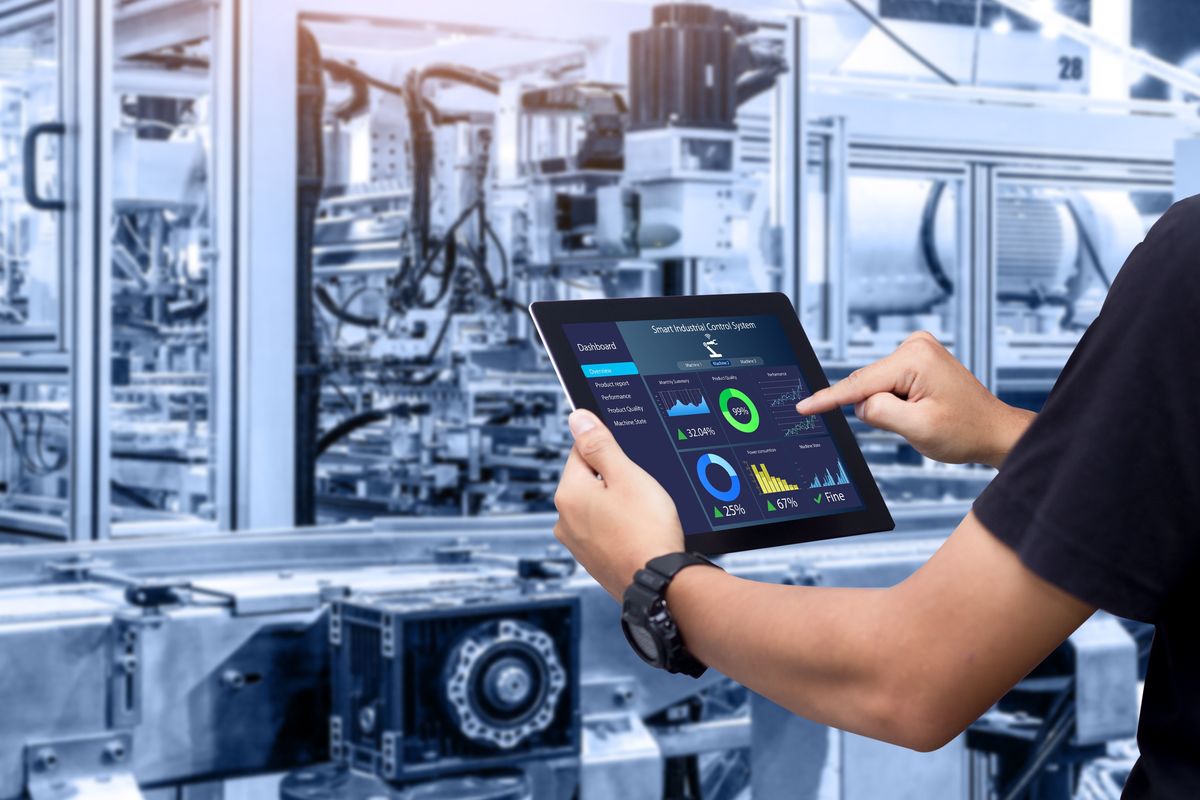
「製造現場には魔物が潜む」。とある製造業のライン長がおっしゃった言葉だ。安定稼働している時には心配は不要だが、いざトラブルが起こると、復旧までに時間を要してラインの稼働率が著しく低下。事業インパクトに直結する納期や品質問題に発展する危険性がある、というのだ。
連載の第3回では、こうしたリスクを未然に防ぐ製造現場の可視化について解説したい。
見えていない現場の課題
スムーズに生産している際には何も問題が無いように見える製造現場でも、実際には(発生頻度はばらばらだが)、さまざまな課題が生じている。それを「全体俯瞰して見えていない」ことが、さまざまな問題の引き金になっている。
・実は現場は分かっている
「見えていない現場」に言及するところから始めたが、現場の作業者たちに、現場で発生する課題が見えていないわけではない。日本の製造業で最も多い金属加工業の工場などでは、現場作業者は長年の勘と経験でおおむね、どの作業工程でどのような品質ロスや設備のチョコ停が起こるかくらいは分かっている(それすら分かっていないとするとそもそも稼働率が悪過ぎて生産が成り立っていない)
ただでさえ、「生産性改善・品質ロス低減・無事故安全」を長年掲げてやっていればさまざまな工夫を通じて個々の担当現場は属人性含めて最適化されているものだ(その属人性が、生産人口が減少して新規雇用ができなくなり技能継承面からも大きな課題になっているわけだが・・・)
・管理者からは見えない現場
では、なにがどう「見えていない」のか。現場を管理するライン長ならまだしも、建屋が離れた複数の加工工程からなる工場の場合には、前工程と後工程、工場長や管理部門、離れた所にある本社と、現場から離れれば離れるほど、現場の実態が見えなくなってくる。
報告を受けたり、人づてに聞いたり、生産管理システムを確認したりしなければ生産数量や稼働率、サイクルタイムやスループット、歩留まりといった重要な指標が見えてこない。そして、生産現場が意外にも何度も止まっているという事実が把握できない。生産現場に行けばすぐに分かる、定期的な保守・保全以外のチョコ停が多発しているという事実が、「見えていない」のだ。
・スループット最大化が理解できていない
たくさん作れば良いという大量生産の時代はとっくの昔に終わっており、現在の金属部品を製造する金属加工業の工場などでは、生産するモノの品種も増やしつつ、それぞれの品種については定められた数量を安定的に作り続けられることが求められている。
安定的に作るためには工程全体を俯瞰して、どこかに設備や人の稼働が低下しているボトルネックがないかを発見して、部品や製品が1つ出来上がる時間(サイクルタイム)を最小化することが求められる。
そして、最終的には工程全体のリソース(設備や人の稼働)をいかに短い時間しか占有せずにモノを作ることができるか、というスループットの最大化を目指すことが重要になる。
だが、現場・管理者・経営者がこのことを理解できていない(見えていない)ことが多いのだ。