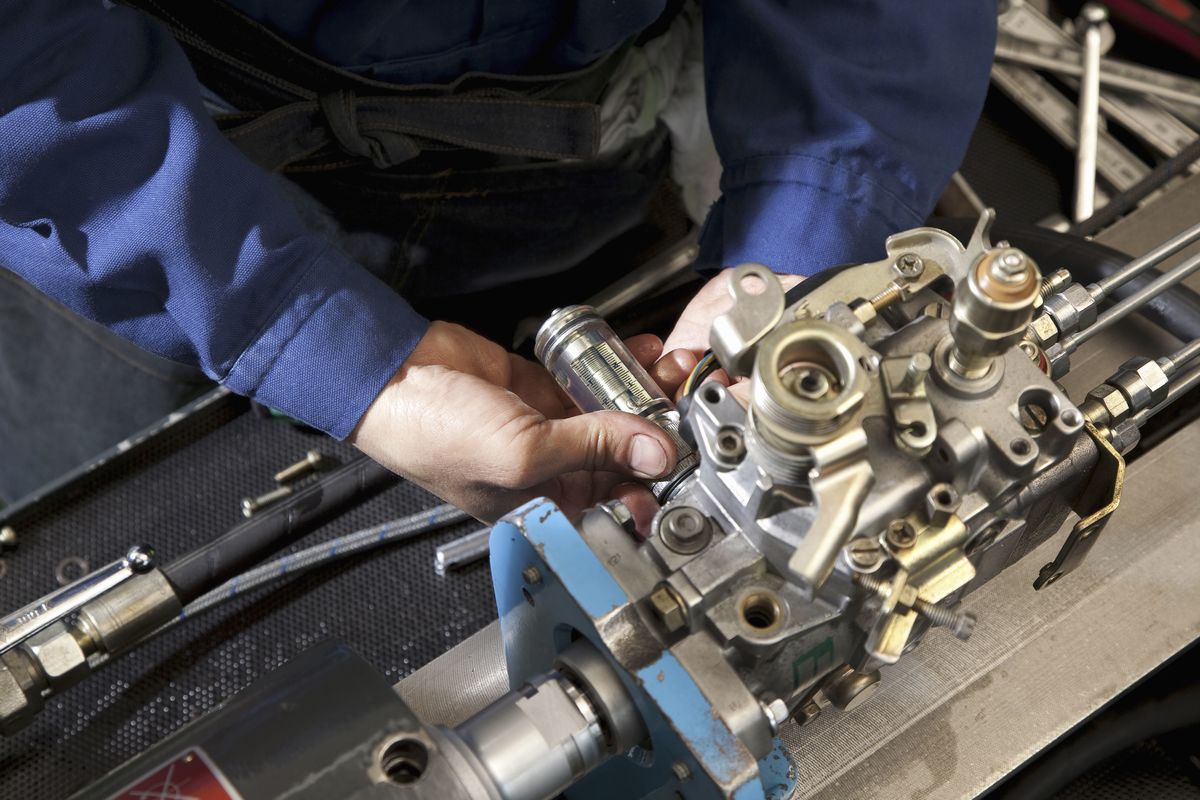
第4回となる今回は、タイ製造拠点における仕組みづくりとして、高い生産性を実現するための「生産性向上」のポイントについて説明する。
タイの製造現場においても生産性は重要な管理指標となっており、多くの企業で実際に管理されている。生産性を向上させる改善技術は日本と変わらないが、タイにおいて生産性の向上を実現するのは日本以上に難しい。
このコラムでは、なぜ日本より難しいのか、その実態はどうなっているのかということを整理していきたい。なお、生産性というのは活用目的によりさまざまな指標が取られるが、ここでは人にフォーカスした「労働生産性」、設備にフォーカスした「設備生産性」について、その実態や向上のための処方箋について考えていこう。
労働生産性管理の実態
労働生産性は時間当たり、あるいは1人当たりの生産量を示すと説明すれば、現場のメンバーは理解する。しかし、いざ労働生産性を向上させようとすると、改善が思う通りに進まないのが実態である。
労働生産性を上げるためにはメソッド(M)を変える、パフォーマンス(P)を向上させる、活用度(U)を高めるというMPUの3視点から改善を実施するのが有効である。
人が作業している状態からロスを発見し改善する必要があるが、タイの現場ではロスを把握できていない場合が少なくない。実際の現場では、驚くような実態に陥っていることもある。
そのため、少なくとも生産性の高い現場をつくるために、人のロスがどのようなものであるか、その見方を理解することと合わせ、人という資源を最大限活用することが大切だと認識してもらう必要がある
また、労働生産性を測定する指標を細かくし、精度を"高め過ぎる"ことが問題を生むケースがある。下図は日本における労働生産性管理の指標構造の例である。少なくともこのような基本的な内容をベースとして職場ごとに管理指標を設計し、測定、問題把握、改善、効果確認に活用できるようにすべきだと考える。
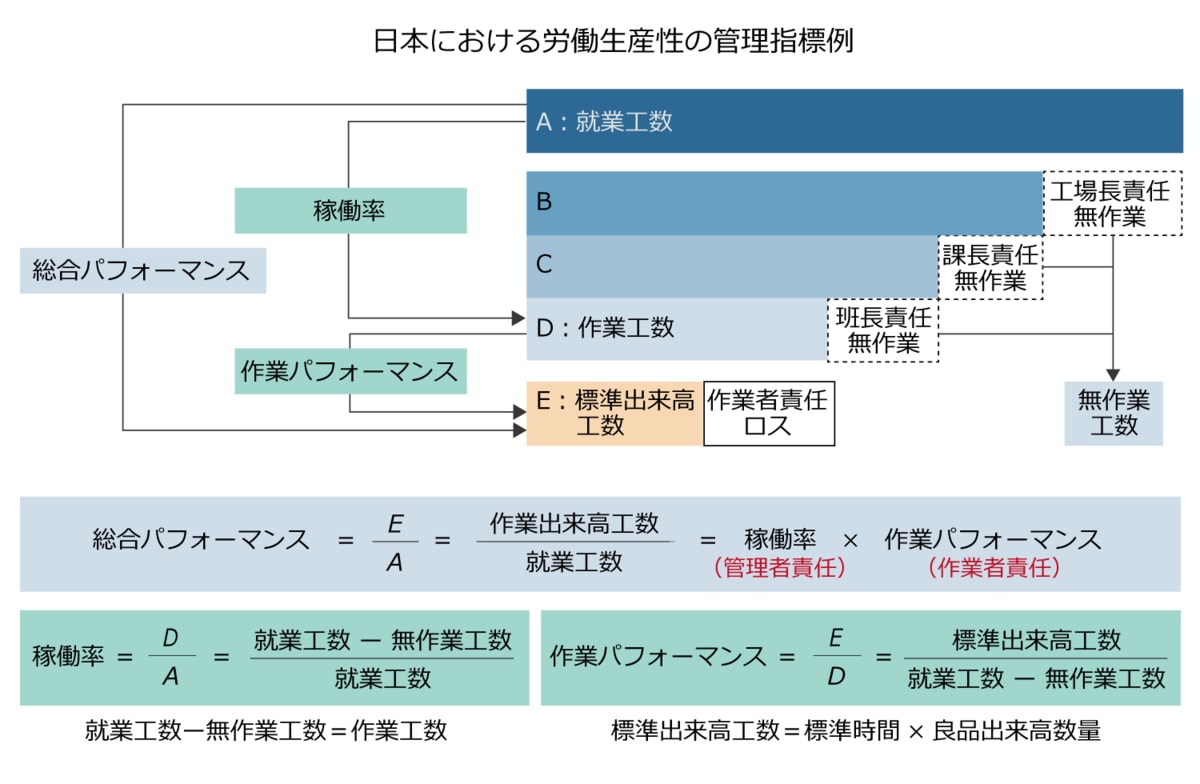
管理指標については、各指標の定義や収集の目的など、現場の人との共通理解が必要であることは言うまでもない。少なくとも現地メンバーが理解できるように指標体系を整備し、継続して活用することが求められる。
グローバルに生産拠点を展開している企業において、グローバルで共通の労働生産性の指標を管理している企業もある。しかし、各拠点での管理指標の理解度・活用度については改めて検証が必要かもしれない。