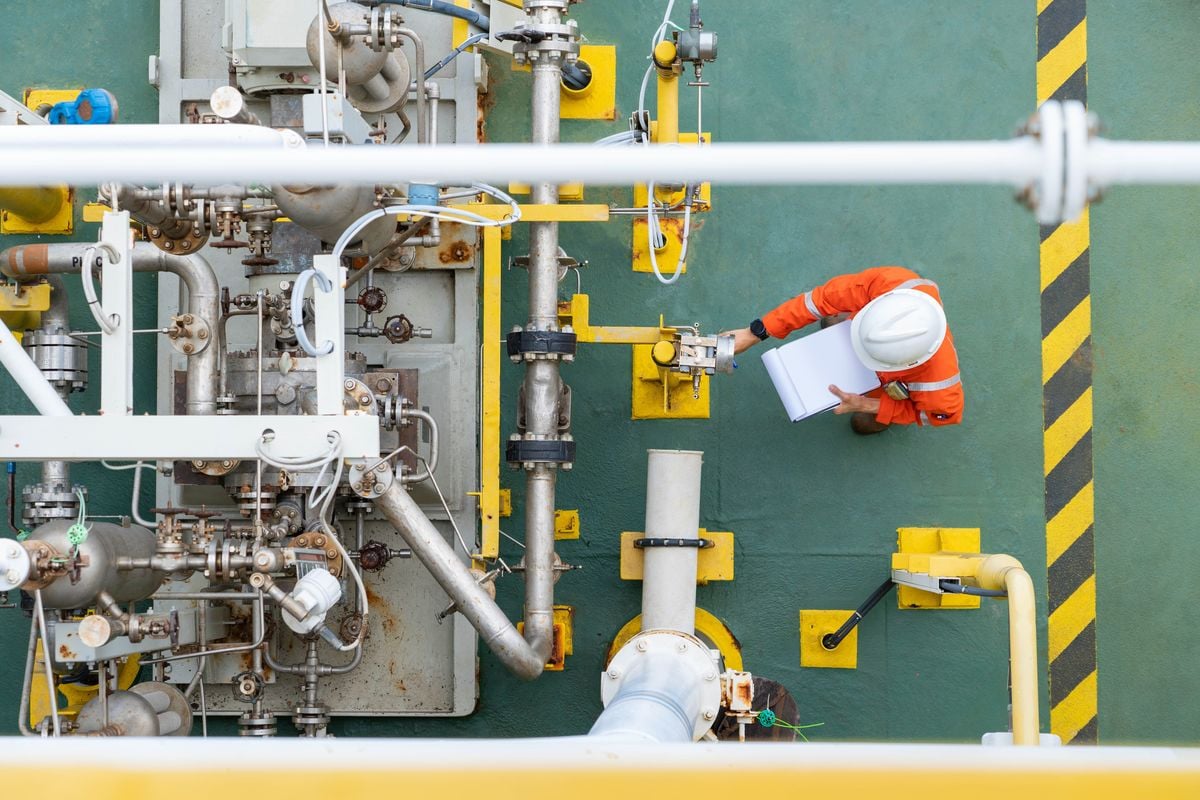
シリーズ第2回となる今回は、タイ製造拠点の実態と、その課題解決の方向性として大切な「仕組みづくり」「人づくり」について説明しよう。
5つの観点から経営課題を整理した
タイの製造拠点には他のアジア諸国の製造拠点よりも高いレベルの成長を求められており、この拠点を軸にアジア展開を図っている企業が増えてきた。しかし、グローバルな視点で見るとタイの製造拠点は総じて改革道半ばという印象を持たざるを得ない。
今回はその理由をこれまでの筆者の経験から整理しよう。全てが当てはまるという拠点は少ないと思うが、これらの問題が一つもない拠点ということもないと思う。まずはこのような問題がないか考えながら読んでいただきたい。
QCD面から見る経営課題
◆品質面の課題
まずは品質面についてである。日本の製造現場では「後工程はお客様」「源流保証」など各工程の品質意欲を高める取り組みが重視されていて、クレームのみならず工程内不良をシビアに管理している。しかし、この品質管理の方法や精神をタイの製造拠点にも持ち込んで品質管理をさせようとしても、なかなか効果が上がらないことが見受けられる。
クレームが発生した場合、その発生工程や発生要因を追求、対策を実施することで再発を防止するが、そのときに大切なのが、関連するメンバーがその内容を知って行動することである。しかし、タイの製造拠点においては、管理者(日本人赴任者や現地管理者)が対策を検討し、現場の作業者へ指示命令するだけで展開している状況がしばしば見受けられる。
現場の作業者はそのようなクレームが出たこと、管理者が対策をしたことを知らず、単に管理者からの命令により作業方法が変わったという認識しかしていないことが多い。そのため、対策内容が徹底されず、あるいは誤解されたまま作業が行われるということがある。
また、クレームが出ていないとしても、各工程の品質基準が現場の作業者に理解されず、甘い基準になってしまうこともある。ひどい場合には、誤った検査方法で検査をする、あるいは検査もせずにチェック表に記載するだけという作業になっていることもある。
そのため、検査結果だけを管理してもその実態には気付けず、問題を引き起こすことがあり得る。そうしたことを防ぐためにも、QC工程表を整備して現場の人に理解させ、現場で実践・定着させることが必要となる。
これは調達する材料や部品についても当てはまり、サプライヤーの不良問題が自社の製品品質に影響を与えることも多々ある。タイに進出している日系企業の現地調達率は50%を超えるという実態調査結果もあるが、まだまだ満足できる調達品質を実現できていない企業も存在する。
◆コスト面の課題
タイの製造拠点を運営する大きな目的の一つは、コスト面にあると言っても過言ではない。しかし、製造拠点に問題が多発し、追加費用が必要以上に発生している企業が多いことも見逃してはならい。
例えば、日本人赴任者、あるいは出張者が非常に多い企業がある。もちろん、製造拠点に何らかの問題があるため日本人がサポートしているのだが、その結果、タイの製造拠点の費用が増大し、ともすると複数の指示が飛び交い、製造現場の混乱を引き起こす場合もある。
また、品質面やデリバリー面でも基準や計画から逸脱することで多大な費用がかかるケースもある。材料や部品の追加発注、緊急輸送のためのデリバリー費用など余計な費用が発生する理由は多岐にわたる。
いずれにしろ、安定した生産を実現できる拠点を早く作り、ローコストオペレーションを実現する必要がある。