お客さまの信頼を取り戻せ
A社ではこのようなトラブルも起こった。景気が悪くなり、売り上げと利益が低下した時、追い打ちをかけるように品質問題が起きてしまったのである。ただでさえ協力会社に対する厳しい風が吹いている中、品質上で問題を起こすことは、取引削減、停止につながることになりかねなかった。さらに、クレーム対応に多くの時間と労力を使うことで、コストアップとなり、ますます経営を圧迫した。
売り上げや利益を出し続けるために、必要なことはさまざまあるが、一番大切なのは安全・品質である。まずは、お客さまが安心して仕事を任せることができる会社にならなくていけない。
お客さまから、品質が良いと思われるには、もちろんクレームを出さないことが重要である。しかし、万が一クレームを発生させたとしても、そのときの対応が良ければ、しっかりした会社と評価される。
A社ではクレームが発生した際に、迅速で適切な対応が行えるよう、社内でのクレームの処理ルールを決めて、それを周知徹底させることから始めた。
その次に、各生産工程の品質レベルを上げ、不良を発生させないようにした。だが、このことは一朝一夕にできることではない。そのため、不良が起きないようにする発生防止活動を行いながら、併せて流出防止活動も行った。たとえ不良が発生したとしても絶対にそれを顧客のところまで行かないようにするのである。
流出防止活動を進めるにあたって、製品の品質チェックの在り方もどうあるべきかを考え直した。
品質チェックの最後の砦は出荷前の完成品検査である。ここで見逃してしまうと、流出した不良がクレームとなって返ってくる。
まず、品質検査を行うためのチェックシートを見直し、カタチだけのチェックからの脱皮を行った。加えて、チェックシートでのチェック項目とその基準は誰でもが行えるよう、簡単明瞭なものに変更した。
しかし、単純な製品であれば、最終工程での完成品検査は比較的簡単に行えるが、複雑な製品となると完成品検査では検査しきれなくなる。そのような場合は、製品を作る一つ一つの工程において、そこで行われたことが品質的に問題ないかどうかを確認する、工程内検査を行うことが必要となる。これは、各工程で品質が保証されれば、その工程の積み重ねとして出来上がった製品は品質が保証されているという考え方だ。
この検査について工場の管理監督者だけでなく、作業者にも理解してもらい、作業者それぞれが、自分の行った仕事に対してのチェックを行った。人が行う検査や確認作業は、気を付けていても、ミスや漏れが発生してしまう。現在ではバーコードやQRコードをスキャンする方法などで、デジタル化を図り、人のミスが発生しない工夫を行っている。
各工程で品質不良をチェックすることは大切なことだが、完璧なチェックを行おうとすると、時間とコストがかかる。もちろん、一番良いのは、各工程で、そもそも不良を発生させないような仕組みを作ることである。
・いつも同じやり方で作業はされているだろうか?
・誰が行っても同じやり方であるか?
・そのやり方は誰でもが分かるようになっているか?
これらのことを実現するため、全ての作業に対して、その標準を決めるべく、A社は今も努力を続けている。
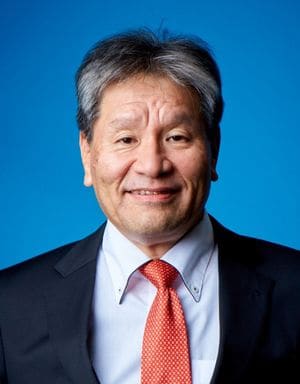
コンサルタント 松本賢治(まつもと けんじ)
デジタルイノベーション事業本部 シニア・コンサルタント
調達、生産、物流、販売にわたるサプライチェーン全般を対象とし、長年数多くの企業を支援してきた。多様化するものづくり分野における豊富なコンサルティング経験をもとに、現在は「IoT活用イノベーションマップ」、「現場IoT7つ道具」などを開発、製造業のDX推進を支援している。