ものづくりに革新をもたらす3Dプリンターだが、国内でも自動車、工業、医療の分野で活用が進み、本格的な普及期を迎えつつあるようだ。一方で、3Dプリンターの生産現場での導入には、検討開始から開発、最適化、量産までのプロセスがあり、一朝一夕にいかないのも事実だ。3Dプリンターメーカーとして、グローバルにビジネスを展開する日本HP 3Dプリンティング事業部・エンタープライズアカウントマネージャーの阿部 英之氏に製造業における課題と活用事例、同社が提供するソリューションサービスなどについて聞いた。
製造業の課題を解決する3Dプリンターの活用
「HPが昨年実施したグローバル市場調査によると、3DプリンターをはじめIT情報を駆使したデジタルマニュファクチャリングに対して、多くの製造業が高い関心を示していました。また、製造業の中でも自動車、工業、医療などを中心に3Dプリンターの活用が進んでいることも明らかになりました」。こう切り出したのは、日本HP 3Dプリンティング事業部・エンタープライズアカウントマネージャーの阿部 英之氏だ。
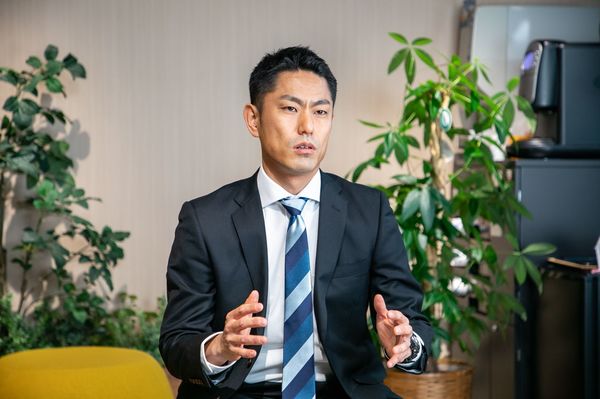
阿部 英之 氏
HPには、パソコンとプリンターという大きく2つの製品カテゴリーがあり、さらにプリンターの中に、個人向けプリンターや法人向けプリンター、大判プリンター、デジタル印刷機、そして3Dプリンターがラインアップされている。
「海外で製造した3Dプリンター機を輸入し、国内のお客様に販売するのが、われわれ3Dプリンティング事業部の主な業務です。お客様は圧倒的に製造業が多いのですが、最近では、例えば国内大手アパート・マンションデベロッパーが建築前のマンション模型を造形するなど、製造業以外での活用も見受けられるようになりました」と阿部氏は話す。
なぜ製造業において、3Dプリンターの活用が進んでいるのか。3Dプリンターの活用を通じて、どのような課題解決につながっているのだろうか。阿部氏は次のように説明する。「3Dプリンター活用の大きな目的の1つに、試作品づくりが挙げられます。自動車をはじめ製造業全般において、従来以上にスピード感が求められる中で、例えば、設計から試作、評価までを1カ月以内に行わなければならないといったケースも珍しくなく、従来の工法では物理的に不可能です。一方、当社の3Dプリンターでは約2日、48時間以内に機能的な試作品をつくることができるので、そうした短納期への対応も十分可能です」。
試作品づくりや治具の製造で活用が進む
国内における試作品づくりの活用事例を紹介しよう。大手電機メーカーA社では、高い生産性や他の3Dプリント方式と比較した際の後処理の容易さなどを評価し、HPの「Jet Fusion 5200 3Dプリンティングソリューション」を採用。業務用空調設備向けのパーツの試作と機能試験に活用している。これによって、より早くパーツを社内で検証できる体制を確立することにもつながった。
先述の国内大手アパート・マンションデベロッパーは、建設前のマンション模型をフルカラーで造形することにより、社内外でイメージを円滑に共有することができるようになった。高強度のナイロン材料を使用することで、耐久性への不安が最小限となり、営業担当者がマンション模型を積極的に社外に持ち出せるようにもなったという。
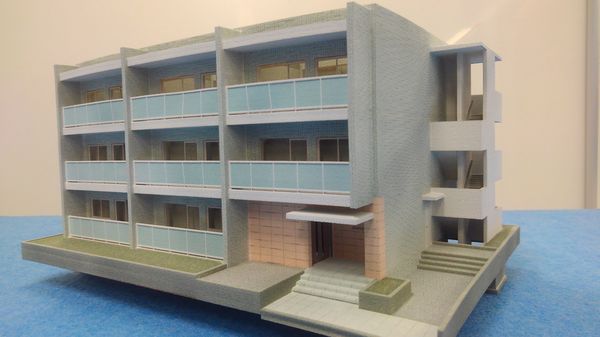
試作品に続いて多い用途が、治具(じぐ)だ。治具とは、部品を加工する際に、部品を固定したり、作業のガイドになるもの。デンマークの航空機部品・サービス会社のサタイア社は、HPのカラー3Dプリンターで高強度、高品質なフルカラーの治工具を提供することで、リードタイムの短縮とコスト削減を実現。従来はパーツに塗装していたが、カラーパーツに切り替えることで、納品までのプロセスを削減することができた。
フランスの工作機械メーカー、セブオートモティスム社では、ロボットアームの造形にHPのカラー3Dプリンターをフル活用している。色情報の付加によって作業効率を改善させるだけでなく、社内で内製する体制を整備できたことにより、継続的な治具の改善活動が可能になった。
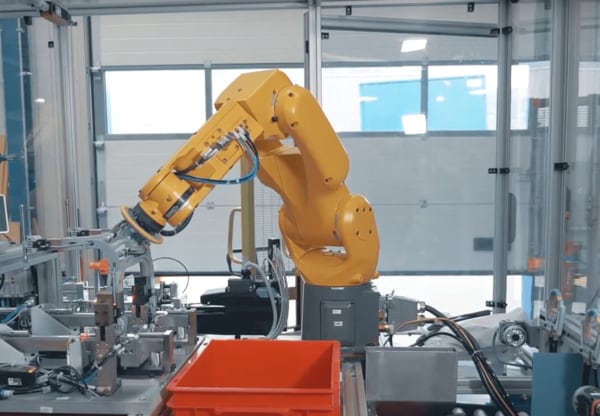
パソコン、プリンター事業に
培ったノウハウが活きる
HPの3Dプリンティング事業における強みは、パソコン事業やプリンター事業などで培ったものづくりの経験、部品設計のノウハウだと阿部氏は言う。「ものづくりには、部品設計が不可欠です。こういうサイズに収めるには、あるいはこういう強度にするには、どのような形状がいいのか、といった部品単位でのものづくりの経験を3Dプリンター以外の領域でも長年にわたり蓄積してきたことはメーカーとしての大きな強みであり、競合他社との差別化要因にもなっています」。
グローバル企業として世界各地に営業拠点と開発拠点を持ち、さまざまな知見やリソースを共有できる点もHPの強みと言えるだろう。「海外のスタッフに、『こういった事例はないか』と尋ねると、どこかの国のスタッフが何らかの回答を持っていて、世界中からサポートを受けることができるため、非常に仕事がしやすいと感じています」と阿部氏は話す。
自社のグローバルネットワークに限らず、ソフトウエア企業や材料メーカー、3Dプリンターでの造形を受託するサービスビューロー(造形受託パートナー)など、さまざまな業種のパートナー企業とエコシステムを形成し、総合的にソリューション提供していける点もHPならではの優位性と言っていい。
3Dプリンターそのものの特長についても追記しておきたい。2Dの印刷機や大判印刷機の技術を活かして、「Multi Jet Fusionテクノロジー」という独自の造形方式を採用している。わかりやすく言うと、造形エリアに材料の粉末を敷きつめ、その上から「エージェント」と呼ばれる特殊なインクを噴射する。ほぼ同時にハロゲンランプで熱エネルギ―を与えることでインクが熱を吸収し、周辺の粉末を溶融・硬化させていくもの。これによって、サポート構造が不要な高い設計の自由度が得られるほか、水平方向と垂直方向で同等の強度を実現したり、試作品の製造だけでなく最終製品の量産も可能だ。
今後は補修部品の領域で拡大が見込まれる
今後、どのような領域で3Dプリンターの活用が拡大していくのだろうか。阿部氏は有望な領域の1つとして、補修部品(サービス部品)を挙げる。直近3月にも、同領域に関連するニュースが発表されたばかりだ。それによると、自動車産業を中心に3D CAD/CAEエンジニアリングサービスを提供するSOLIZEは日本HPと共同で、日産自動車の生産終了となったヘリテージ車両の補修部品「NISMOヘリテージパーツ」を、HPの3Dプリンターで復刻生産する。その第1弾として復刻生産されたのが、R32型スカイラインGT-Rのハーネス用プロテクター(樹脂部品)である。
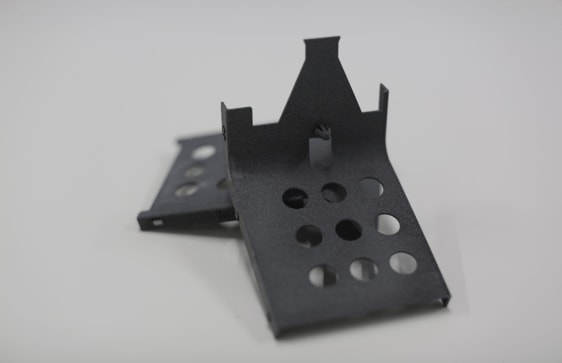
こうした補修部品は、量産時にはある程度、低価格でサプライヤーからメーカーに納めることが可能だが、量産終了後は、当時と同じ価格で納めることがコスト的には非常に厳しい。
一方でサプライヤーも量産終了後、一定期間は補修部品を製造する金型を保管しておく必要がある。サプライヤーによっては、数千~数万点にものぼる補修部品の金型を10~20年も保管しておくことは、倉庫スペースを含め相応のコストがかかることになる。
そこで、数量はあまり出ないが、メーカーやサプライヤーの責任として、期間に捉われず、補修部品を製造する体制を可能にするのが、3Dプリンターなのである。「金型を廃棄し、データで保管し、3Dプリンターに置き換えると、サプライヤーとしては金型の保管費や更新費用が掛からないので、トータルのコスト面で抑えることが可能となります。金型がすでになくなってしまった、20年以上前の古い部品等も復刻生産という形で、最終消費者にとっても恩恵があり、補修部品の領域で3Dプリンターの活用が進むと思います」。高額消費財であり、耐久消費財でもある自動車をはじめ、家電などでも、補修部品のニーズはあると阿部氏は見込んでいる。
HPはグローバル市場において、3Dプリンターの検討から、開発、最適化、量産まで、デジタルマニュファクチャリングのプロセスを一貫してサポートする「プロフェッショナルサービス」の提供に注力していくとしており、日本でも自動車産業を中心に製造業や医療分野をターゲットに同様の戦略を実行していく方針だ。
「3Dプリンターを導入するお客様は、大きく分けて2種類に分かれます。1つには、自社で設備を導入して、社内で使うお客様。もう1つは、設備を導入して、他のお客様のために部品を製造して提供する、サプライヤーです。部品を製造・販売するサプライヤーに対しても、われわれは手厚く支援していきたい」。阿部氏はこう意気込みを示す。
現時点で使用可能な材料はナイロン樹脂だが、今年の夏以降、プラスチック材料のポリプロピレンが新たに加わる予定だ。造形後の粉の除去と払い出しを自動で行う、「製品自動取り出し機(Auto Unpacking Station)」のリリースも年内の予定で、3Dプリンターに関する日本HPの動向に今後も注目していきたい。
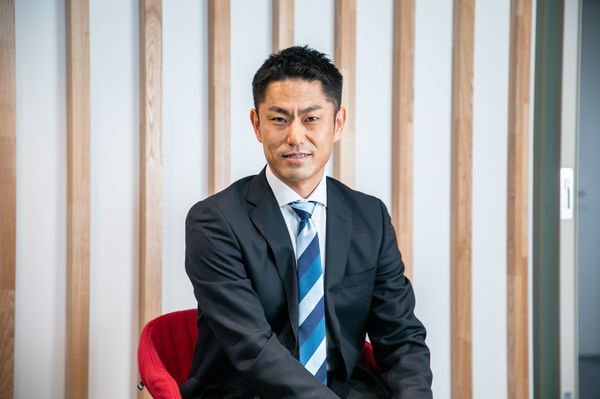
<PR>