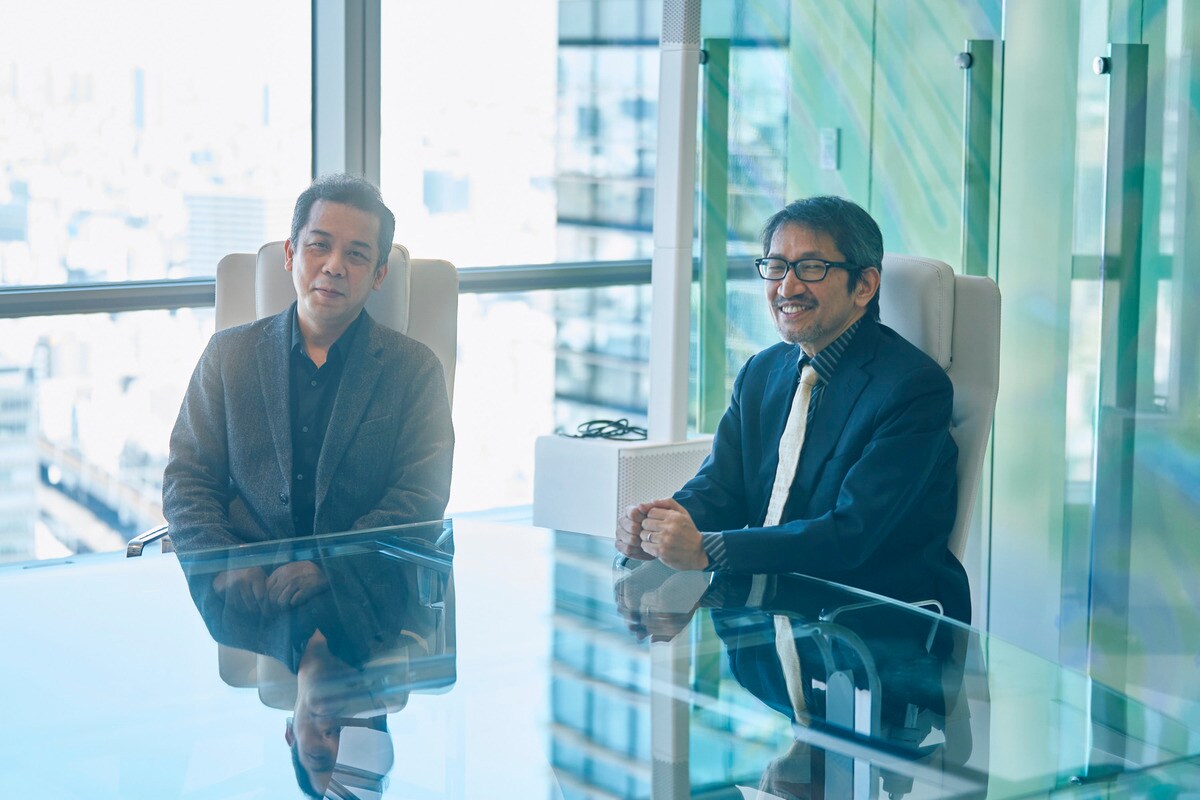
新型コロナウイルスの出現は製造業にも課題を投げかけた。従来のように製造現場に行くことが困難になった際に、事業を継続させる鍵となるのはデジタルの活用だが、そこには製造業特有の難しさが立ちはだかる。それをどう乗り越えて製造業の未来を切り拓くのか。製造現場からみたボトムアップのIT化を推進する団体「IVI」の理事長を務める法政大学教授の西岡靖之氏と、製造現場でのAI活用を推進するNTTコミュニケーションズの伊藤浩二氏が議論を交わした。
想定外が連続して起きる現場はデジタルでの再現が難しい
――製造業においてもDXが求められていますが、どんな課題があるのでしょうか?
伊藤浩二氏(以下、伊藤) 化学業界の製造現場にAIで新たな価値を提供したいと横河ソリューションサービス株式会社様と協業して取り組んできましたが、困難の連続です。当初は、プラントそのもののデジタルツイン化を試みたのですが、道半ばです。
反応器の内部状態を、AIで再現しようと試みましたが、蒸留塔などの比較的単純な工程と異なり、反応器の内部は非常に複雑であり、運転中のデータを使ったデジタルツイン化は非常に困難であることがわかりました。しかし、そのような場合でも製造現場の反応器の運転員は、過去の経験を踏まえて状況に応じて適切に対処することがわかりました。
現在、プラントそのもののデジタルツイン化ではなく、運転員の運転技術のデジタルツイン化を行う、「AIプラント運転支援ソリューション」を開発し、実現に向けて挑戦してしています。ただ難しい点は、どこまでAIで再現できれば価値を提供できるのかというところです。
西岡靖之氏(以下、西岡) 再現できるギリギリまで挑戦してもまだ課題が残るという点には共感できます。それほどプラントのデジタルツイン化は難しいです。7割~8割を再現できたとしても、肝心なところが再現できなければ意味がありません。
伊藤 確かにそうですね。将来の適切な運転方法を先読みし推薦するためのモデルを作りましたが、運転の2割~3割の部分はモデル化できませんでした。AIは定常運転のもとでなら有効に機能するのですが、製造現場には通常と異なる操作をしている場合もあり一筋縄ではいきません。
――製造業を営む企業は、デジタル技術に対してどのような姿勢で臨むべきなのでしょうか。
西岡 デジタルツインには2つの目的があると考えています。サイバー空間上にリアル空間と同じものを作ってシミュレーションすることと、リアルタイムにデータを吸い上げてモデルを更新しながら現実を共有することです。
どちらも正しい方向ですが、継続的な改善が必要です。製造現場は例外の塊です。想定外のことが起きた場合に対処することが人の役割です。つまり改善の世界なのです。
伊藤 私もプラント自体のデジタルツイン化には更なる技術の進化が必要だと考えます。反応器の運転員のスキルを複製することはできますが、現場は絶えず変化するため、その複製が陳腐化してしまう点が難点です。
そこで、人の知見を常に吸収してモデルが生まれ変わり続ける技術を開発しています。
ところがここにも課題があります。人は一つ教えると、それを様々な状況に展開できます。ところが、極端な例ですが、AIは一万個教えて一つを理解します。これでは人をAIが追いかける世界となってしまいます。
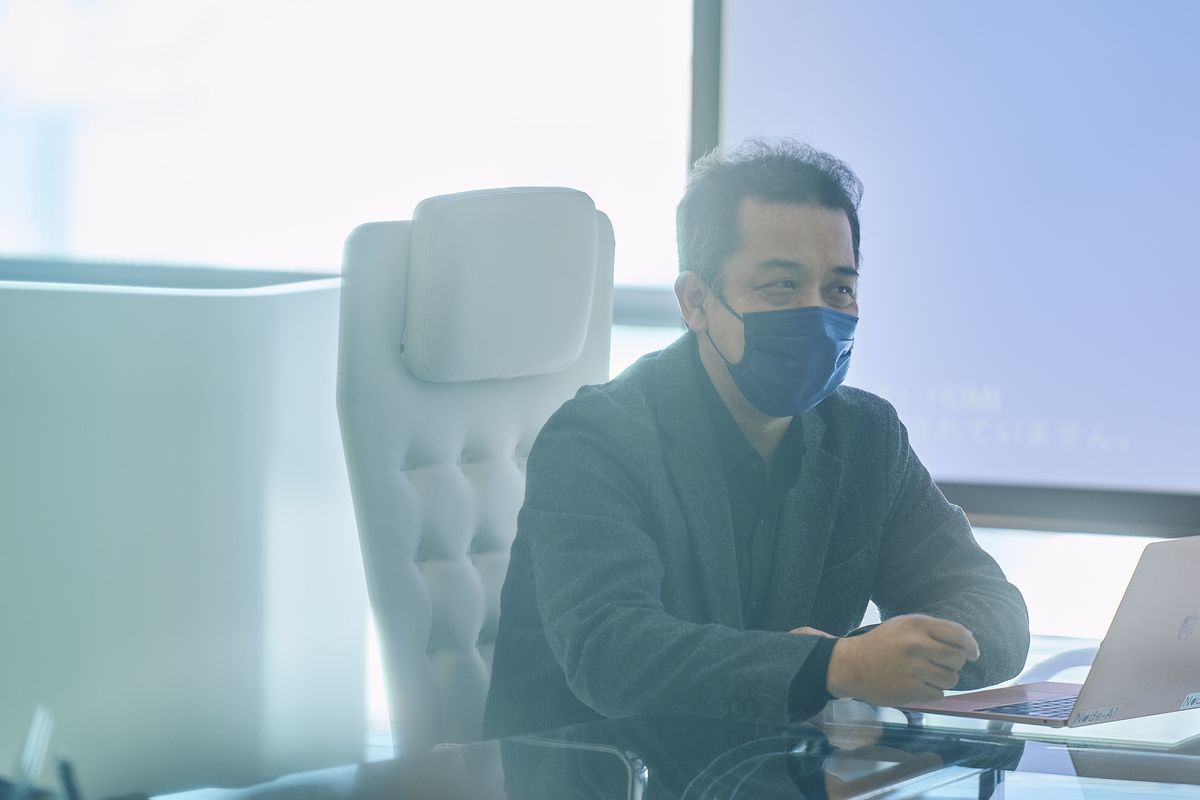
西岡 なぜAIの実装に費用がかかるかというと、モデルを更新するためにAIの技術者が必要となるからです。
コミュニケーションによってDXの化学反応を引き起こす
――製造業のコアコンピタンス強化を後押しするためのDXというと、具体的にはどのような取り組みが考えられるでしょうか。
西岡 現場の個別性にフォーカスすべきです。これまでDXの推進が難しかった背景には、デジタル化の環境が発展途上にあったため、個別性のある部分については人が対応した方が効率的だったからです。
しかし、これからは個別性のある部分についても、デジタル化が可能になっていきます。この個別性を際立たせる使い方へとシフトするべきです。そうなればリアルとデジタルのギャップが少なくなり、デジタルへの違和感が消え、現場にとっても活用しやすいDXを実現できるでしょう。
伊藤 私たちが現場とのコミュニケーションを効率化するために提供しているのが「Node-AI」です。これは、コミュニケーションを通じて現場の知見を高速に取り込むものです。
現場力は日本の製造業の強みです。海外と比較すると、日本の化学プラントは細やかな運転を行い、原材料を効率的に使用しています。それをAIでモデル化し技術伝承に活用できないかと検討しています。
西岡 日本の製造業の強さは柔軟な現場力によるところが大きいですが、さらに変化に機敏に対応できるよう、デジタル化で現場力を絶えず高めていく必要があります。
昨今は、デジタルツールで表現された現場の言葉を、企業内外の「共通言語」として活用しようというサイクルが回り始めました。現場こそが新たな価値を生み出す起点です。ここにスポットを当てることで、日本の製造業の価値全体を押し上げることができると考えます。
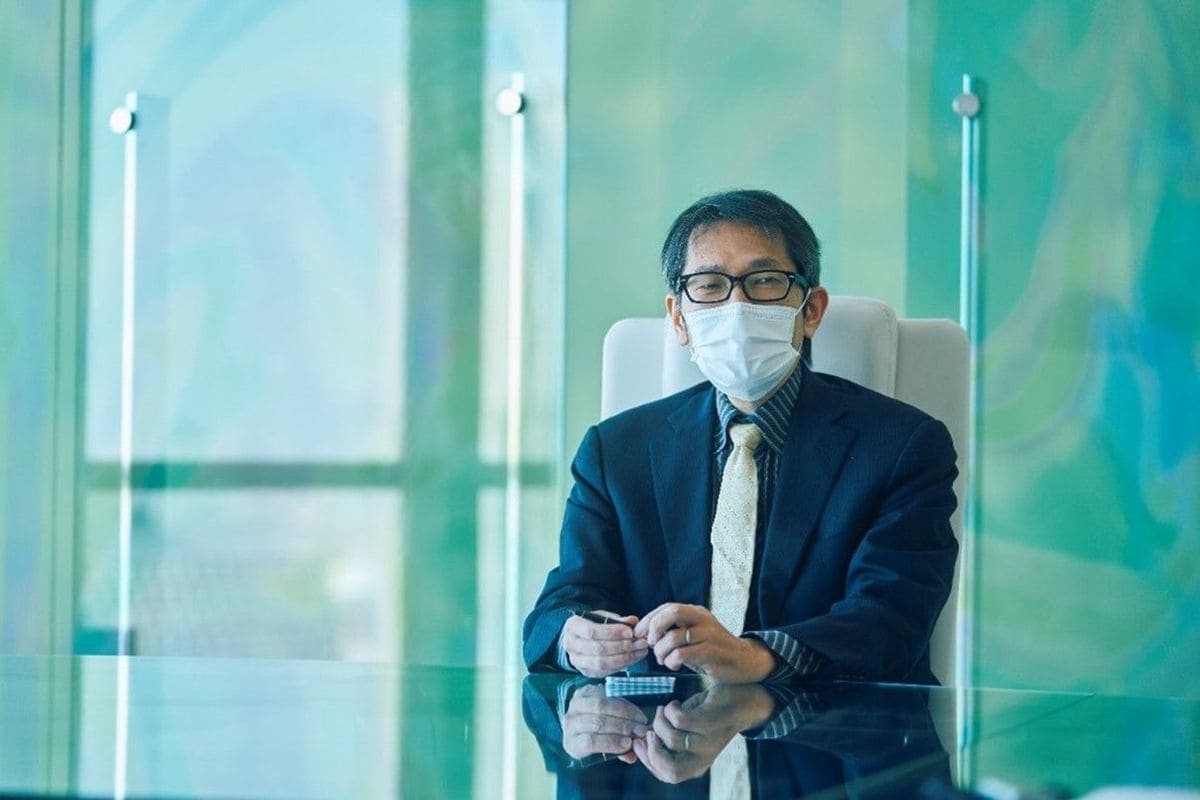
伊藤 データを各工場内に閉ざさずに、工場同士をつなげることで、スキルトランスファーにも活用できるようになるはずです。
西岡 80年代は品質管理とオペレーションが製造業のコアでした。それがAIなどのテクノロジーに置き換えられきました。今一度、オペレーションをコアととらえることで、企業価値を高めることができます。
日本の企業には成功事例や課題がたくさんあります。それらをデジタルでつなぐことで素晴らしい化学反応を起こせます。デジタルによるスマートシンキングです。
デジタルで工場間をつなげると、蓄積されたノウハウの検索が可能となることに加えて、他の工場にも展開できます。それぞれの状況を加味したコンテキスト依存の知識のほうが、かえってリアルな本質を伝えられるというメリットも期待できます。
ゆるやかな標準化を推進し枠を超えてつながる世界を
――西岡先生が2015年に立ち上げた「インダストリアル・バリューチェーン・イニシアティブ(IVI)」では、どのような活動に取り組んでいるのでしょうか。
西岡 IVIが目指すのはつながる工場です。これまでは、異なる現場をつなげるためには、標準化が必要でしたが、製造現場で標準化を推し進めようとすると、それに対する反対も少なからずあります。そこで、現場としても受け入れやすいよう、帳票や画面、仕事の流れなどを急激に変えずに、緩やかに変えていこうと考えています。
伊藤 AIは、それが生み出す結果が人の感覚と合っていれば評価され信頼されます。その観点で、人とAIの感覚を近づける仕掛けが重要です。現場と感覚を合わせる仕組みまで作り、活用を広げていく必要があります。
西岡 複数の工場のコアがつながると、ビジョンがより強化されます。工場は個別に最適なものづくりを目指してきましたが、自前主義が行き過ぎると、つながらない工場になってしまいます。「つながらないと危ない」という考え方を伝え、デジタル化の土台を作っています。
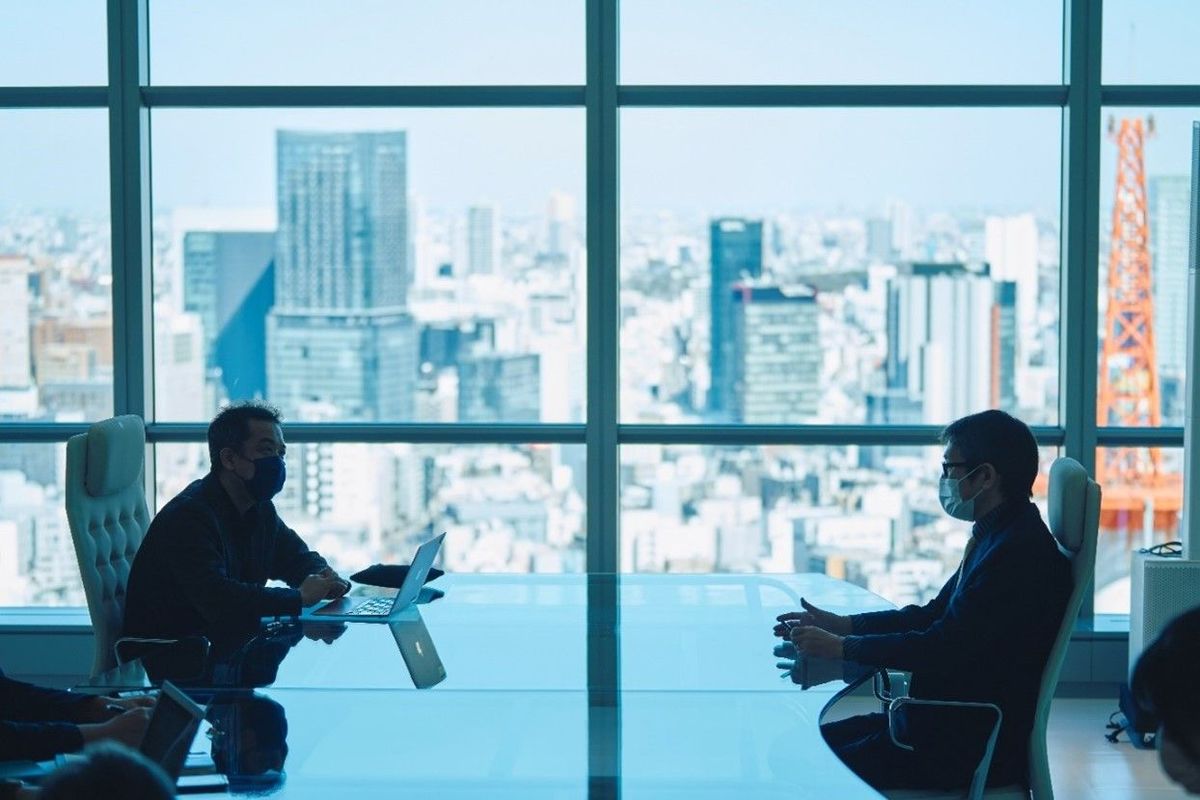
――AIやその他デジタル技術によって、製造業の未来はどのように変わっていくのでしょうか。
西岡 2030年には工場は3つに分類されると考えています。1つは消費者に近い場所に設計図データを転送して3Dプリンティングによる部品製造や組み立てなどの最終工程を手掛けられる「コンビニ工場」です。2つめが専門性が高く大規模な投資が必要な特定の製造工程に特化して請け負う「シェアリング工場」です。そして最後がコアコンピタンスに関する製造知識やノウハウといった知財を強みとして系列などを超えて自在に他の製造業とつながる「コネクテッド工場」です。設備ではなく要素技術をネットワーク化することで、新しい加工技術を取り込み多様なニーズに対応できるようにします。その前提となるのがデジタル技術やコミュニケーション技術です。
伊藤 化学コンビナートは今でも物理的につながっていますが、アナログで計画していたことに起因して効率化の余地もあるはずです。デジタル技術でより効率化を進めることができるのではないでしょうか。
西岡 また、今、IVIが注目しているのはカーボンニュートラルです。それに取り組むことで取引が拡大するのであれば、
<PR>