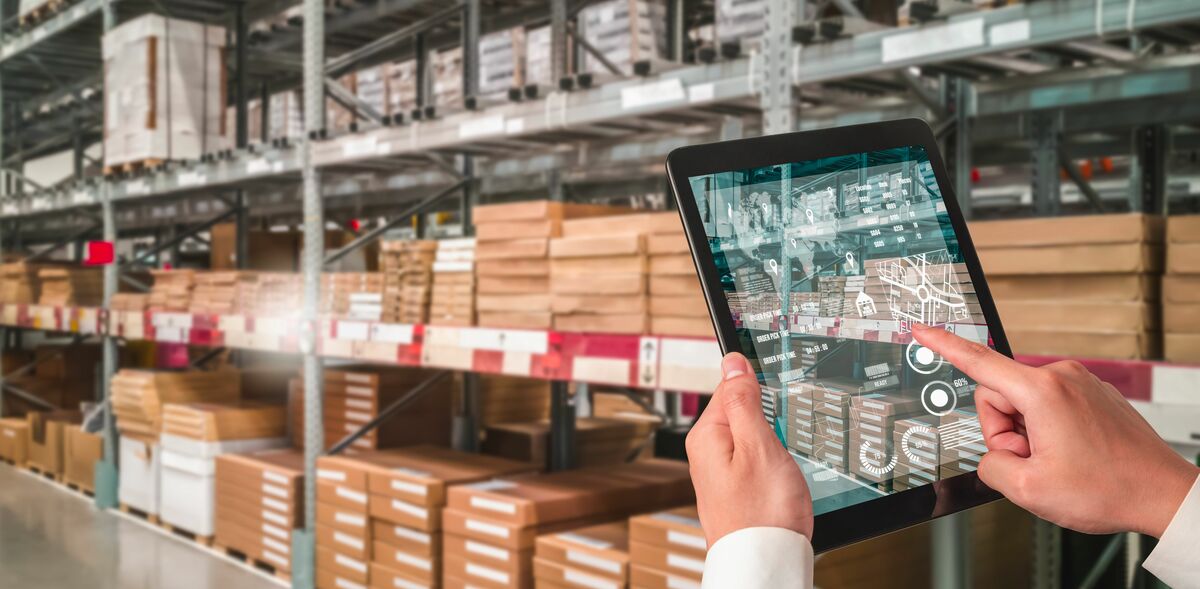
いつの間にか安全在庫が”安心”在庫になってしまうのはなぜか
在庫は、製造業には欠かせないものである。見込み生産の会社では、製品在庫を持ちながら、顧客からの注文に対応する。受注生産であっても、多くの会社は共通となる原材料について、あらかじめ在庫を持っておく。
生産管理や購買の担当者にとって、在庫は身近な存在であり、日々在庫状況を確認しながら、生産量や発注量を決めている。そのため、どれだけの在庫を持ちながら運営していくのかは、生産管理や購買の担当者に任されていることが多い。
一方で、生産品目や調達品目が多岐にわたると、人手では、一品一品まで詳細に確認しながら必要量を手配していくのには限界がある。そこで、ERPや生産管理システムといった情報システムを用いて必要量を計算している会社もある。その場合でも、人手の時と同様に、担当者の判断で安全在庫の基準を決めて、システムに計算させていることが多いのが実態である。
このように、担当者の判断に基づいて在庫水準を決めていると、需要側・供給側で起きているざまざまな状況変化を踏まえて柔軟に対応できるというメリットがある。しかし一歩間違うと、担当者の独断で必要以上に先行して在庫を確保してしまうことや、需要側の急変に対応できないといった事態になりかねない。
実際ある会社では、資材調達担当が現場からの欠品に対するクレームを受けて、その後必要以上に先行して在庫を発注し、製品終売により、大量に部品在庫を余らせてしまうといった事例もある。同じように、別の会社では、資材担当者が生産管理システムの安全在庫設定数を自由に見直すことができ、いつの間にか、担当者によって在庫水準に大きな差が出ていたといった事例もある。
これらの事例は、まさに本来「安全在庫」として必要な分を持つべきものが、各担当者の「“安心”在庫」になってしまった例だと考えられる。
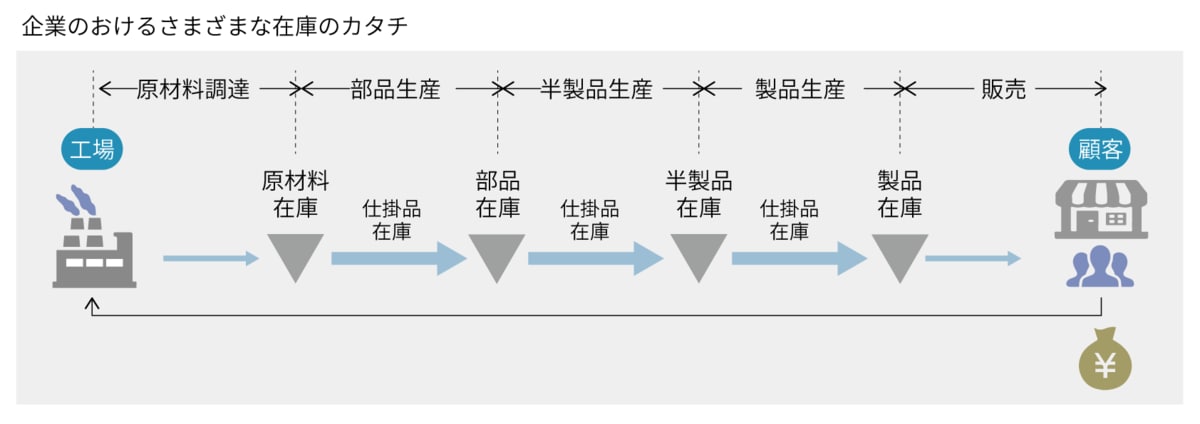