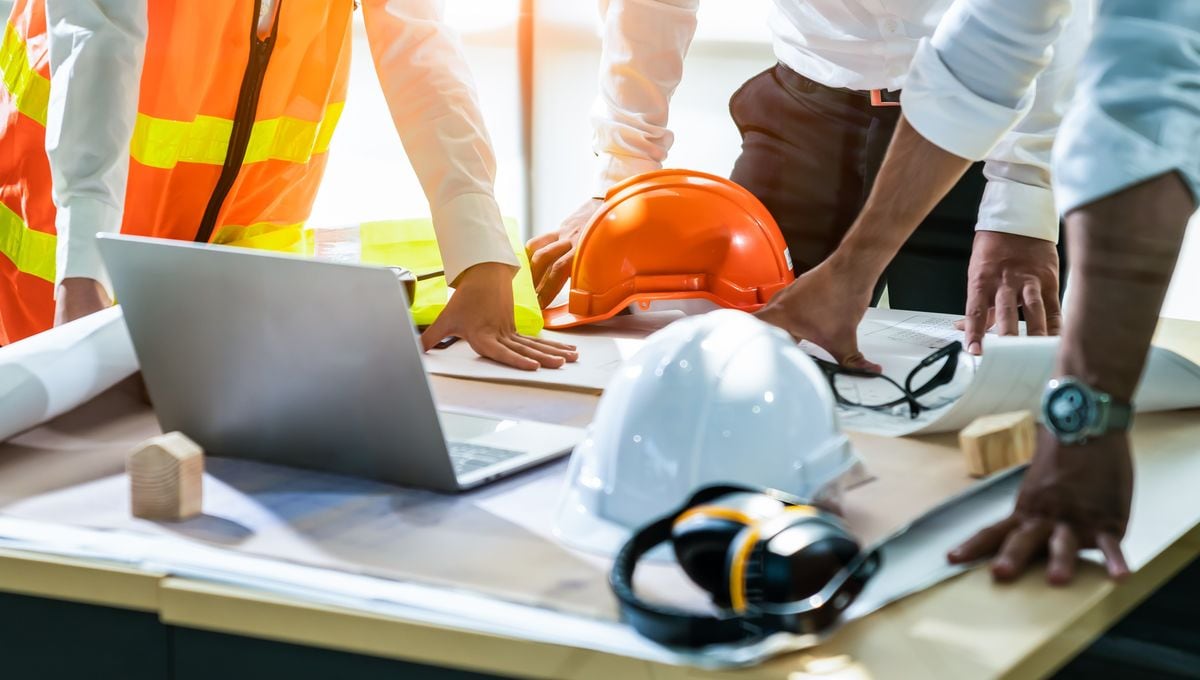
第6回となる今回は、タイの製造拠点における仕組みづくりとして、「生産管理」のポイントについて説明しよう。
タイ製造拠点における生産管理の実態
生産管理の機能には大きく「計画」と「統制」の2つがある。顧客ニーズを満たす生産計画を立案し、計画を確実に遂行できるよう各種リソースを手配、生産の統制を行うという生産現場にとっては重要な機能である。
昨今はタイ製造拠点でも製品種類が増加し、各種投入リソースも複雑になっているため、マニュアルでこの業務を遂行している企業は少なく、生産管理システムなどの情報システムを導入し、活用が進んでいる。しかしながら、(日本国内と同様に)導入された情報システムを活用しきれず、生産の現場に混乱をきたしている、あるいは生産性を低下させている日系タイ製造拠点も少なくない。このような実態について、その問題や処方箋を整理したい。
■生産計画立案の実態
日系タイ製造拠点では日々の生産計画が守れず、納期通りに出荷するのに苦労している、という悩みを持つ現場が多いように思う。製造現場における計画順守は果たすべき重要な機能であり、計画順守の実現は生産能力向上など拠点成長の基礎となる。
ところが、実現できない(守れない)無理な計画が立案され、現場に指示されて、結果として計画順守を諦めた生産が常態化している現場もあるように思う。
生産計画は営業からの受注に基づき、実現性を考慮して立案されるのが一般的だ。実現性を考慮するとは、生産に必要な各種リソース(モノ、人、設備など)の適正量を納期通りに手配できるかどうかを確認することである。多くの企業では既に各種資源の必要量を算出する仕組みやそれを手配するルールが決まっている(生産計画立案時に考慮されている)はずである。
しかしながら、ここで無理が生じていてもそのまま計画として確定している、あるいは手配計画が順守されないために生産計画を変更せざるを得ない現場もあると思う。
また、計画精度を高く維持するためには、実績情報の正確性が求められることも理解してもらえるだろう。リソースの種類や数の情報を正しく表現することはもちろん、タイミングの適切さも大切な正確性の要素である。
ある企業では発注した部品が工場に届いているものの、入庫処理・実績計上が遅れたために、部品が欠品していると判断され、結果として計画変更や追加発注が生じてしまうという問題が発生していたケースもあった。 いずれにしても立案された計画が順守できていない場合、妥当な生産計画を立案できるように検討する必要がある。
■現場での統制の実態
適正な生産計画が立案されたとしても、また仮に達成が難しい生産計画が立案されたとしても、計画順守に向けた努力は現場で行う必要がある。計画に問題がなくても、現場への指示の仕方によっては日々計画された生産量をこなすことだけが目標になっているケースがある。
計画されたロット、量、順序を無視して自らがやりやすい順序で生産を行う、具体的には数量を上げるために現場主導で計画を解釈してしまうなどは、タイの現場では起こりやすいように思う。特に現場への指示が種類と総量の指示になっていると、このようなことが起こりやすくなる。
現場の管理者を中心に守るべき種類と量を時間帯別に共有し、進捗管理に生かすことが大切である。現場の管理者が何をどこまで行うべきかを理解した上で進捗を見ると、問題に早く気が付くことができ、対処も進む。
現場の管理者には、ただ数量を上げるだけでなく、順序や時間も守る重要性を理解させ、行動させることが求められるのである。この点で、現場の管理者の役割を見直す必要がある企業も多いかもしれない。
現場の管理者が計画順守に責任を持っていないと時間いっぱい作業をして、時間がくれば終了するという現場になってしまう。こうした状態が定常化してしまっている企業は意外と多いように感じる。計画の順守に対する意識が乏しいため、品質や設備のトラブルに対する感度が低下、生産性が低下して納期遅れの発生につながり現場が混乱する。