真の原因を究明しよう活動
品質クレームの再発を防止するためには、「なぜなぜ分析」を行い、要因を掘り下げ、「真の原因をつかむこと」が必要である。品質管理部のメンバーや工場の管理職の誰もが「真の原因をつかむこと」の重要性は認識していたが、本当に真の原因が究明できたかどうか曖昧なまま対策を行ってきたというのが実情であった。
そこで、品質改革プロジェクトでは改めて、この真の原因究明に挑戦した。「なぜなぜ分析の基本」を勉強し直すとともに、今まで管理してきたクレーム率や不良率といった結果の指標だけではなく、原因究明が確実にできているか否かが分かるような活動指標の設定も検討した。
そこで考えたのが「真の原因究明率」という少し変わった指標である。当初、プロジェクト内でも、「そんな指標どうやって定義するの?」といった意見が交わされたが、逆に、その指標をどうやって定義すればいいか分からないということは、「真の原因究明がなされたかどうか分からないまま、なぜなぜ分析をやってきたのでは」ということになるわけである。
指標の定義から議論を重ね、4M(man、machine、material、method)にもれなく目配せをして、そこから「現象が引き起こされるメカニズムを突き詰め、これが犯人だと特定できれば真の原因が究明された」とみなすことでスタートした。
「真の原因究明率」を導入したことで、真の原因とはなにかを単に言葉だけでいうのではなく、再現性をテストしたり、現象発生のメカニズムを究明しようという意識が定着したことが活動の大きな成果となった。
製造・設備部門一体で生産性と品質を改善しようモデル
工場の設備は、それを使用する製造部門側からすると、必ずしも使い勝手のいいものばかりではない。中には洗浄するために分解しなければならず多大な工数がかかったり、切り替えのために特殊な工具を持ち込んで時間をかける必要があったり、品質に影響する重要な部位の交換が容易にできなかったり、などといった問題を抱えていた。
品質改革プロジェクトでもこの問題を取り上げ、設備設計の段階から「洗浄しやすい」「分解しやすい」「交換しやすい」といった現場の作業性・品質安定性に配慮した設備仕様を勘案するというモデル構築を狙った。設備部門も現場の要望を分かってはいるものの、今までは「いきなり全部やるのは無理だし、お金もかかる」という言い分だった。
プロジェクトでは、作業性、品質安定性の面から、優先順位をつけ、「モデル設備改良にトライしよう」という活動を行った。モデル設備は洗浄のために分解が必要な「撹拌機構」を持つ混練槽で実施し、ワンタッチ式の分解しやすい機構の採用に至った。その結果、分解洗浄時間が大幅に短縮され、その時間を工程内の品質点検やクレームの原因究明にあてることで、品質改善の後押し効果も発揮された。
初年度下期に入ると、クレームの削減効果が表れ、最終的には上期対比で品質クレームの30%削減、現場の設備洗浄工数半減(モデル設備)という成果をもたらした。これらの活動で「目指す姿」の実現に向け、大きな自信を得ることができ、2年目以降も「品質改革は現場が主役」という考え方に沿って進める予定である。
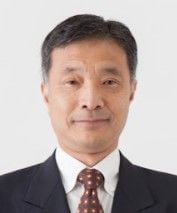
コンサルタント 廣田正人(ひろた まさと)
生産コンサルティング事業本部 クオリティー&エンジニアリング革新ユニット
品質革新センター テクニカルアドバイザー シニア・コンサルタント(技術士)
企業の「品質経営実践」を基本に、「工場の品質保証・安全性保証体制の構築」、「製造現場の生産性向上・品質向上」といったテーマから「開発部門・調達部門のリスクマネジメント」まで、生産活動全般に渡る幅広い分野のコンサルティングを手がける。特に、化学・医療機器・食品工業の安全・品質マネジメント、労働安全衛生管理についての指導経験は豊富であり、最近ではこれら業界の事業基盤強化、リスクマネジメント、コンプライアンスについても積極的に取り組み経営課題の解決を支援している。