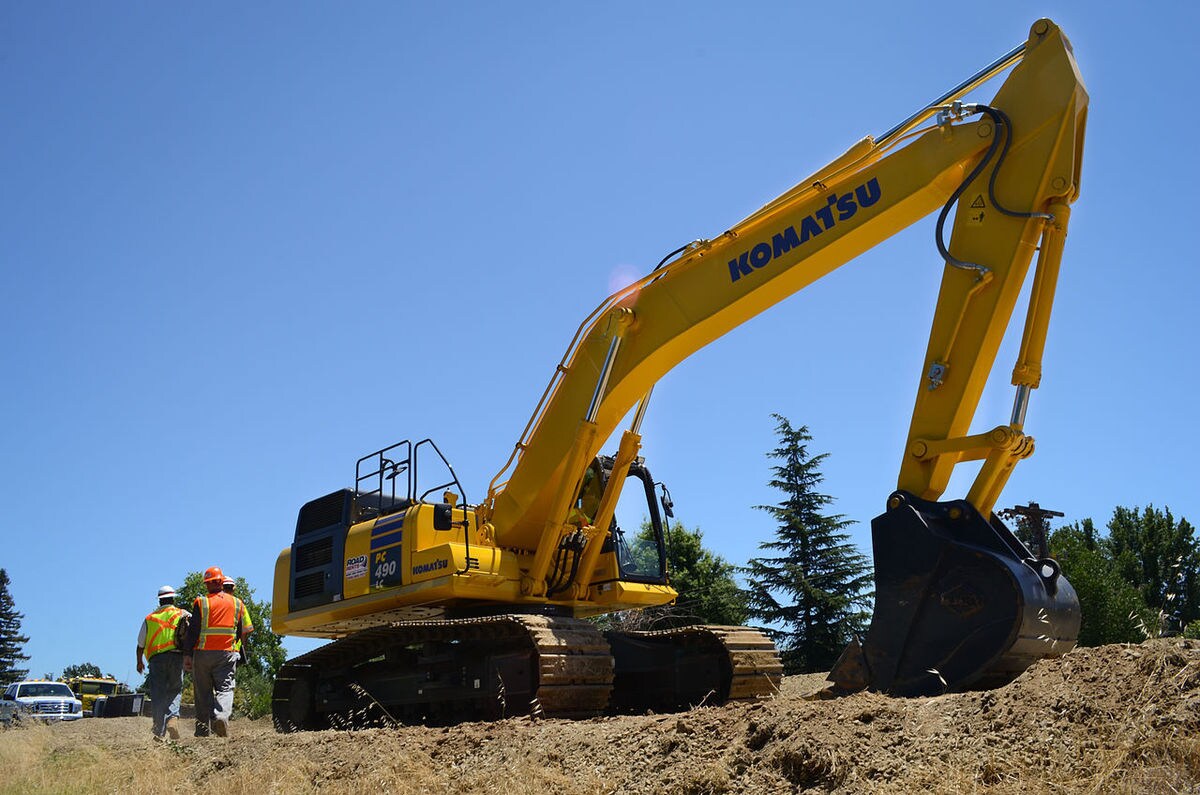
今、日本の産業界ではIoT(Internet of Things)が異常なブームである。
IoTがブームとなった背景には、モノからデータを収集するためのセンサーコストの低下、通信コストの低下、データ蓄積や分析コストの低下といった、IoTを実現する各種コストが大きく下がってきたことが挙げられる。また、インフォシス(Infosys)やテックマヒンドラ(Tech Mahindra)といったインド企業のように、低コストでIoT環境を整備できるエンジニアリング企業が誕生していることも見逃せない。
つながる工場とつながる製品
産業界におけるIoT活用の形態には2種類あると考えている。1つは自社工場の生産ラインや保有設備にセンサーを取り付けてデータを収集、生産性向上などに活用する「つながる工場」である。もう1つは、自社製品にセンサーを取り付けて、ユーザーが自社製品をどのように利用しているかを把握して、コスト低減や売上アップを提案する「つながる製品」である。
つながる工場については、自社で「何をやるか」を明確にできれば比較的実施しやすい(現実的には、何をやるかを明確にできずに企画倒れになる、データはたくさんあるが示唆が得られないことも多いが)。
有名な事例としては、タイヤメーカーのブリジストンが生産データや品質データを収集し、製造条件を適切に制御することで、タイヤ成型工程の生産性を2倍に高めることに成功している。また、欧州のエンジン部品メーカーでも同様に、加工条件と品質の関連性を分析。全工程で良品条件を満たしていれば検査工程を省略することで、検査コストを削減することに成功したと言われている。
一方、「つながる製品」についても、GEの航空機エンジン事業や小松製作所(コマツ)の「KOMTRAX(コムトラックス)」が収益化に成功した事例として有名である。しかしながら、ここまで成功している事例は実は多くない。