どうすれば安定した製造プロセスを早期に実現できるか?
これまで説明してきたように、単純化・標準化したプロセスを設計し、守るべき標準や製造条件を現場で順守させることが安定した製造プロセスを早期に実現するために必要なことである。
新規にラインや設備を設置するときには、現地の作業者の技能レベルを見極めた上で、ライン(分業)方式を検討することも必要だ。また、量産立ち上げにおいては量産時を想定した製造条件を設定し、順守できるような現場への落とし込みと順守されるように管理することが非常に重要である。
これらのことを実現するには、現地の努力だけでなく、生産技術部門や開発設計部門を中心とした日本からの支援方法や体制を改める必要がある。例えば、現地の技術者、管理者を交えた工程設計や立ち上げのプロセスを確立する、現地生産技術者を強化するための実践教育を強化する、量産開始時点だけでなく安定生産までを常駐してフォローするなど、これまでのやり方を見直してみることだ。
今回はタイ製造拠点の製造プロセスの立ち上げという観点でどのような問題が生じているか、その問題を解決するために大切なことは何かを解説した。次回は立ち上げたプロセスをより高いレベルに改善する「製造プロセスの生産性向上」について、具体的な事例を交えて整理したい。
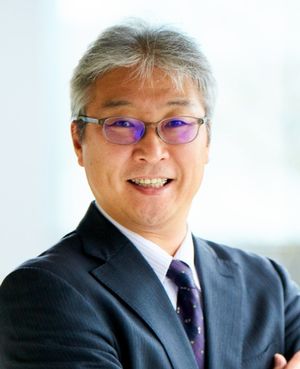
コンサルタント 角田賢司(つのだ けんじ)
生産コンサルティング事業本部
プロセス・デザイン革新センターセンター長
兼 デジタルイノベーション事業本部 シニアコンサルタント
IEをコア技術として収益向上のコンサルティングに取り組んでいる。自動車(部品)、化学プラント、樹脂成型、建材、食品等、多業種で収益向上の支援を実施。現場の生産性向上、品質向上、調達コストダウンや在庫削減等複数テーマを同時に展開、マネジメントの支援を行う。近年はタイ・中国等の製造拠点支援として生産性向上や品質向上の成果実現と併せ、マネジメントの仕組みづくり、ローカル人材育成を実践