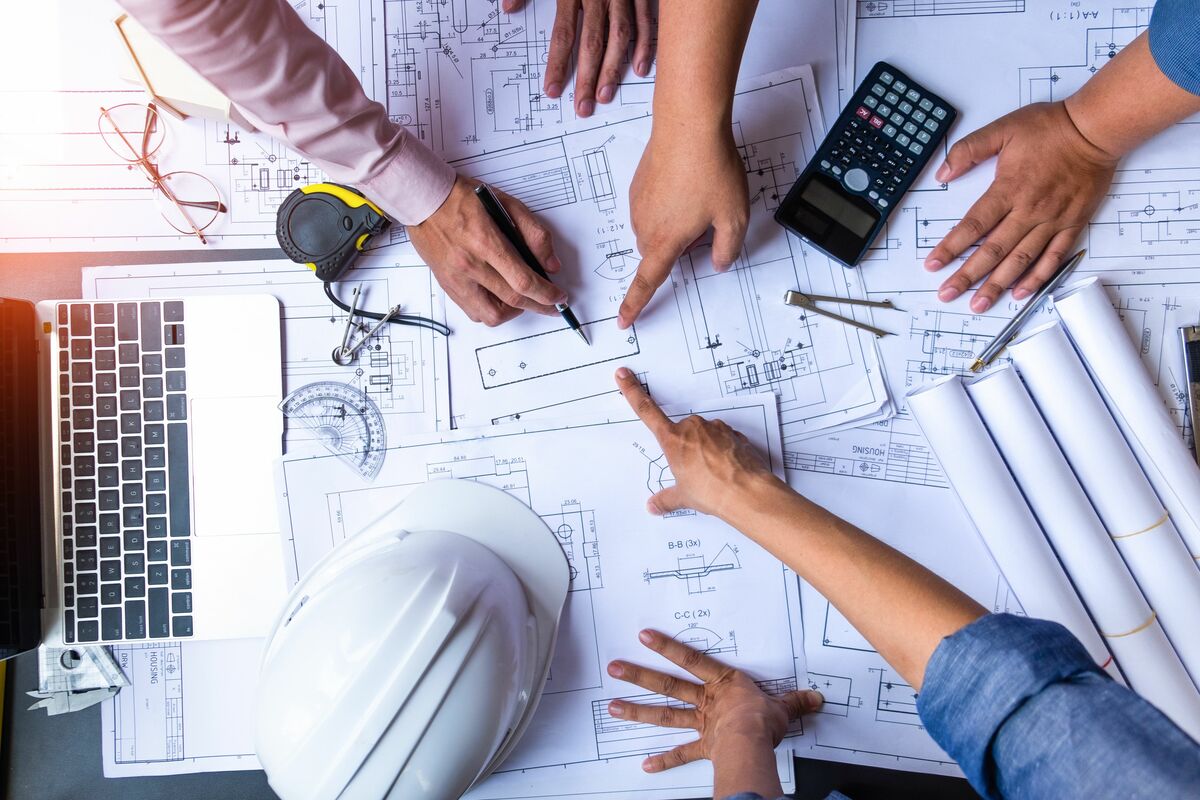
メーカー任せの設備発注がもたらす悪循環
最適設備の導入と製造条件の最適化により、QCDの水準を高めていくのは生産技術の役割である。昨今SDGsが注目され、QCD要求はますます高まり、労働人口の不足が顕著になっている。そのような中で、ものづくりの現場では設備導入による自動化、無人化を追求した工程により競争力を高めていくことが求められる。
しかし、限られた開発期間やリソース不足を言い訳に、担当者の経験やあきらかな問題対応に精一杯で、本来設備に要求すべき仕様を具体的に検討するステップが飛ばされていないだろうか。
結果として、メーカー任せで設備仕様が決まる、すなわち、標準仕様ベースで仕様が決まるため、自社にとっては冗長機能によるコストアップ、あるいは仕様が不十分なことによる生産段階でのトラブルや不良などのリスクが内在することになる。
さらに、このステップが省略され続けると、社内に設備に詳しい人材がいなくなり、自社では設備に対して何も手を付けられない状態に陥ってしまうケースも少なくない。悪循環の温床である。
設備メーカーに「要求仕様を提示できない」問題
なぜこのような事態に陥ってしまうのか。これは、設備メーカーに対して要求仕様を提示するための情報が不足し、要求仕様策定時に活用できていないからである。
この情報とは、自社固有の設備に関する情報であるが、大きく、「設備の運用に関する実態情報」であり、また「工程の将来構想に関する情報」である。設備メーカーに比べ設備固有の知識は少ない中、自社の情報を持ち合わせていなければ、メーカー主導で話が展開され、提示された仕様に対しての改善提案を出すことはかなり難しくなる。
限られた期間で要求仕様にまとめ上げ、設備メーカーと話をするためには、中長期的にこれらの情報を生成、蓄積しなければいけないが、その取組みの重要性が認識されていないことも、一因ではないだろうか。
設備要求仕様検討段階でのフロントローディング体制を構築し、自社固有の情報を投入する
この問題を解決するには、設備導入の源流段階で必要な情報を確実にインプットし、有識者との議論を通じて仕様に反映していく、フロントローディング型のプロセスに変えることが重要である。このとき、源流段階で投入すべき必要な情報は、以下の図の通り4つに分類できる。
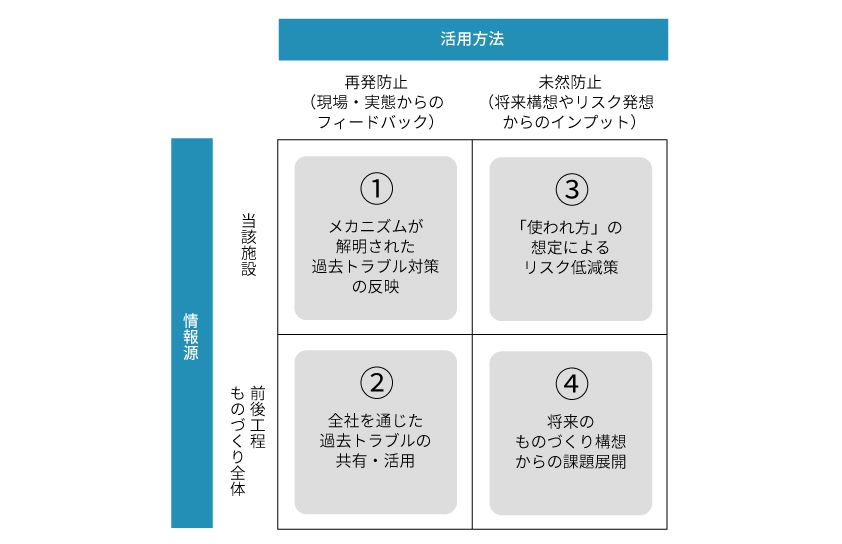
縦軸は情報源となる対象範囲を指している。当該設備に関わる直接的情報はもちろん、生産システム全体(工程前後)や他拠点の同機能設備などに関わる情報である。
一方、横軸は活用方法として、未然防止や将来課題を踏まえて想定される課題である。過去に起きたトラブルの再発防止の確実化はもちろん、あらたなリスクの検討や将来の構想から課題をインプットし、未然防止を狙っていく。図中の4つの情報についてさらに詳しく見ていこう。