出向くことや、実機を分解することなく、診断や徹底した根本原因を分析できるようになるのだ。
柴田氏は「ANSYSシミュレーションのプラットフォームによる3Dシミュレーションを活用して、異常の根本原因が特定できます。デジタルツインは、動作検証と将来の最適化という両方の用途に活用できるため、実機で試験することなく、what-ifシナリオを実行できます。そこで、システムモデルの修正処理を評価するユーザーが、高度な3Dオンデマンドシミュレーションを使用して、実際の製品に生じる問題を修正できるのです」と話す。
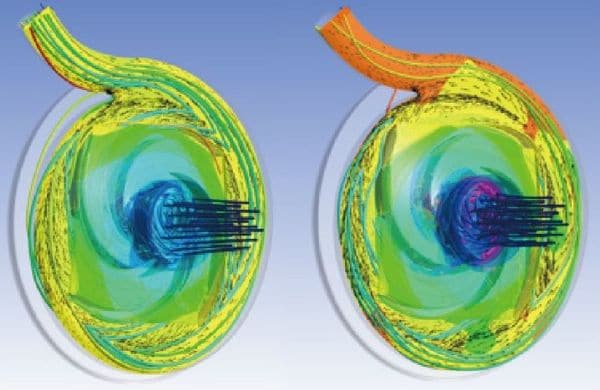
ANSYSが提唱する次世代のPervasive Engineering Simulation
ANSYSは、実際に使用されている製品の環境や使用状況をデータとして吸い上げ、高精度な3次元シミュレーションを行った結果を用いてバーチャルで「デジタルツイン」を構築する。「デジタルツイン」をテストデータやリアルタイムデータに接続するためにPTC社が提供するIIoTプラットフォームと統合させ、ユーザーフレンドリーなGUIにより保守担当者が瞬時に状況を判断して対応したり、計算時間のかかる3Dシミュレーションから計算を高速化するために次元を落とした1Dモデル(縮退モデル)を自動で作成することで、保守担当のエンジニアが瞬時に状況を確認したり、実際に装置を使わずに対応方法を試したりといったことが可能になる。
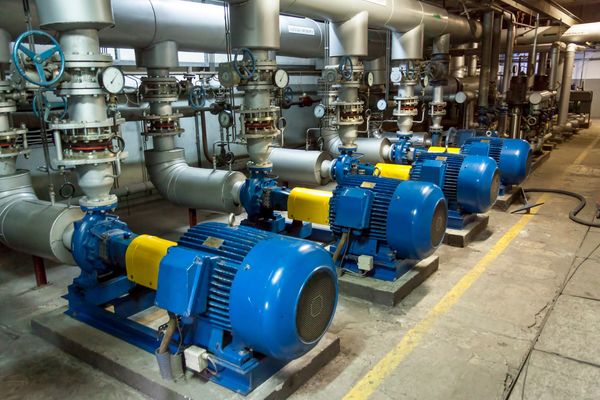
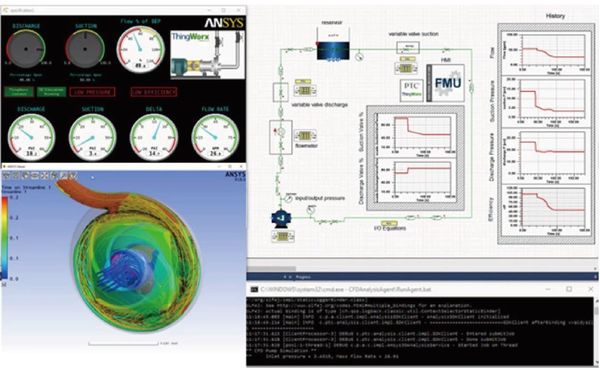
ANSYSは、デジタル技術による変革を促進するために、次世代のPervasive Engineering Simulation(エンジニアリング シミュレーションの活用拡大)を提唱している。柴田氏は「ANSYSは、シミュレーション技術の精度や応用範囲を拡大するために、半導体やマテリアルに電子基板などに特化した企業を買収しています。デジタルの精度が今後もさらに向上していけば、より広範囲に設計や製造の現場でエンジニアリングシミュレーションが活用されるでしょう。製造業におけるデジタルトランスフォーメーション(DX)の波は、すでに押し寄せています。今後の設計における最適化も、シミュレーションで得られた知見を優先する流れは加速すると思います。そして、材料の調達においても、シミュレーションデータの有無が優先されるようになるでしょう」と話す。
ANSYSの提唱する「デジタルツイン」は、製造業のデジタル変革を象徴する最先端のテクノロジーであり、次世代のPervasive Engineering Simulationの可能性を見出していくだろう。
■アンシス・ジャパンのデジタルツインに関する取り組み・活用例の詳細はこちら
【関連記事】
■ANSYSの電動化シミュレーション環境が新たな電動化の未来を拓く
〜新記録を樹立したVolkswagen Motorsport社の電動レースカーの開発をサポート〜
■自動運転技術の開発を加速するANSYSのシミュレーションツールチェーン
年間60万人の命を救う自動運転―その開発と競争力の向上に貢献
<PR>