変化に対する対処法やルールが不明瞭で、その場対応が多い
理由としては、主に以下の3点が考えられる。
1つ目は、販売計画情報の精度に対して、生産計画のタイミングが早すぎることである。生産計画のタイミングは、生産リードタイムや生産能力の余裕度に基づき設定すべきであるが、その実力値を把握できず、安全を見て早めに計画立案しているケースをよく目にする。
2つ目は、計画の見直しルールがはっきりしていないことである。需要動向の変化や確度に基づき、定期的に計画を見直すことで変化に対応できるようになる。
3つ目は、計画の優先順位が不明確になっていることである。目の前で発生している問題に振り回されてしまい、都度対応が発生してしまう。
段階的生産計画と優先順位ルールの明確化で効率的な生産を実現
生産計画では、需要予測や営業情報(受注・引合い)に基づいて生産量と時期を「経済的」かつ「需要変動や仕様変更等」に対応し、かつ「弾力性」を持たせるために、段階的に生産計画を立案するとよい。
一度の計画で長期間の生産計画を固定すると設備、要員、資材、資金(4M)の固定ができコントロールしやすくなるが、現実には需要変動や現場トラブルなどの変化要因で実際との乖離(かいり)がおきてしまう。その結果として、需要と生産量がアンバランスになり、不足が発生すれば機会損失を、過剰になれば在庫のムダを生むことになる。これらのバランスを考慮するため、4Mの準備、手配、実行のタイミングに合わせ各計画の期間やサイクルおよび単位が決められるべきである。
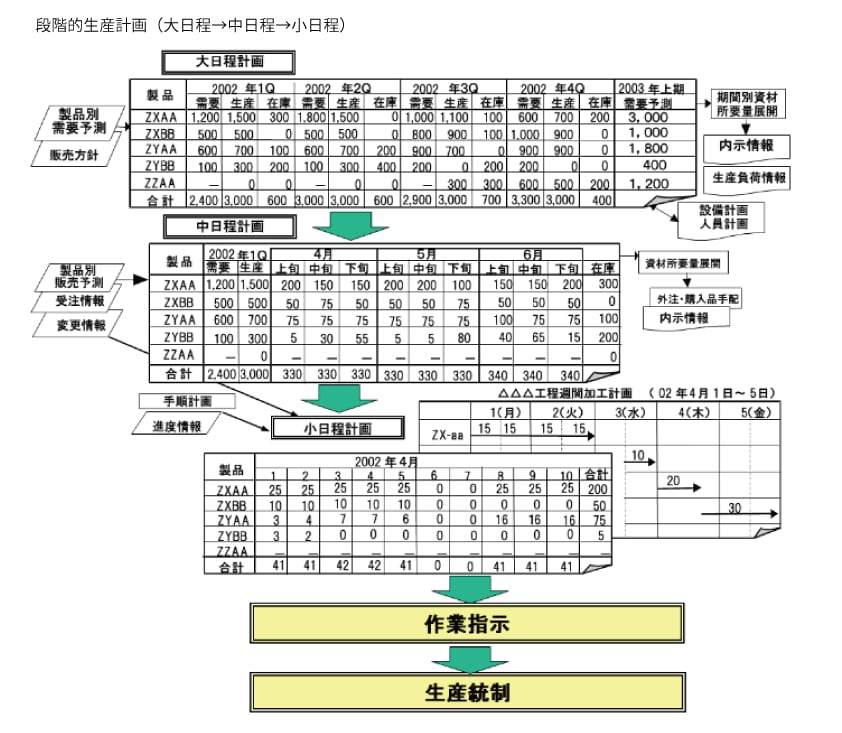
生産計画は一般的に
・年次生産計画
・月次生産計画、週次生産計画
・日別生産計画
といったように計画する期間の大きさによって分けられる。このような期間計画は見込み生産形態に多く用いられる。
受注生産形態においてはこれらにあたる計画は
・大日程計画
・中日程計画
・小日程計画
と呼ばれることが多い。
年次生産計画は販売計画をもとに1年間の生産量を月別に決める。この計画では、毎月の生産量を確定するというよりも、工場の操業度や内外作の割り振り、在庫をどれだけ持つか、必要となる人員や設備能力といった生産に必要となるリソースの計画を行うことが主たる目的となる。
月次生産計画あるいは週次生産計画はその期間にどのタイミングでどの製品をどれだけ作るかを計画し、それに必要な人員や材料の計画を行う。一般的にはこの段階で生産量が確定されることが多い。
日別生産計画は日々の製品別生産量と生産スケジュールの確定を行う。これにより必要な材料等の手配と製造現場に対しての作業指示を行う。
このように、段階的に生産計画を確定させることで、変化への対応と効率性、安定生産を両立させることができる。
また、各計画を立案する際にも、直近の期間計画だけではなく、翌期間以降の内示や予定情報の提示を行い、ローリングさせることで変化の準備も行いやすくなる。
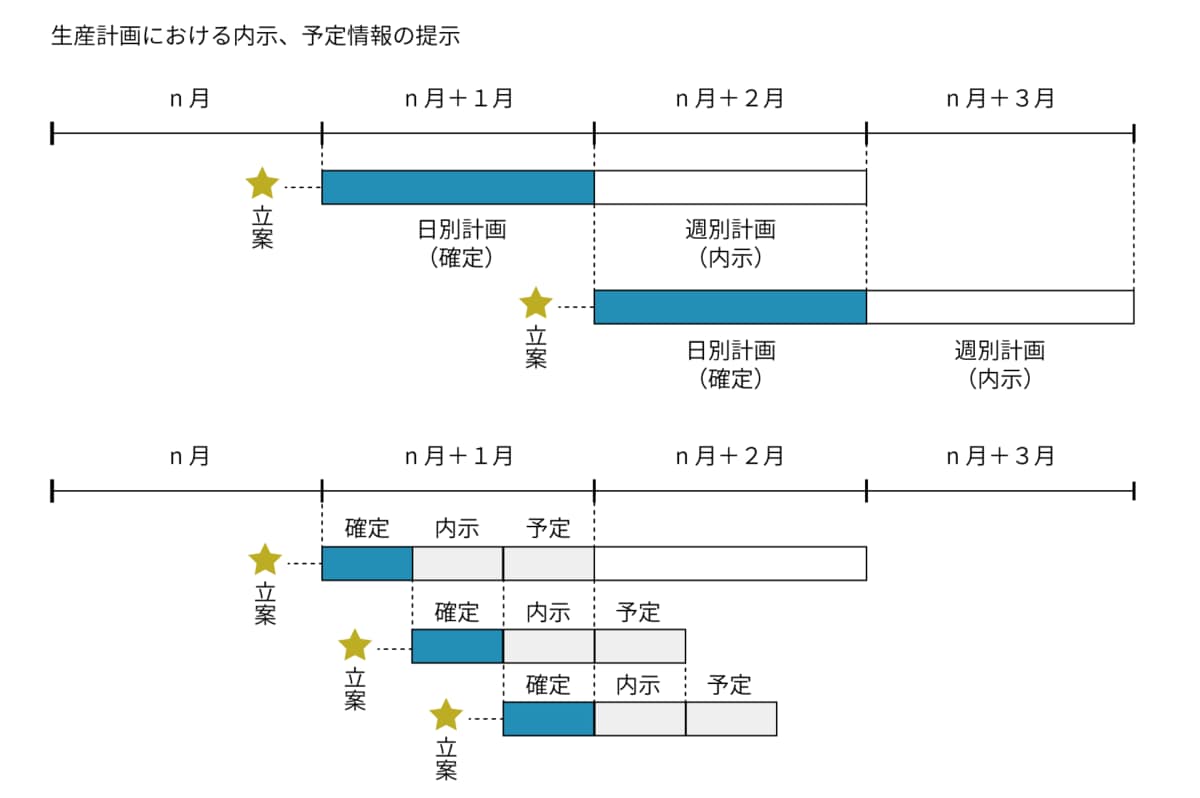
最後に、優先順位については、ルールを明確にしておくことが大切である。基本的には、段階的生産計画の各段階において、最終的に確定させた項目については変更をせず、変更可能なタイミングの明示と関係者へのアナウンスを行うなどして、受け身の対応から能動的なアクションに変えることがとても重要である。
① 在庫切れ確度の高いもの
② 作業の加工時間の少ないもの
③ 仕事の到着順番の早いもの
④ 仕事の残時間の多いもの
⑤ 仕事の残工程の多いもの
⑥ 仕事の残時間の少ないもの
⑦ 仕事の残時間を残工程数で割った比率の高い
⑧ 段取回数・時間最小になる組み合わせのもの
・ 品種切替最小パターンの適用
・ タイムパケット内の同一品種(品目)寄せ
⑨ 顧客によるもの
⑩ 作業の手持ちロスの少ないもの など
変更の影響度を小さくするために、特急枠の設定、指定席予約枠の設定などの変化対応用の枠取りや在庫状況の可視化による優先順位の明確化など、会社としてのルールを整備し仕組み化することが望ましい。

コンサルタント 茂木 龍哉 (もぎ たつや)
SX事業本部
シニア・コンサルタント
生産、物流機能領域を中心に、サプライチェーンマネジメントの視点から、在庫適正化、生産管理システム導入、コストダウン等のコンサルティングを行う。また、製造業の人材育成にも積極的に取り組んでおり、自律的継続的改善ができる職場づくりなど、サステナブルなものづくりの在り方についての研究・実践を行っている。
共著に『物流改善ケーススタディ65--コストダウン、作業効率を徹底追求--』『続・物流改善ケーススタディ65--コストダウン、作業効率を徹底追求--』(いずれも日刊工業新聞社)、『図解 ビジネス実務辞典 生産管理』(JMAM)、『生産管理のべからず89』(JMAC)