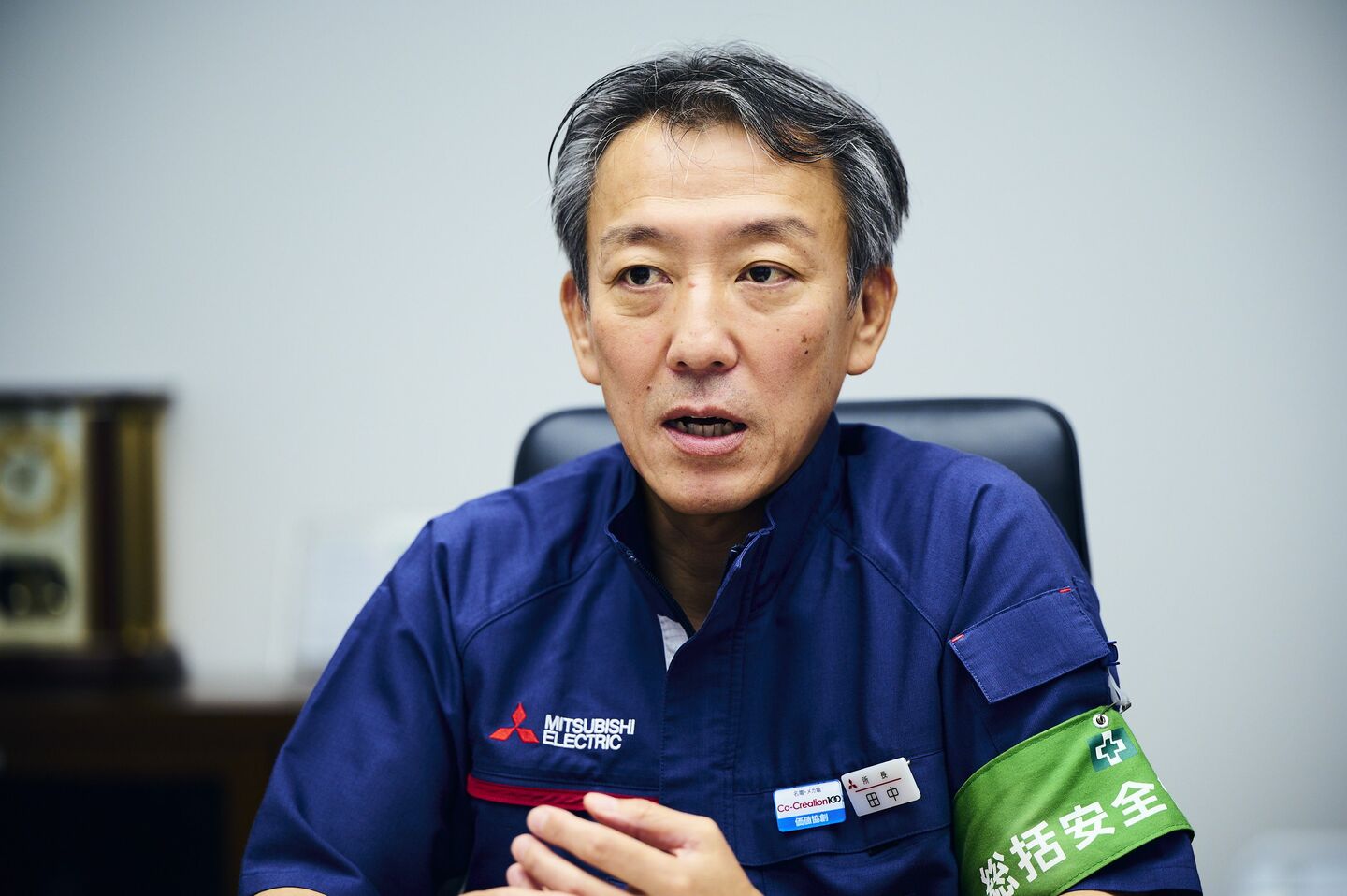
三菱電機の中で、FA事業における中核工場の役割を担う名古屋製作所は、同社が推進する工場のデジタル化、データ活用ソリューションである「e-F@ctory」の実践拠点でもある。多品種変量生産の時代に重要度を増す製造業におけるデジタル化の現状と、デジタル時代の工場における「人」の役割について聞いた。
■【前編】三菱電機のものづくりを支える名古屋製作所 田中貴久所長が語る、グループ工場の「親」として果たす責任
■【後編】三菱電機の“FA中核工場”名古屋製作所長に聞く、デジタル工場でもなお「無人」にはならない理由(今回)
時代の要請に応える「e-F@ctory」ソリューションを推進
――ものづくりの工程や社会システムの運用において、デジタル空間でシミュレーションを行う「デジタルツイン」の考えが注目されています。今、工場のデジタル化はどこまで進展しているのでしょうか。
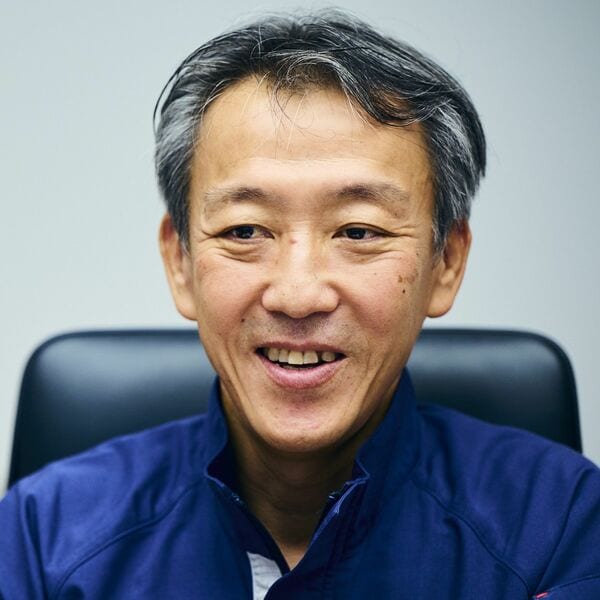
自動車部品メーカーでカーナビゲーションのソフトウエア開発に携わった後、1997年に三菱電機入社。工作機械メーカー、自動車業界向けメーカー支援などのチームを経て、ハードウエア、ソフトウエア開発、品質管理部門の管理職を歴任。2021年産業メカトロニクス製作所所長。2024年から現職。
田中貴久氏(以下・敬称略) 多品種変量生産の時代になり、生産設備を早く立ち上げなくてはいけない、また段取り替えを早くしなくてはいけないというニーズが急増しています。事前のシミュレーションは、もはや必須といってもいい状況です。
生産現場におけるシミュレーションの考え方は、かなり以前から存在していて、徐々に採用されていたのですが、ここ数年のデジタル技術の進展に伴い、一気に進んだ感があります。
これには、製造業の産業形態が変わってきていることも関係しています。かつては、自社の製品は自社の工場で作って、お客さまに届ける形が当たり前でした。そこにEMS(Electronics Manufacturing Service:電子機器受託製造)という形態で、製造に特化した第三者の企業が、さまざまな企業の製品をまとめて生産するビジネスモデルが登場しました。
当社のようなFAのメーカーは、EMSの企業に製品を納品することも増えていますが、彼らは生産の効率を上げるために、シミュレーションの技術に特に力を入れています。
――名古屋製作所では、シミュレーションなどデジタルの活用をいつごろから始めていますか。
田中 名古屋製作所では、2003年ごろからデータ活用の取り組みを始めています。当時はデジタルとは呼んでおらず、生産現場の改善活動がその出発点でした。生産管理部門から、当社が手掛けるシーケンサやサーボなどの生産ラインから出てくるデータを分析すれば、生産の改善ができるのではないかという発想が、活動の原点です。
全てのデータを集めると、「この生産設備の歩留まりがおかしい」「機器の能力のバランスがよくない」といったことが見えてきました。場合によっては、製品の設計に問題があるから、ここを少し変えた方がいいというように、生産ラインだけでなく、上流工程の改善にもアドバイスができることがあります。
この活動が発展して、IoTのデータを用いてデータを前工程にフィードバックさせることで、生産性を改善し、工場全体のデジタルツイン(※)を実現する「e-F@ctory」(イーファクトリー)が生まれました。e-F@ctoryは現在、三菱電機のFA-IT統合ソリューションとして、お客さまに提供しています。
※デジタルツイン:現実世界にある製品や機器の情報をデジタル空間に送ることで、現実世界と同様の製品や機器をデジタル空間上に再現すること。