ホンダは「ホンダ0(ゼロ)シリーズ」という電気自動車(BEV)を、2026年からグローバルの市場へ投入することを発表しています。ホンダ0シリーズの「ゼロ」は、「ゼロからの発想で創り出すまったく新しいEV」との想いが込められているそうで、プラットフォームやバッテリーやモーターやデザインなど、これまでの経験や実績に、いい意味でとらわれないクルマ作りに取り組んでいます。
ホンダ0シリーズが商品となって私達の前に姿を現すのはまだ2年ほど先ですが、現時点でどんなことをやっているのか、開発はどれくらい進んでいるのか、そんな本来なら秘匿事項のような内容の一部をホンダが公開してくれました。
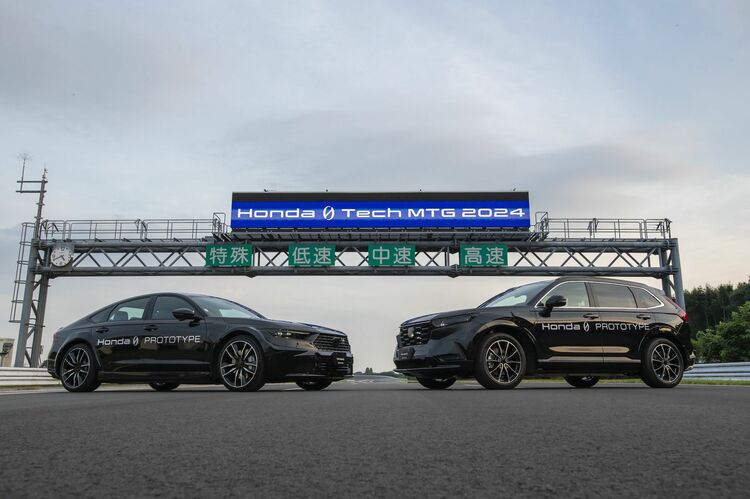
EV専用プラットフォームとe-Axle
今年の始めに米国ラスベガスで開催された“CES2024”でお披露目されたコンセプトモデルの「サルーン」は、4ドアセダンでありながら全高の低いスタイリングが特徴でした。
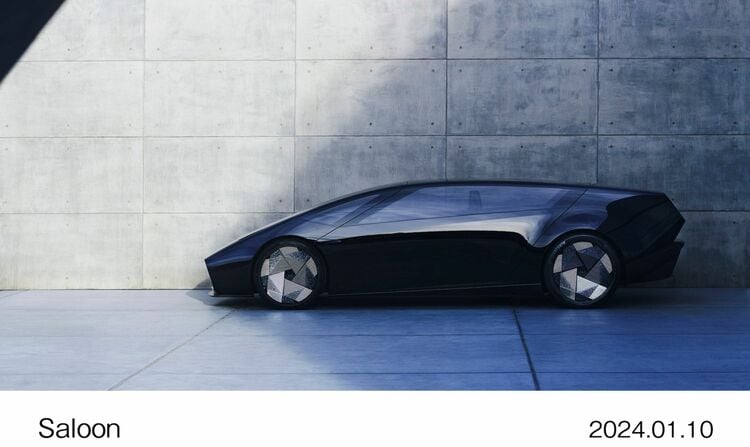
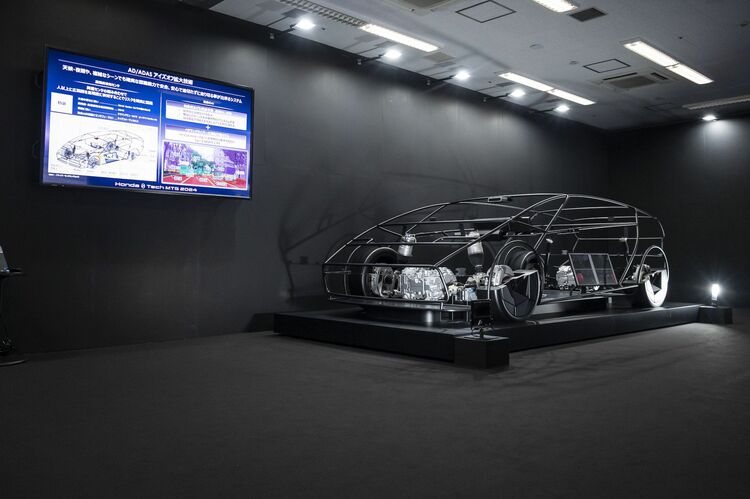
これは、EV専用のプラットフォームに2.0GPa級の超高張力鋼板を使うことなどで実現しているそうです。またホンダでは従来から独自の低床技術を構築していて、フロアを下げると同時に重心も下げ、広い室内と低慣性の操縦性の両立を実現。この経験も「サルーン」にはいかされているとのこと。
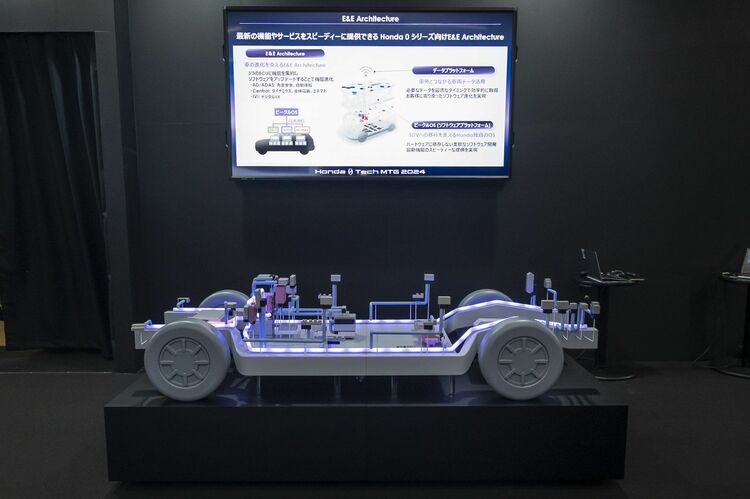
e-Axleとはモーターとそれを作動するために必要なインバータといった補機類の総称で、これの小型化に着手しています。とくにインバータは従来比で約40%も小さくすることに成功。内燃機やハイブリッドよりも圧倒的に小さいパワートレインとすることで、パッケージの優位性や軽量化に大きく寄与しています。
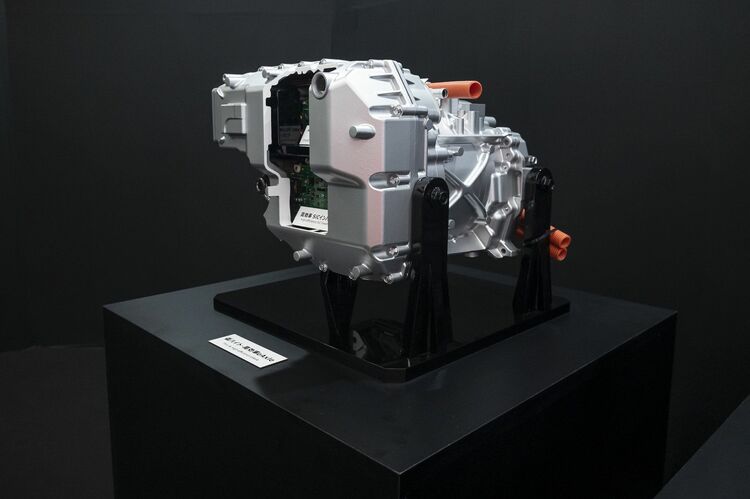
薄型バッテリーパック
重く大きなバッテリーはEV開発の悩みの種です。航続距離はバッテリーのサイズと容量に比例するわけで、極端に言えば「航続距離は2000kmです。ただしふたり乗りで荷物も積めず車両重量は3トンです」みたいな話でもあります。バッテリー自体の構造については全固体電池などの開発も進んでいますが、しばらくはリチウムイオンやニッケル水素のバッテリーが主流で、電解液を伴うバッテリーのコア部分が極端に小さくなることは見込めません。そこでホンダは、バッテリーを収めるバッテリーケースに目を付け、約6%の薄型化を狙っています。
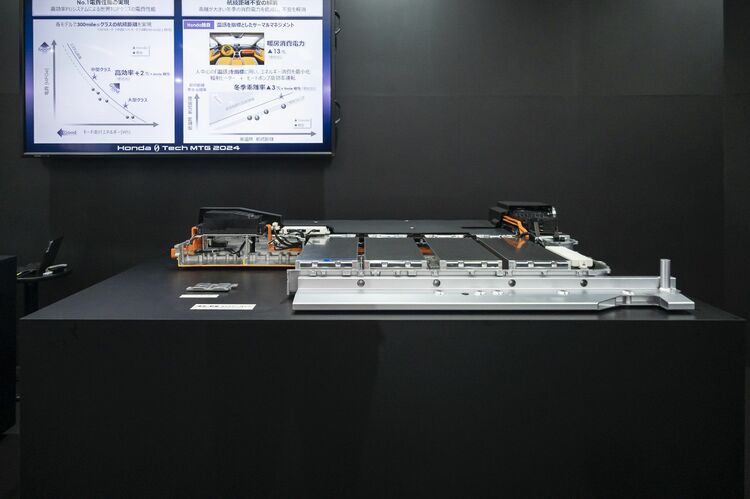
具体的には、製造ラインに6000トンクラスのメガキャスト(高圧高精度鋳造)マシンを設置し、これまで60点以上も必要だった部品点数をたった5部品へと大きく削減。モデルのサイズによって作り分けができるよう、FSW(フリクション・ステア・ウェルディング=回転力による摩擦熱で材料を軟化させ接合する技術)の締結技術も新たに採用しています。
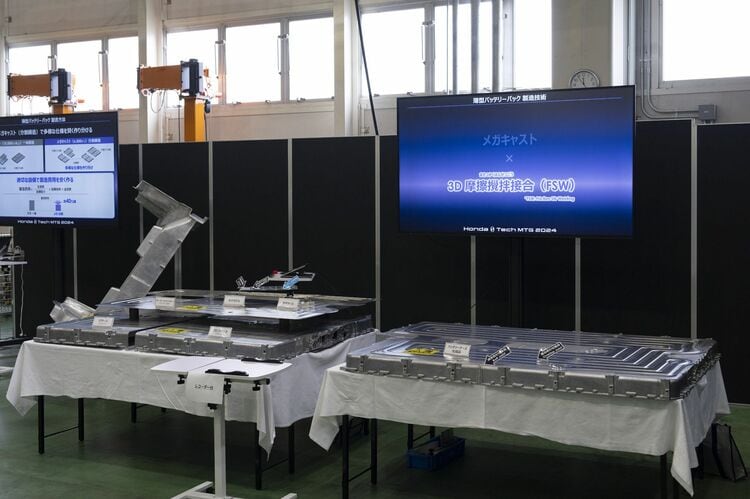
空力と操縦性を司るボディ
車高の高いSUVは空気抵抗が大きく、燃費には不利なボディ形状です。そこで、速度に応じて自動的にフロア下に設置したエアロディフレクターを作動させ、床下の空気の流れをコントロールすることにより、空気抵抗の軽減とダウンフォースの引き上げに伴う直進安定性の向上を両立させるそうです。さらに、コーナリング時にあえてボディをしならせることにより、タイヤへの荷重をコントロールしてスムーズな旋回の一助としているそうです。
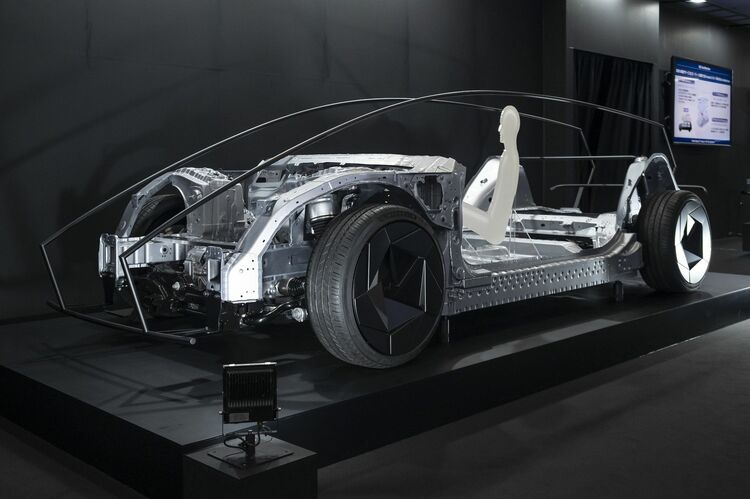