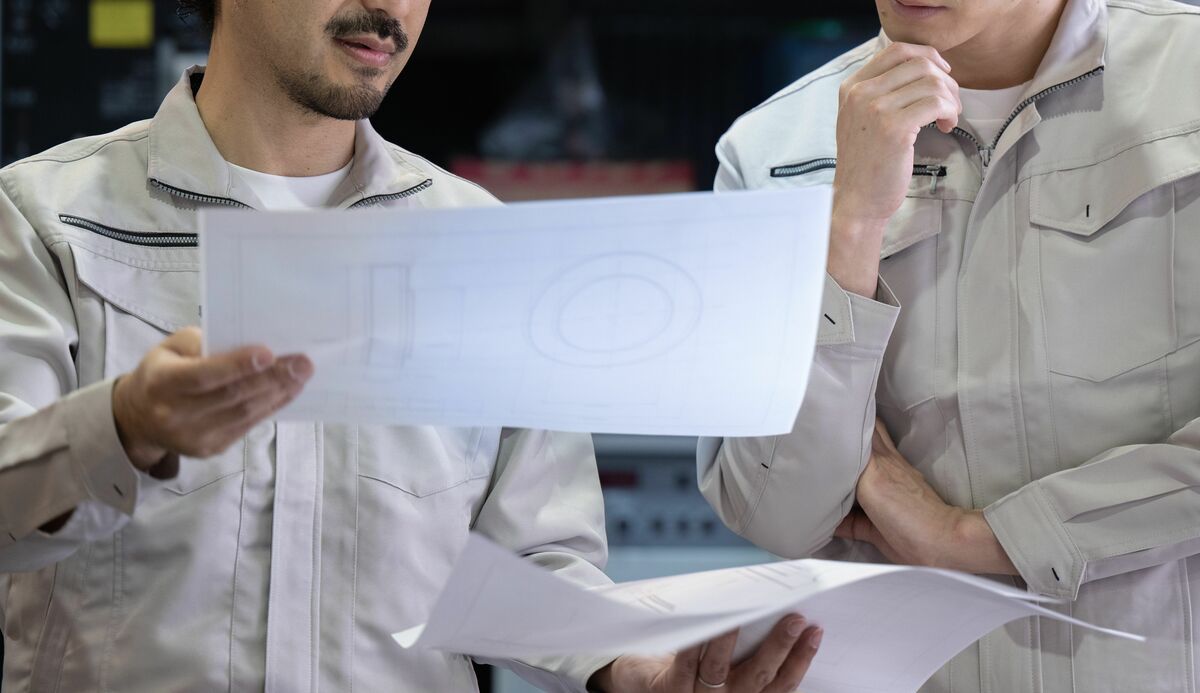
基準情報が整備されていない生産現場で起きていること
生産計画を立案するためには、<計画の基準となる情報の整備>が重要であるが、それらの基準が整備されていないケースが多い。その結果、生産管理部門は、営業部門からの情報を右から左に流すだけの役割になっており、本来生産管理部門が行うべき管理業務を、製造現場が行わなければならない状況になっている。
基準情報が整備されていないまま生産指示を行った場合には、生産計画が実態とずれているため、製造現場の監督者が生産計画を作り直すことも多い。つまり、生産管理部門と製造部門の二重計画が発生している。
よく見られる基準情報の不具合としては、
(1) 品目→新製品の登録遅れ、設計変更
(2) 構成→仕様変更、設計変更
(3) 発注→見積もりの遅れ、コストダウン要請
(4) 工程→作り方が決まっていない
(5) 基準時間→設定していない、メンテナンスが行われていない
(6) リードタイム→そもそもいい加減、決め方が分からない
などがあげられる。
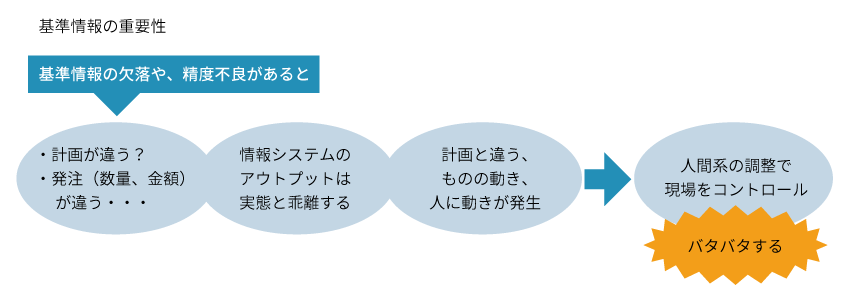
特に、基準時間、リードタイムについては、生産スケジュール、設備計画、人員計画に影響を及ぼす情報であるものの、整備不足のまま、生産計画を立案しているケースが多い。製薬メーカーのある工場では、生産計画は、数量計画が中心で、負荷計画機能が弱く、シフト・人員計画をオーバーする場合のみ、計画調整を行うが、少ない場合の調整はほぼ行われていない。
このような場合、基準時間やリードタイムに余裕を持たせて計画立案を行うことになり、結果として、低効率での生産活動になってしまう。
実績収集、部門間コミュニケーション不足、工数計画の仕組みが無い
基準情報が整備・活用されていない理由の1つ目として、実績情報が正しく収集できていないことが考えられる。製造現場で日報を記入しているものの、それらの情報を分析し、標準的な情報として登録できているケースは少ない。バラつきのある情報を分析するスキルが無いことや専任で業務する担当者が不足している場合も多い。
2つ目としては、生産管理部門と製造部門のコミュニケーション不足が考えられる。実績収集はしているが、生産管理部門と製造部門それぞれで基準情報を取りまとめていて、情報共有が行われていない。ありのままに情報を共有することで、自部門に不利になる基準が作られることを避けたいなどの意思が働いている場合が多い。
それらが常態化してしまうと生産計画部門はズレを当たり前のように許容することになり、結果として販売部門からの必要量を右から左へと流すだけの生産計画になってしまう。
3つ目としては、基準情報に基づく工数計画の仕組みがないことが考えられる。基準情報のメンテナンスを含めて、負荷計算や能力計算の算出ロジックを明確にし、定量的に提示することが必要となる。