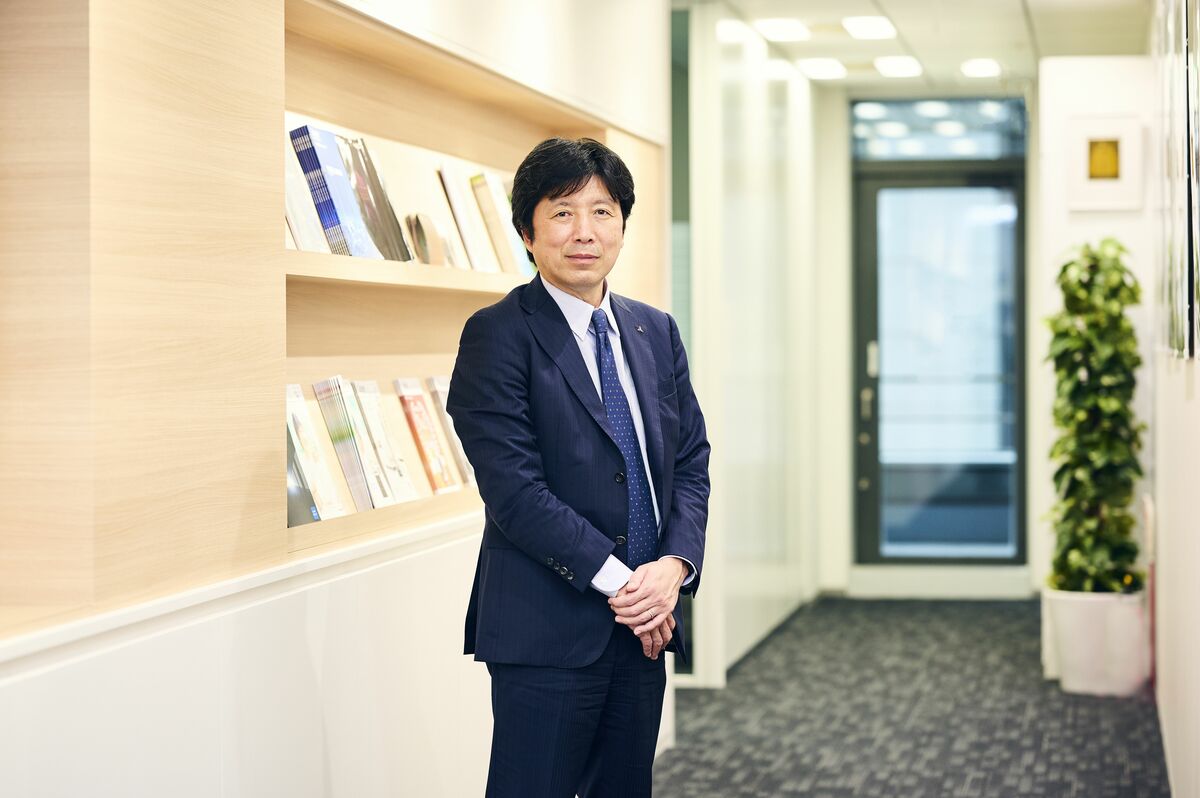
「循環型 デジタル・エンジニアリング企業」をビジョンに掲げ、総合ソリューション事業の強化を進める三菱電機。主力の一つ、FA事業においても長年に渡って培ってきたFAの技術力や提案力、高度な製品開発技術を活用し、現場起点のDXで製造サイクル全体の最適化を支援している。実際、DXによってFA事業をどう進化させ、社会や顧客にどのような価値を提供しているのか。同社常務執行役でFAシステム事業本部長の武田聡氏に聞いた。
日本の製造業が、国際マーケットで競争力を維持していくためにはDXをはじめとしたイノベーションの実現が必須です。本特集では、設計・開発業務のデジタル化やスマートファクトリーの推進、脱炭素社会の実現に向けた取り組みなど、ポストコロナ時代に加速した製造業イノベーションの最新事例に迫ります。
フォローしたコンテンツは、マイページから簡単に確認できるようになります。
ものづくりのデータを一つのプラットフォームで集中管理
――三菱電機が新たなビジョンとして掲げる「循環型 デジタル・エンジニアリング企業」の下、FA事業ではどのような取り組みを行っていますか。
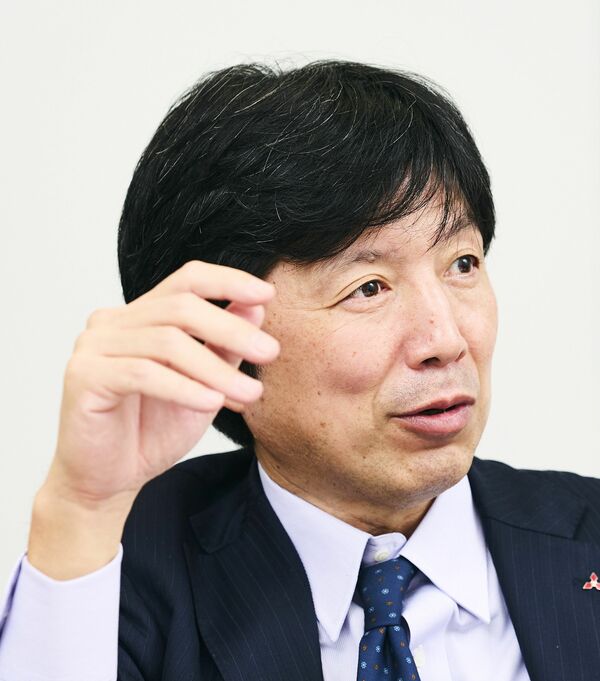
1989年4月、三菱電機に入社。名古屋製作所副所長、FA海外事業部長、FAシステム業務部長を経て、2022年4月に同社常務執行役、インダストリー・モビリティビジネスエリア オーナー(FAシステム事業担当)、現在に至る。
-----
座右の銘・好きな言葉:「スピード」「アジャイル開発」
DXで注目の企業・人物:Netflix、セールスフォース
お薦めの書籍:『NO RULES 世界一「自由」な会社、NETFLIX』(リード・ヘイスティングス、エリン・メイヤー著)、『TRAILBLAZER(トレイルブレイザー) 企業が本気で社会を変える10の思考』(マーク・ベニオフ著)
武田聡氏(以下敬称略) 当社のFAの技術力と、FAとITをつなぐ連携技術を最大限に活用し、あらゆる機器や設備をIoTでつなぎ、データを収集・分析・活用することで、製造サイクル全体を最適化する支援を行っています。
ものづくりの現場を例にすると、工場を中心に前工程には製品設計や生産計画などがあり、後工程には物流、保守・運用などがあります。こうしたサプライチェーンとエンジニアリングチェーンがデータを共有することで、新たなソリューションの創出に取り組んでいます。
具体的には、デジタル上にリアル空間を再現した「デジタルツイン」を構築し、IoTで現実空間から収集したデータを基に、AIが分析やシミュレーションを実施します。効率的な製造プロセスや適切なメンテナンスなどを導き出し、それを現実空間にフィードバックすることで、製造サイクル全体の最適化を図ることができます。
このように、設計・生産・顧客データなど、ものづくりのデータを一つのプラットフォームで集中管理することにより、製造サイクル全体の効率化を一気通貫で行うわけです。
――三菱電機のFAはデジタル技術の進展とともに進化し続けていますが、現在はどのような特徴がありますか。
武田 機械装置が壊れたり、アラームが出た後ではなく、その前の段階からサポートし、開発・生産・保守などにおけるコスト削減のお手伝いをしています。例えば、これまでは機械装置を完成させるまでに何度も試作や現場での調整、プログラムの修正を繰り返す必要があり、大きなコスト負担になっていました。それがデジタルツインでは、製造現場を再現したデジタル空間で機械装置の動きを再現し、プログラムを修正しながら完成に近づけることが可能です。トライ&エラーが容易なため、試作を低コストで繰り返すことができます。
製造ラインの稼働後は、IoTデバイスから取得したデータをデジタルツイン上に反映し、AIによる異常予測機能を用いて重大な故障を未然に防ぐこともできます。機械装置に不具合が発生したときには、デジタルツインのシミュレーションデータと画像、製造現場のデータを照らし合わせることで、原因を素早く特定できます。
最近はカーボンニュートラルの達成が企業の課題になっていますが、全ての製造プロセスにおけるエネルギー消費量とCO2排出量を一元管理できますから、その実現にも役立ちます。機械装置の運用条件の変更や省エネ機器・装置の導入などによるエネルギー使用量削減効果をデジタルツイン上で検証し、最大限の効果が得られる方法を提案しています。
製造現場から収集した膨大なデータを基に、デジタルツイン上でAIが分析やシミュレーションを繰り返し、そのソリューションを現場にフィードバックしていく。こうした循環型の仕組みで改善を重ねています。