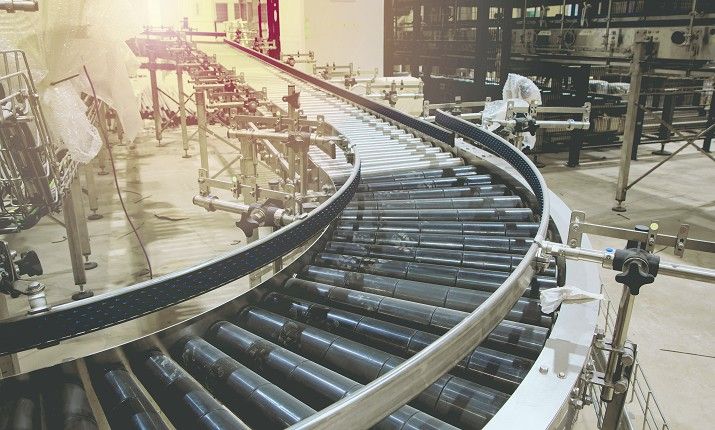
ロットまとめ生産が染みついて無駄な取り置きや運搬だらけの職場
製品や仕掛品の取り置き作業や運搬作業は、付加価値を生まない作業である。そのため、それらが少ない方が生産性の高い職場であることは、製造業に従事するものであれば基本中の基本として心得ていることだろう。
しかし、それらの作業をゼロにすること難しいことも事実である。従ってそれらの作業をできる限りゼロに近づけるべく、生産技術者は工程設計やレイアウト設計、ものの流し方を工夫する。ところが、ロットまとめの流し方を前提としたものづくりに慣れている職場は、改善できるはずの運搬作業やタッチ作業のロスを潜在化させてしまっている場合がある。
以下の図のようにロットまとめ生産している職場は、ラインバランスが悪く非効率かつ、さまざまな工程に仕掛が多数存在しているため運搬や取り置きが発生する。極端にいってしまえば、1個流しできていない組立職場、小ロットに対応できていない加工職場に多くみかける。
1個流しできる職場は工程間の運搬は少額投資で済むマテハン機器(小さなコンベアなど)でラインが構成できており、ラインバランスも非常によいため作業編成効率が高い。またロットまとめ生産している現場と1個流し生産をしている現場では作業の基本機能比率(基本機能:製品に付加価値を与えている作業 例:組立、加工など)が異なる。当然1個流しの方が無駄はなく、効率のよい生産ができるが、なぜかロットまとめから脱却できていない職場が多いのである。
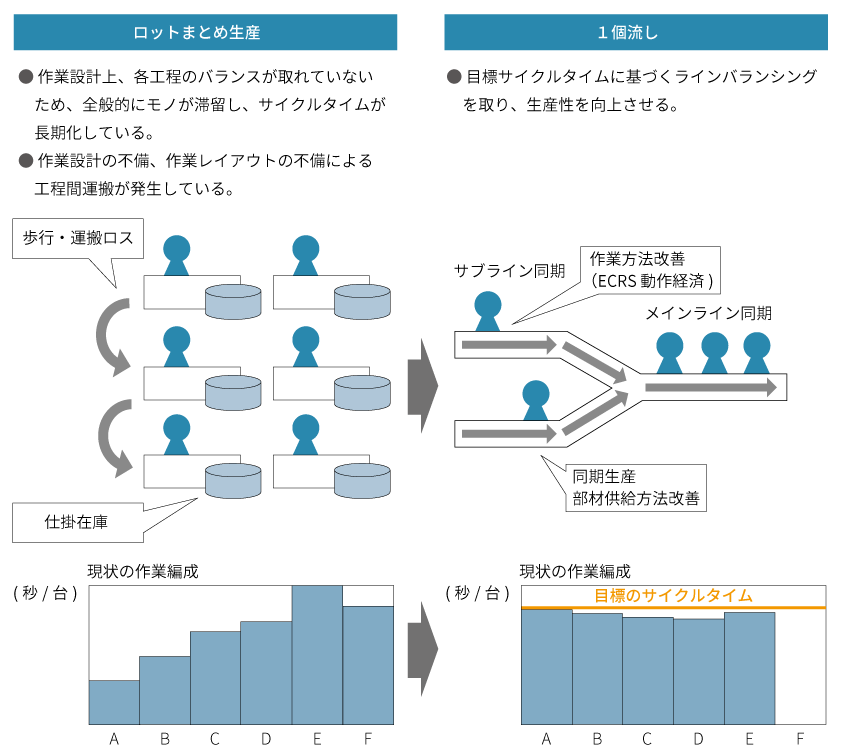
「やりやすいから」ロットまとめ作業を選択している生産技術者
仮に1品種の製品しか生産しない組立ラインがあると想定してみよう。
工程設計、作業設計する場合、1品種のみなので各工程の標準時間が設定できる。目標サイクルタイムに合うように各工程の作業分担を割り振ることで、1個流しが容易に実現可能だろう。
しかしこれが数十、数百と生産しなければならない品種が増えて、さらに仕様にも統一性がない場合だとどうだろうか。並の管理レベルでは高生産性を維持するためのラインバランスを保つことができず、各工程で仕掛が発生し、ライン停止も頻発する。
多品種少量の場合、作業編成を個別製品ごとに考えるのは大変な労力がかかる。作業設計者(管理監督者・生産技術者のスタッフ)からするとあらかじめ大まかな分担を決めて、ロットまとめ生産させて、作業者に工程間の応援をさせるやり方の方が楽だ。現場の作業者もこのようなやり方に慣れてしまって、仕掛が当たり前となり、工程間の運搬や取り置きのロスが潜在化してしまう。工程間の運搬量が増加するとマテハン機器が必要になったりして時間がかかるし、作業者も必要となる。またAGVで自動化している職場もあるが、そもそも1個流しができていればそのような機械も無駄である。
このような職場になるのは多品種少量という言葉に甘え、本来やるべきである設計標準化、計画基準の整備(工程計画、標準時間設定等)、作業設計の効率化に取り組んでこなかったことが起因している。現状は仕掛が停滞し、運搬ロスなどが発生している姿から改善後のような1個流しの生産方式にいかに変革するかが重要となってくる。