シンプルで適切な発注ルールづくり!
■発注タイミングの変更
D社の発注方法は、上記の通り、発注日は個々人でバラバラ、発注量の決め方も統一されておらず、「不定期不定量」の発注方式になっていた。これを「定期不定量」に改めることを決めた。
まずは不定期だったものを毎月1回の定期とし、発注担当者が発注する日を決め、適切な発注量の決め方を定めた。
■安全在庫の設定
発注量については、全品目一律で1カ月の在庫を保有するような発注方法だったが、D社の商品は、1000種類と多品種であり、その販売量も常に変動する。そのため、1カ月の在庫を持っていても、商品によって欠品になるものもあれば、逆に過剰在庫になるものも出てきてしまう。
そこで、商品ごとに安全在庫量を設定する方法に変えた。例えば、販売量のバラツキの大きい商品の場合、安全在庫を厚めに持っておき、平均よりも多く売れたときに欠品が起こらないように対応する。逆に、毎月ほぼ平均的に販売量が推移をする場合は安全在庫の設定は少なくてよいので安全在庫はぎりぎりまで少なくし、平均的な量の発注で対応するということになる。
このような安全在庫の基本的な考え方に基づき、販売実績から統計的に算出するルールを決めるとともに、商品特性別に安全在庫の欠品許容率の設定を行った。通常、欠品率をゼロにしようとすると安全在庫は極端に多くなり在庫が増えることになるため、在庫削減のために商品別に適正な欠品率を設定することが求められる。
■在庫削減を実現する
まずは欠品を防止することを主眼として定番等、月販量が多い売れ筋品は欠品許容率を低くすることで安全在庫量を増やした。逆に、月販量が少なく代用品を充てて欠品による顧客への影響を最小限にできる商品は、欠品許容率を高くして安全在庫量を減らすことで、全体の在庫量を少なくした。
その方針に従い、在庫管理システムから売上量・仕入量・在庫量のデータを月別・商品別に抽出し、過去の傾向から統計的に商品ごとの発注量を算出できるようにした。
■手計算からシステム化へ
海外仕入品に頼っているD社では、1000種類それぞれの発注量を算出後、仕入先別にコンテナ単位に発注量をまとめる必要があった。コンテナ単位にまとめるために、どの商品をどのくらい増減させるかを自動的に計算して、発注量を決められるようにした。従来はこれらを手計算で行っていたために非常に時間を要していたが、システムで自動的に算出できるように改良し、結果的に発注業務の効率化にもつながった。
上記のルールに基づき、仕入担当者は発注日を確実に守り、計算された発注量にて発注を行った。これまでは不定期の発注であり、仕入先と取り決めた納入LTより短い納期での発注も見られ、仕入先も納期を守ることが難しくなり、結果として欠品につながるケースも目立っていた。
つまり、D社自身が仕入先との約束を守れていないこともあったというわけである。D社自身が納入LTを守った発注を確実にすることで、納期順守率の向上のために仕入先への働き掛けもできるようになった。
このようなシンプルなルールを決め、それを確実に守ることにより、欠品は定番商品ではほぼなくなり、在庫は従来の約30%削減をすることができた。また、業務の混乱も解消し、効率化も実現した。
次回は、 品質(Q)面:「クレーム対応レベルの向上とクレーム削減」について紹介する。
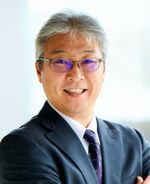
コンサルタント 角田賢司(つのだ けんじ)
生産コンサルティング事業本部
プロセス・デザイン革新センターセンター長
兼 デジタルイノベーション事業本部 シニア・コンサルタント
IEをコア技術として収益向上のコンサルティングに取り組んでいる。自動車(部品)、化学プラント、樹脂成型、建材、食品等、多業種で収益向上の支援を実施。現場の生産性向上、品質向上、調達コストダウンや在庫削減等複数テーマを同時に展開、マネジメントの支援を行う。近年はタイ・中国等の製造拠点支援として生産性向上や品質向上の成果実現と併せ、マネジメントの仕組みづくり、ローカル人材育成を実践