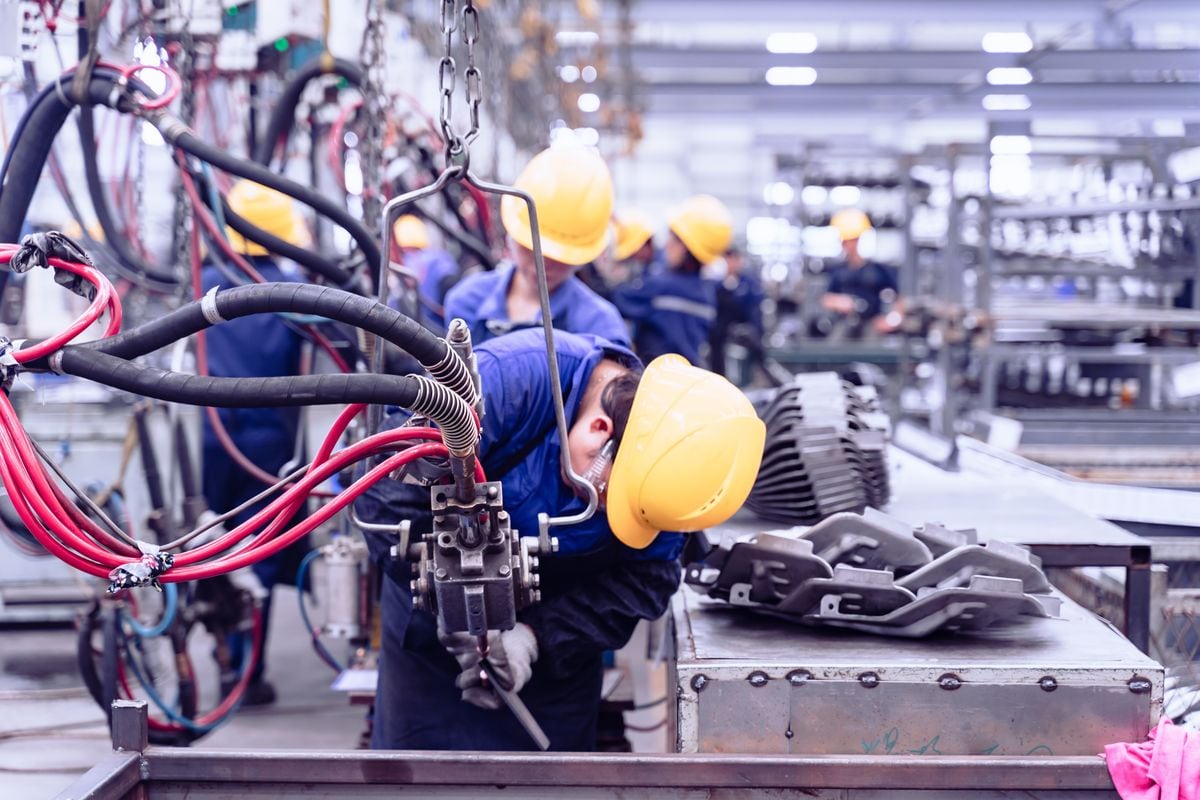
第3回となる今回は、タイの製造拠点における仕組みづくりをテーマに、高い生産性を実現する製造プロセスをつくる上での大切なポイントについて説明しよう。
製造プロセス立ち上げにある2つの問題
タイで製造拠点を展開している企業は、多くの場合、日本国内での製造プロセスを移管している。しかし、日本国内の製造プロセスのように正常な生産ができていない企業が多いのが実態である。これらの課題について製造プロセスの立ち上げという観点で2つの問題についてみていこう。
◆新しく生産ラインや設備を設置するときの課題
1つ目はプロセスそのものを立ち上げる、すなわち新しくラインや設備を設置して量産していく上での問題だ。
タイにおいて新しくラインや設備を設置する上で非常に大切なのは、単純化・標準化された作業設計となるように工程設計を行うことである。
日本国内の製造プロセスをそのまま移管すると問題が起こることがある。日本国内のプロセスは古くから小集団活動やQCサークルなどを通じて現場の工夫が多く盛り込まれており、高いスキルを持った熟練作業者を前提とした工程になっていることがある。過去からの改善ノウハウや熟練者の作業を前提条件として、タイに製造ラインを設置すると、多くの場合、不具合が発生し、管理ができない状態になることが多い。
筆者もそのような現場を数多く見てきた。例えば、日本でセル生産を行っている組み立て作業があり、タイにそのまま移管したところ、生産性は一向に上がらず不良も減らないという問題が継続し、日本でかつて行っていたようなライン作業(分業)体制をあえてつくったという企業もあった。日本国内では作業者が図面を読み取り、それを組み立て手順に展開し、実行するという作業を行っていたが、それには高いスキルとノウハウが必要だった。そのため、タイでその生産方式は十分に機能しなかったのである。
過去には日本でも生産方式に関して、ライン生産方式とセル生産方式のどちらがよいのか、という議論があったが、その本質を知らずに今の生産方式をそのまま移管してしまうと無理が生じる。海外で新しく生産ラインや設備を設置するときには分業レベルを考慮して工程設計を行うことが重要である。
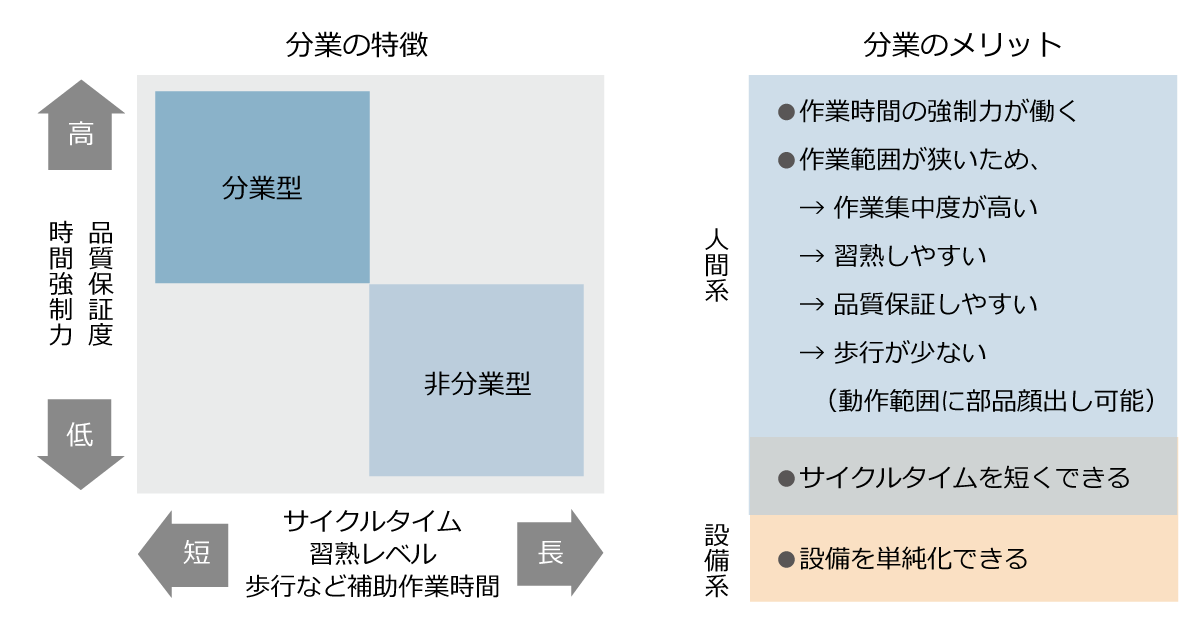
また、別の企業では鋳造設備を導入して鋳造部品を生産していたが、1回の切り替え時間に数時間もかかるため稼動率が低下、さらに生産しても金型に起因する不良が多発している状況であった。
切り替え作業の方法や金型のメンテナンスに関しては日本国内で標準手順書を作成し、その英訳版を作業者に読ませて作業させていたが、作業者が英語で書かれた作業標準書を正確に理解できない上に、内容そのものも表面的な手順の記載しかなかった。
本来のノウハウは高いスキルの作業者に属人化していたため、タイの拠点には技能が伝承されなかったのである。これは、ある意味では日本国内(日本の作業者)の生産性の高さを裏付ける事例だが、海外で生産ラインや設備を立ち上げる際にはノウハウやスキルも含めて標準化が進んでいないと大きな問題を引き起こす可能性がある。