デジタルツインの導入により稼働率を高めても渋滞しない「協調型スマートファクトリー」を実現
――今後日本企業が現場でデジタル技術を活用する上で、どのような戦略が考えられるのでしょうか。
藤本氏 これは、私の分析枠組(図4)では➁「地上戦略」にあたる話です。例えばデジタルツインを活用し、「設計の比較優位論」からみて競争力の維持が期待できる「変種変量変流生産*による複雑な擦り合わせ型製品の開発・生産」などを国内工場に集中させ、国内生産能力が不足なら一部を海外生産拠点で補完し、アジアを中心としたグローバルサプライチェーンも活用する戦略が有効です。
*変種変量変流生産=生産する品種・生産量・流れが変動する生産方式
日本企業は、特にエネルギー、環境、安全基準、小型化・軽量化要求など、物理的な制約条件が厳しい製品の製造で、長く優位を保ってきました。擦り合わせ型製品でよく使われる専用設計部品・専用生産設備の変種変量変流生産は、日本企業が得意とする分野ですが、最適設計では製品ごとの部品設計が異なることが多く、共有部品や標準部品として大量生産することは容易ではありません。また、変種変量変流生産は、いつどこにボトルネックが発生するかが予見しにくく、稼働率を少し上げただけでどこかに仕掛品の渋滞が発生し、納期遅れの原因にもなります。
しかしリアルタイムで現在の工場の「流れ」を完全に写し取るデジタルツイン、そしてAIによる「流れの画像認識」などを活用すれば、広域の流れのリアルタイム把握、1時間後の流れのシミュレーション予測、流れの即時修正などが可能となり、稼働率を上げても渋滞が発生しなくなります。
例えば、工場の1階(生産現場)、2階(全体の流れのコントロール室)、3階(工場長・社長室)の各所で100インチなどの巨大モニター画面で列車のダイヤ図のような時間流れ図(図6)が見えており、それが10秒ごとに更新されてアニメのように動き、作業現場やコントロール室の人々がAIなども交えてこれを見ながら相談し、現在、1時間後、半日後などの「良い流れ」を作っていくイメージです。
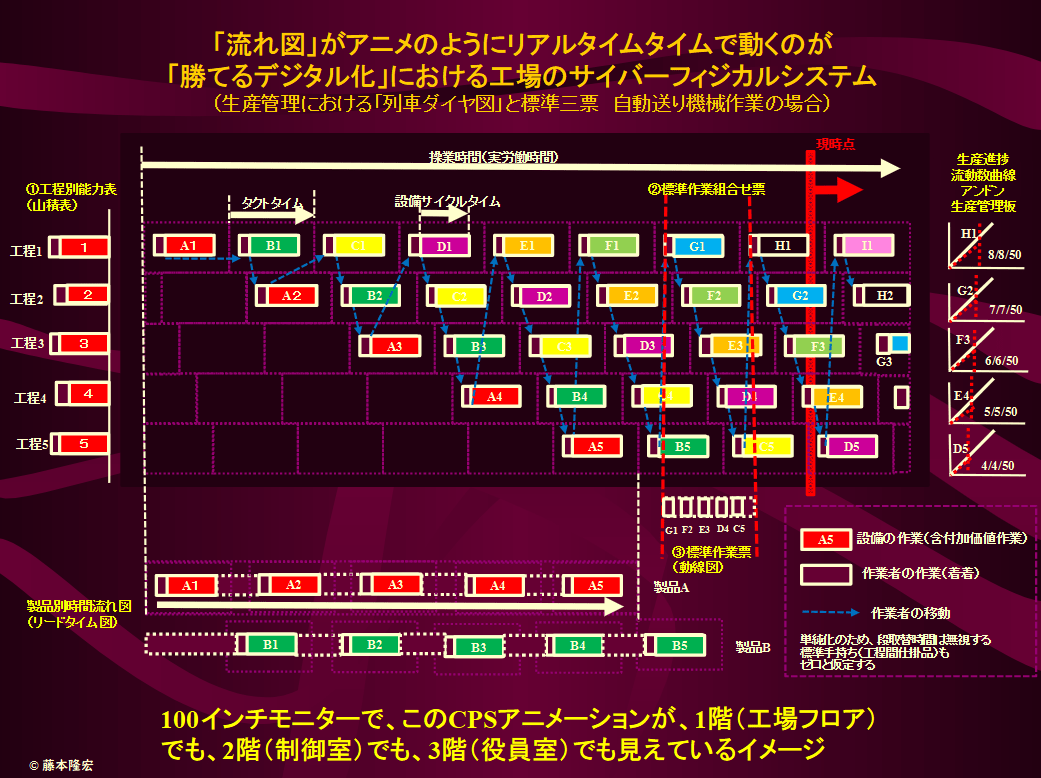
拡大画像表示
サプライヤーからの部品等の流れも含めて、広域で連携可能なこのような「協調型スマート工場」による高品質・高生産性・短リードタイムの変種変量変流生産が実現すれば、他国の企業や工場は追随できなくなる、あるいは面倒くさいので日本にまかせるようになるでしょう。