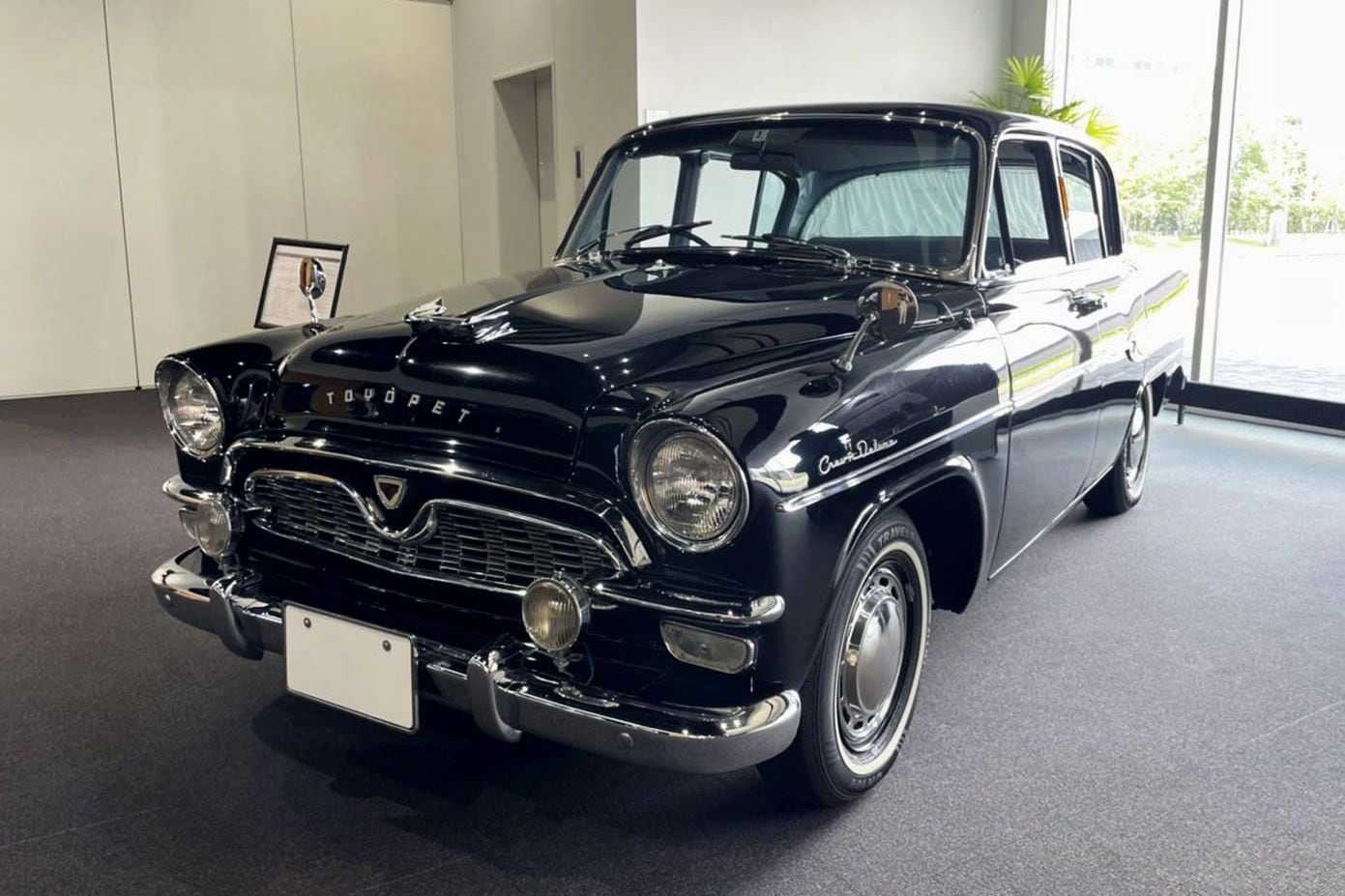
写真提供:共同通信社
「ものづくり大国」として生産方式に磨きをかけてきた結果、日本が苦手になってしまった「価値の創造」をどう強化していけばよいのか。本連載では、『国産ロケットの父 糸川英夫のイノベーション』の著者であり、故・糸川英夫博士から直に10年以上学んだ田中猪夫氏が、価値創造の仕組みと実践法について余すところなく解説する。
今回は、1990年代からDXを先取りしていたトヨタ製品開発システムの独自のプロセスを紹介する。
同時並行で製品開発を行うトヨタのシステム
トヨタ製品開発システムでは、設計変更の容易性と開発リードタイムの短縮を実現するため、基本的にフロントローディング(早い段階)で各工程が同時並行で行われる。
例えば、グローバルモデルのカムリのチーフエンジニア(CE)だった北川尚人氏がCEを務めた若者向けのbBの開発(第8回参照)では、各工程を司るそれぞれの部門(車両実験部、生産技術部、工場検査部、原価計算経理部、仕入れ調達部)が大部屋に集まり開発を行った。
3次元にデジタル化された設計データや部品データをコンピューター上で仮想に組み立てる自社開発ソフトウエアV-Comm(Visual & Virtual Communication)を使いながら、CAE(Computer Aided Engineering)で流体解析や熱解析などの性能シミュレーションを行うことで、試作レスを実現し開発費を半減した。最近のDXブームで実現したのではなく、なんとトヨタでは、1990年代後半にすでにこれを実現しているのだ。
このようなサイマルテニアス(同時並行)の開発を行うトヨタ製品開発システムを、第12回で紹介したMOT(技術経営:Management of Technology)の「研究」→「開発」→「事業化」→「産業化」という直列プロセスにマッピングしてみる。