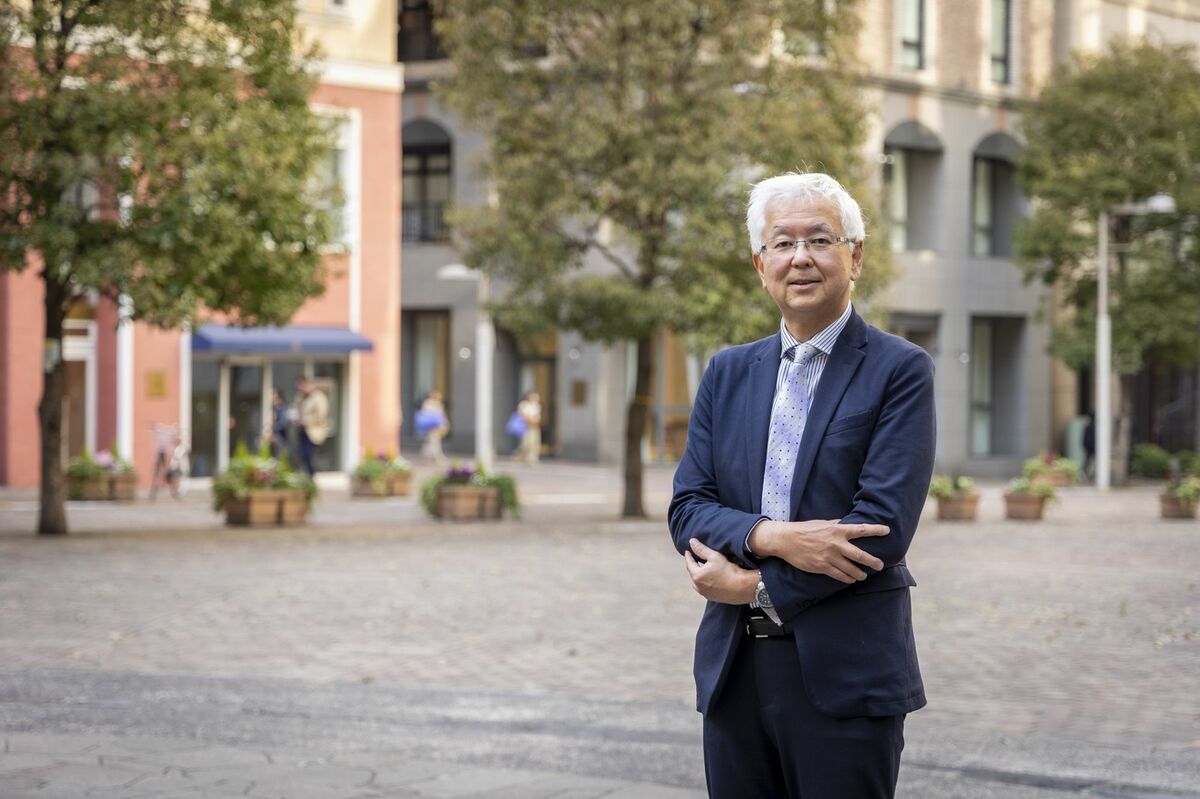
ものづくりの先端技術を駆使する製造業でも、調達、生産管理の現場では未だに紙ベースの業務が続き、DXが遅れているケースは多い。カシオ計算機では、調達やPLM(プロダクトライフサイクルマネジメント)の領域でDXを断行。商品企画、開発を含む領域に拡大した一気通貫の情報共有を進める。全社規模のサプライチェーン改革をリードするキーマンに聞いた。
2000年代のIT化が生んだサプライチェーンの課題
――カシオ計算機(以下・カシオ)では調達、生産を中心にしたサプライチェーンの改革を進めています。これまでの経緯をお聞かせください。
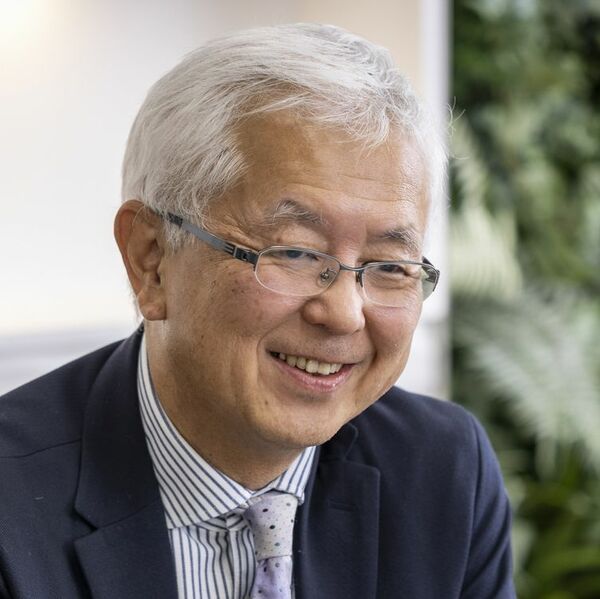
1981年カシオ計算機入社。海外営業、物流企画、業務開発(情報システム)部門長を経て、2006年執行役員業務開発部長(CIO)を務める。その後、生産資材部門へ異動し、2015年執行役員生産資材統轄部長、2017年執行役員生産本部長に就任。2020年生産本部シニアオフィサー、2022年より現職。情報システムベンダーのユーザー会長、IT人材育成審議委員など社外組織の活動も多数。
-----
座右の銘:「一生勉強」
注目する企業経営者:野路國夫氏(小松製作所元社長:情報システム本部長、生産本部長を経て社長に就任したDXの先駆者)
お薦めの書籍:『マネジメント』(ピーター F.ドラッカー著)
矢澤篤志氏(以下敬称略) 私は情報システム部門を長く担当し、CIOを務めた後、2012年に生産部門へ異動しました。調達、生産管理部門のオフィスに着任して最初に感じたのは、なんと紙が多いのかということでした。フロアでは電話も鳴り続けており、まさに「昭和アナログ仕事」の世界でした。
なぜ、調達、生産管理の領域はITの活用が遅れていたのか。もちろん、社内の基幹システムであるERPは2000年代から稼働しており、調達や生産領域で、海外を含めた受発注、在庫、計画などはその機能でカバーしていたので、デジタル化も進むはずでした。
しかし、ものづくりに必要な図面や部品情報の共有、納期情報の確認など、調達にかかわる業務は、アナログから脱却できませんでした。システムから取り出したデータをいったん紙やPDF、Excelデータに加工してからメールに添付してやりとりするという煩雑な作業をしていました。加えて、電話での後追い業務が多いなど、さらに手間がかかっており、当社だけでなくパートナー企業にも同等の負担を強いていました。
また、国内のパートナー企業については、2000年代にEDI(電子データ交換システム)で連携しており、ペーパーレス化を実現していたのですが、このシステムはバージョンアップがほとんどなく、使い勝手に問題がありました。また、当社だけでなくEDIに接続するサプライヤー企業にもシステム費用をいただく必要があり、特に、中堅・中小企業には負担を強いていました。EDIは海外のサプライヤーには導入できず、海外の生産比率が8割を超えている当社にとって、不十分なシステムでした。
このように、当社の調達、生産管理は、縦割りのシステムの間に多数の「デジタル空白地帯」が生じており、そこを人の手で埋めて回しているのが実態でした。
――そこでサプライチェーンシステムの再構築に着手したと思いますが、ここ数年の外部環境の変化を考慮しなければいけないと思います。どう対応していますか。
矢澤 まさに、外部環境の変化が、改革を待ったなしの状況に追い込んでいると感じています。半導体需要の増加による部品の逼迫やロシアのウクライナ侵攻による原材料費の高騰、さらに国際経済のブロック化など、グローバルサプライチェーンを取り巻く状況は、「VUCA」といわれる先の見えない不透明さが、当たり前の現実となっています。
そのなかでメーカーとしては、調達品のプロセスの所在地を確認し、臨機応変に対処していかなければいけません。しかし前述したような、人の手に頼った非効率な業務に支えられたサプライチェーンでは、情報共有のスピードと精度の点で大きな問題があります。一刻も早い改善が必要でした。
改革にあたって基本的なコンセプトとしたのは、「シンプリファイ&コネクト」です。業務ごとに縦割りに導入されていたシステムに横串を入れ、一つのインターフェースで各システムを連携するプラットフォームを作ることを目指しました。
具体的には、ERPでカバーできない社内領域は、全社統一でローコードツール+ETLツールで内製開発できるようにし、サプライチェーンに関わる仕事全体のデジタル化を実現しています。また調達領域では、その基盤にSaaS型のサービスを組み合わせてプラットフォームを作ることで、サプライヤー企業には費用負担なくご利用いただくことを可能にし、海外のサプライヤー企業のアクセスも可能にしました。すでに注文データの共有や納期、請求確認などのシステムは稼働しており、現在は金型、図面などの設計情報を共有できるシステムの開発を進めています。