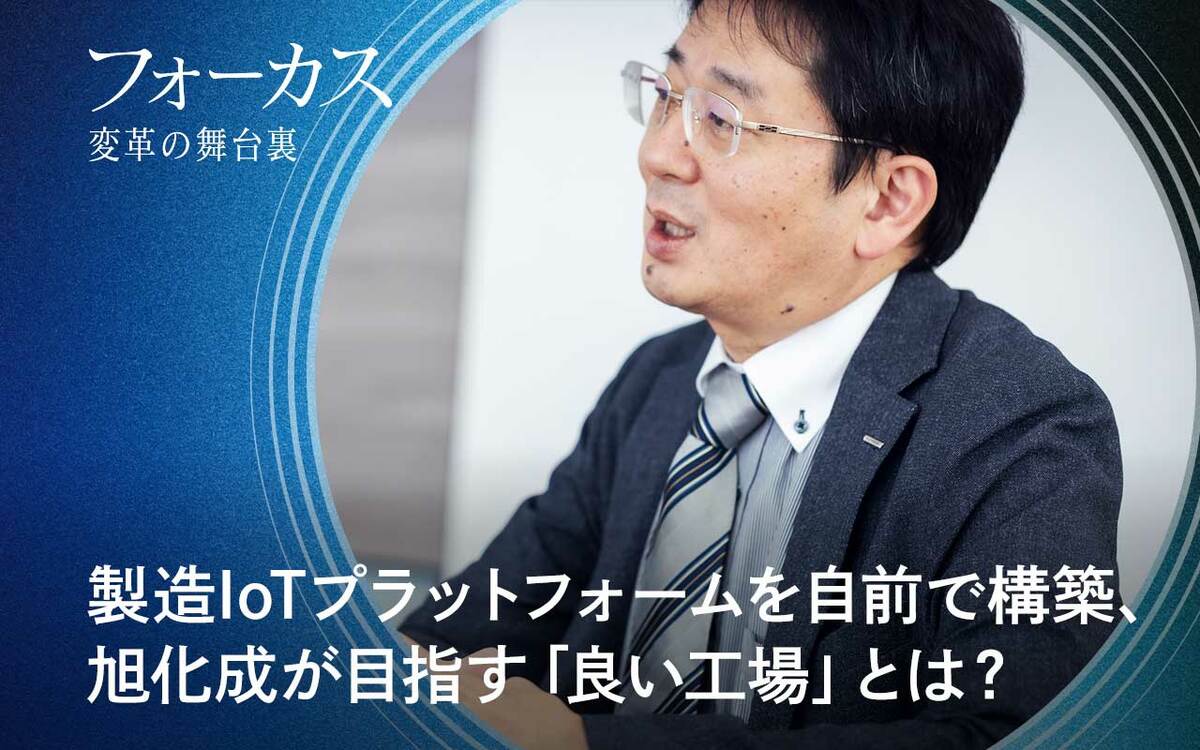
日本経済の競争力の源泉となってきたのが、ものづくりの現場だ。今も品質や生産性の向上が常に目指されているのはもちろんだが、温室効果ガスとされる二酸化炭素の排出削減や、労働人口減少への対応といった課題も立ちふさがる。マテリアル、住宅、ヘルスケアの3つの事業領域をもつ旭化成は、国内外拠点での「工場の革新」が課題となっている。今回は、同社がデジタル共創本部に設置したスマートファクトリー推進センターの取り組みを紹介する。
データ駆動型の工場へ、データ分析で課題の原因を特定
デジタル技術の活用によってプロセス全体の変革や生産性向上を図った工場を「スマートファクトリー」と呼ぶ。
「スマートファクトリーに対する工場の人たちの反応は、積極的であったり、さほどでなかったりと、様々です。そうしたいろいろな考えのある人たちに、『工場を良くして課題を解決したいという気持ちは皆さん同じですよね』と話しかけ、工場の革新を進めているところです」
こう話すのは、スマートファクトリー推進センターの中山雅彦センター長。1991年に旭化成工業(現・旭化成)に入社し、以降、旭化成グループ内向けの情報通信技術やデジタル技術の活用領域に携わってきた。現在では拠点同士をつないで従業員がオンライン会議をするのは日常的となったが、電話・通信にデジタル回線のはしりであるISDNが使われていた時代、宮崎県の延岡支社と、静岡県の富士支社の両工場をつないで画像検査機の検査画像を伝送し、検査の状況を遠隔から即座に把握するといった取り組みもした。
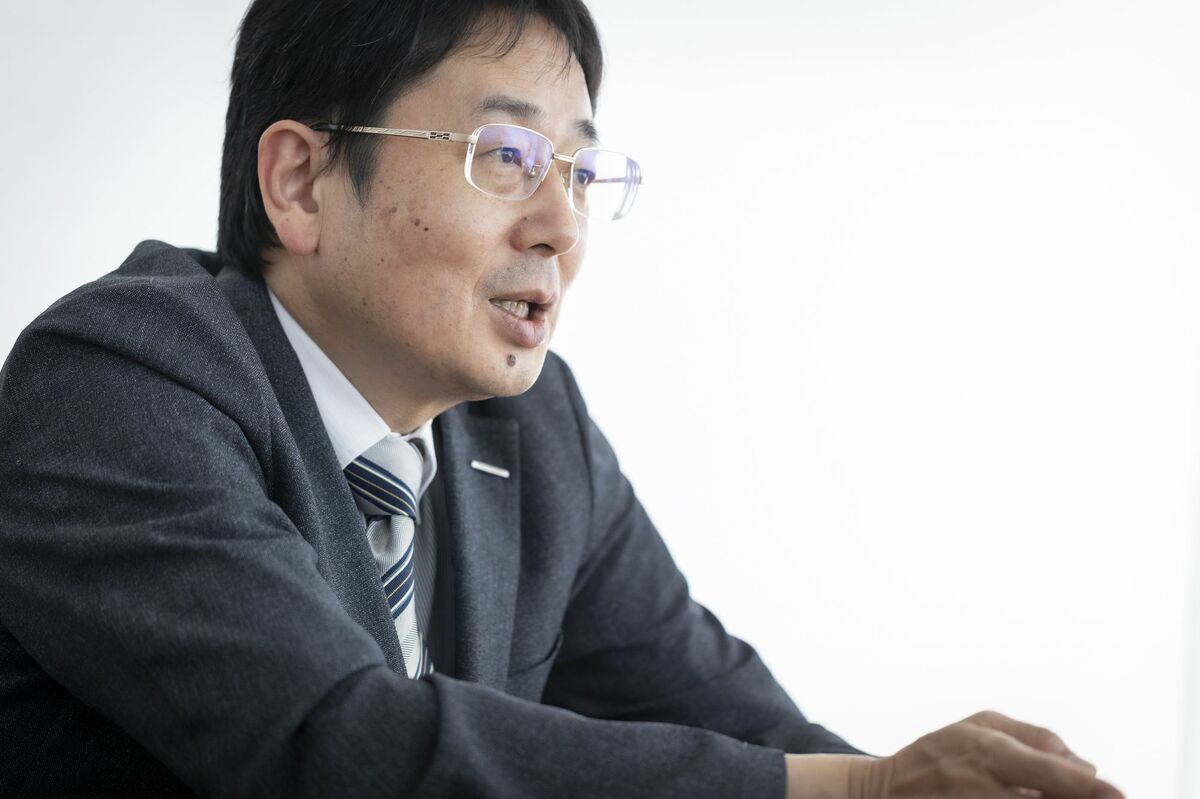
工場をより良くして課題の解決を図っていく。そのために共通的な手だてとなっているが、「データ駆動型の製造」を推進することだ。中山氏が挙げる事例に、「繊維毛羽(けば)品質向上」がある。「コストダウンという課題もありますが、現在は品質の安定化や収率の向上を目指しており、結果コストダウンにつながればと考えています」。