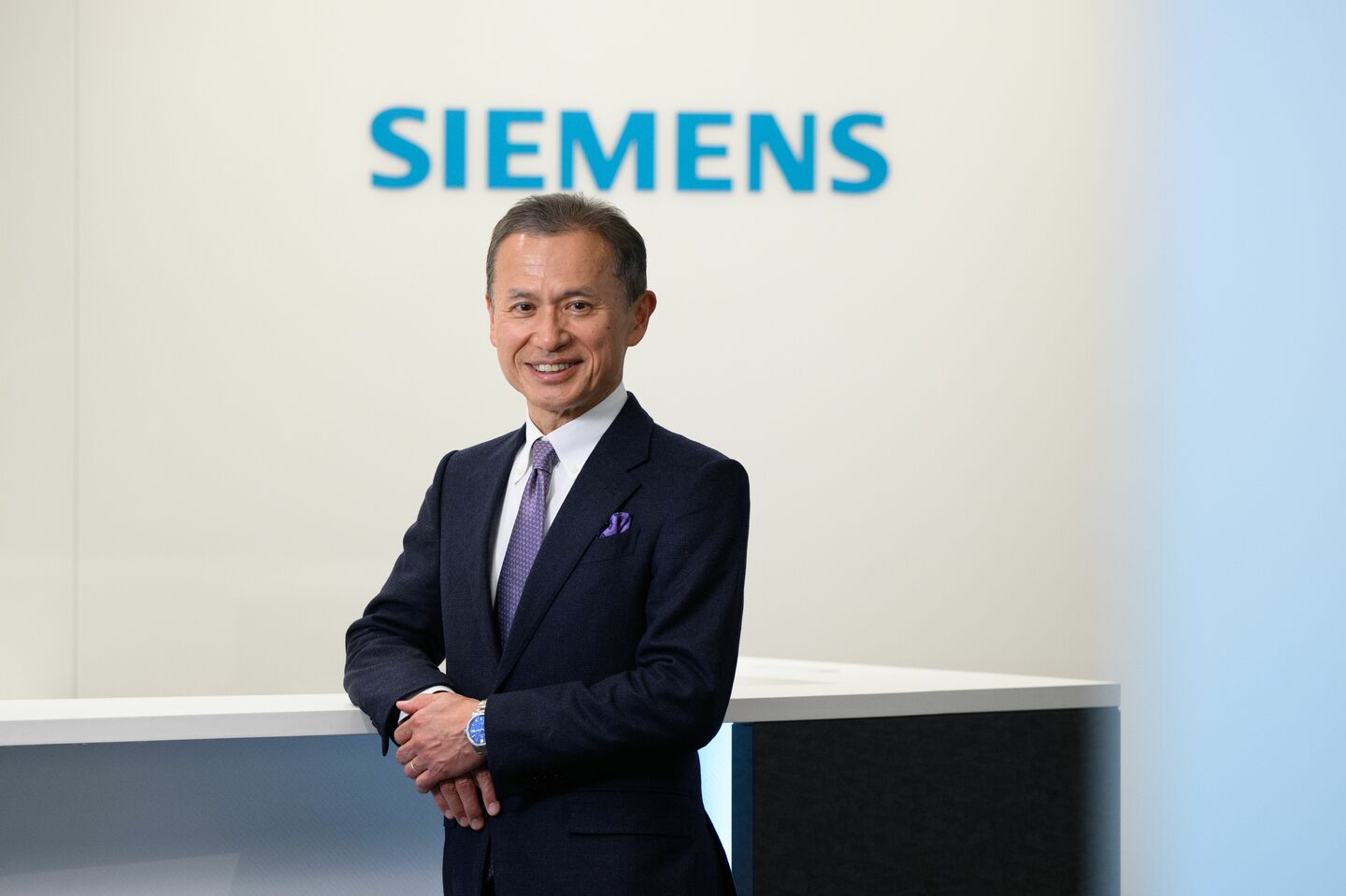
かつては栄華を極めた日本の製造業ですが、近年は、欧米や中国企業のようにデジタルシフトできず、国際競争力が低下したと言われてきました。一方、これまで培ってきた現場による業務改善の文化や従業員のリテラシーの高さについては、世界から再評価されつつあるという側面もあります。こうした状況を踏まえ、世界中の製造業のイノベーションを支援するドイツ発の企業、シーメンスの日本法人CEOを務める堀田氏は、日本独自の強みとデジタルを掛け合わせた“日本流”の戦い方をすれば「新たな道が開ける」と語ります。
本記事では、同氏が製造業の発展に不可欠なProduct Lifecycle Management(以下、PLM)の歴史を解説しながら日本の製造業が進むべき道を説きます。
・PLMが生まれた歴史的背景(Play back to 1980)
・日本と世界のPLMの動き(Play back to 1990)
・データと経営の連動
・グローバル化の波(Play back to 2000)
・カスタマイズからFit to Standardへの移行(Play back to 2010)
・データ連携の本格化(現在の潮流)
・これからの日本の戦い方
・日本のDXのパターン
・Digital Twinの社会実装
PLMの原点
PLMは、製品のライフサイクル全体を管理するためのシステムやプロセスを指しますが、これを分解すると、その大枠はCAD・CAM・CAEそれぞれから生み出されるデータの管理という要素で構成されています。その中でも1980年代初頭より、機械設計をする上での強度や、流体の流れ、自動車の振動・騒音などコンピューター上で解析を行うCAEの領域が急速に発展していき、そのデータの管理の必要性が高まったことがPLM発祥の起源とも言えます。
PLMが生まれた歴史的背景(Play back to 1980)
前述のCAEによる、分析領域が急速に発展した背景に、パソコンやワークステーションの台頭があります。橋や列車、飛行機などの技術による交通インフラの発展やロケットに代表される宇宙開発という分野では、「試しにやってみて壊れるか確認する」という方法が通用しません。そのため、事前に分析を行う必要性が高まり、スーパーコンピューターのような大型の計算機を使ったシミュレーションが活用されてきました。
その後、パソコンやワークステーションの台頭により個人の目の前にあるコンピューター計算機で、そのようなシミュレーションが出来るようになってきたことにより、コンピューター上での分析解析が爆発的に広がりました。最近、AIやWeb関連のベンチャーがどんどん出てきているように、1980年代前半にもCAE領域のベンチャーが生まれていました。 こうしてPLMで管理が必要になるデータ自体も爆発的に増えることになりました。
日本と世界のPLMの動き(Play back to 1990)
1980年代のCAEとパソコンの普及から1990年代に入り、データ連携が飛躍的に進みました。個別の設計解析という形から、解析した結果を基に形状を変え、その結果が製造に反映されていくようなデータを利用したフィードバックループに改善のサイクルを高めていく活動が普及していきました。その派生として金型を事前に3次元で設計して加工プログラムを作成するCAMの実用も進みました。また、人の動きを考慮した生産シミュレーションなど、シミュレーションの用途が拡大し、新たなベンダーが1990年代にも多く登場しました。
PLMが部門を跨いだデータ連携によりプロダクトライフサイクル全体を効率化していく礎は、1990年代に形作られました。ここまでは日本と世界が同じトレンドの中で動いてきましたが、日本と世界で大きく潮流が違う、あることもまた顕著になってきました。それは「ツールの内製化」です。ソフトウエアベンダーがプロダクトとして展開していった海外に対して、日本はそれぞれの会社が独自のツールを内製するという方向に舵を切る企業が多かったのです。
海外では当時すでに水平分業が進んでおり、日本では設計生産製造まで一貫するカルチャーが根強く、自社で現場が使いやすいシステムを開発していきました。
データと経営の連動
経営とデータの連携という観点で大きな役割を果たす3D CADソフトウエアを提供する企業が登場しました。ソフトウエアの機能そのものではなく、データが繋がることで何が出来るか、どう変わるかというストーリーを分かりやすく市場に示したのが、このソフトウエアのプロモーションでした。
経営者に対して「CAD/CAM/CAEが一体何なのか」を目の前で見せて効果をイメージさせるというプロモーションは、当時は画期的でした。
設計を変えて、そのとたんに画面に映っているキャビティの形が変わり、図面も変わる。さらにこれまで3次元のワイヤーフレームなど骨組みしか見えなかったのが、非常に綺麗な画面でデザインでも訴求する。このように、ツールの機能を「体験」させることで、単に技術的な優位性をアピールするのではなく、「相手の心に響く」アプローチが可能になりました。この手法が、データ連携の効果を伝え、浸透させることに一役買ったと言えるでしょう。
グローバル化の波(Play back to 2000)
1990年代、日本はバブルと言われた時期でした。今の若い方はイメージが出来ないかも知れませんが、土地も建物もどんどん価格が上昇し(山手線内の土地でカリフォルニア全域が買えるくらい)、銀行もどんどんお金を貸し出していました。企業もお金を使わなければいけないので、若者でも高額な提案書がバンバン通り、外車を原宿で乗り回すのが当たり前のような時代でした。
こんなことが出来た一因には、日本の自動車が海外、特にアメリカで売れに売れていたという背景がありました。カリフォルニアの厳しい排出ガス規制もあり、燃費が良くて安い日本車が米国市場で拡大した結果、今の中国とアメリカのように、高い関税がかけられるようになりました。これは当時の日本車にとって死活問題であり、日本の自動車メーカーがこぞって生産拠点・設計を米国に移し、アメ車として認めてもらうことで関税を回避し、その代償としてオレンジや牛乳の輸入を促され、小田原のオレンジ農家が打撃を受けたというような歴史もありました。
アメリカに住んでみて改めて知ったのですが、日本と違ってアメリカは1家族が車を3台~4台もっていました。やはり1台目は大きいアメリカ車を買い、セカンドカー/サードカーとして価格と燃費に優れた日本車を買うという選択でした。このように、価格転嫁が出来ない構造であったことが米国への移管の原動力になり、それが日本の製造業のグローバル化が加速するきっかけになりました。
このグローバル化の波は、必然的に日本とアメリカの同時設計を必要としたのですが、その結果、国内で各企業が独自開発していたCADを直撃し、そのほとんどが一気に淘汰されていきました。水平分業と製造業のグローバル化が進む中、国産CADはグローバルのソフトウエアベンダーの製品に置き換えられていきました。このようなサプライチェーンのグローバル化は、PLMの中でも特にPDM(製品データ管理)の機能と密接に関わるようになりました。
当時、自動車1台に30,000点ほどの部品が使われている中で、それをどこから買ってくるかというデータ管理はエクセルではできず、PLMの裾野が広がる礎が2000年代に形成されました。1990年代までの百花繚乱の時代からバブル崩壊、貿易摩擦によりグローバル化が進んだことで、日本でも2000年代には独自システムからグローバルソフトウエアに移行していきました。
カスタマイズからFit to Standardへの移行(Play back to 2010)
グローバルソフトウエアからの移行に際して、実際の現場では大きな問題がありました。業務で使う現場の方々からすれば、自身の要求を基に作ったシステムなので非常に使いやすかったのですが、それに比べるとグローバルソフトウエアは使いにくかったわけです。当時は業務をソフトに合わせるという文化がなく、多くの企業が自社のニーズに合わせてカスタマイズをしていくことになりました。
今度は、そのカスタマイズが重荷になりました。バージョンアップに時間もお金もかかり、その判断が出来ないために古いシステムを使い続けるなど、様々な弊害が顕著になり、カスタマイズから脱して、基幹システムに近いソフトウエアをコアクリーンなシステムにしていこうというのが2010年代の大きな潮流でした。
データ連携の本格化(現在の潮流)
全体最適の為にend to end でデータを繋げるというのが、現在の日本でも世界でも起きている大きな潮流となっています。
グローバルでの調達及び在庫管理を行うSCM、会計を軸にモノとお金の流れを管理するERP、顧客/市場、セールス及びサポートのデータを管理するCRM、製造実行への展開とそれに伴う5M※データを管理するMESなどが代表的でしょうか。過去それぞれの業務で深く関わる部門が導入してきたシステムをすべて連携していくことで、生産プロセスの途中の改善(変更)がお客様・ビジネスに対してどのように影響しているかを考えたり、前後の因果関係をクリアにして全体最適の打ち手をタイムリーに検討することが、現代では行われています。
※5M:Man(人)、Machine(機械)、Material(材料)、Method(方法)、Measurement(計測)
その中でも一番難しく、課題が多く残っているのが工場です。工場は歴史が長いほど現場主義で改善を重ねており、経営としても詳細が分からない中で、納期通りに予定の数量を出荷してくれれば文句のつけようがない、ある意味不可侵(神聖な領域)になってしまっているケースもあります。ただデータ連携が進むほど製造業のビジネスプロセス上、真ん中にある製造(工場)のデータが繋がらないことがボトルネックになっています。
本来はPLMを介して、部門・システム間のデータが繋がることで、設計段階で工場のケイパビリティに合わせた製造が可能になります。たとえ、過去の実績が豊富でも、一部の工場でしか取り扱えない、また、生産キャパシティの制約を受ける可能性がある形状は避けることができますし、市場流通の少ないパーツは作りません。ただし、モジュール化したパーツを外注と内製で製造することで、生産の柔軟性を高め、様々な打ち手が可能になります。実際に需要・ポートフォリオの変化に合わせて、end to endの情報を繋いで予測に基づいたものづくりをしている企業は、グローバルでは確実に増えてきています。
特に、中国の一部の企業は優秀です。過去の現場資産がなかったからというのもあるかもしれませんが、デジタルツイン、ITとOTの連携を理想的な形で(教科書通りに)そのまま実践しています。
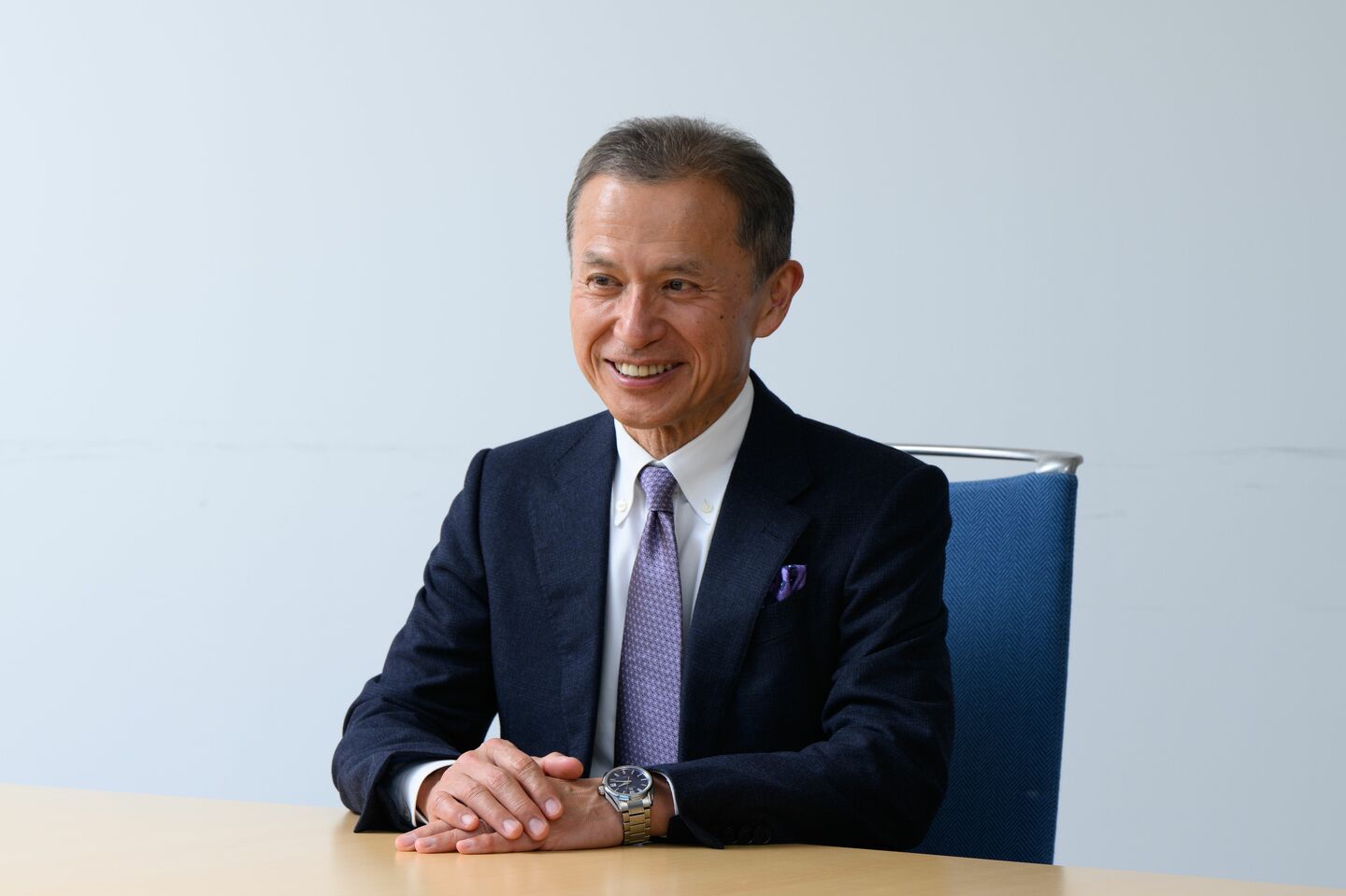
これからの日本の戦い方
グローバルでデジタル活用が進む中、GDPは伸びておらず、労働生産性も諸外国に比べて労働生産性が落ちています。過去の成功モデルが負債となって変革が出来ない、縦割りの個別最適から全体最適に移行出来ないなどの課題は事実としてあると思いますが、今後も同様かと言うと、それは違うと考えています。
その根拠のひとつに、日本はスロースタートでも、一旦動き始めればスピードと推進力が高いという点が挙げられます。最近だと「新型コロナウイルス感染症のワクチン対応はスタートが遅い」と言われていましたが、いざ始まってからは、すごいスピードで浸透していました。いかに効率的なプロセスで注射していくかを工夫して実践するにはチームワークや関係者同士のすり合わせが必要で、そのコンセンサスを取るには時間がかかります。日本には、一旦コンセンサスが形成されれば、自発的に改善を回して効率化をしていく素養があります。
別の観点で見ても、日本は先行的なプロジェクトに取り組んでいることが多いです。ただ、日本は先行的なトライアルを外部に積極的に発信する文化がなく、ともすれば隠したがる傾向すらありますが、海外はそれを積極的に発信します。これには、転職の流動性の高さが起因していると推測しています。海外では新しい取り組みと経験が新しい仕事を獲得する大きなチャンスになります。ストレートに言えば、転職に活用できるので、どんどん発信したがるわけです。
日本のDXのパターン
欧米はトップが「個別最適ではなく、データを全部連動させて全体最適をやる」と言えば問答無用でやります。トップが定めたビジョンに対してKPIを決めると、そのKPIは各部門にブレイクダウンされたうえで展開され、目標を設定していくというやり方が文化的に浸透していますし、彼らはそれを好んでいます。しかし、日本はそのやり方が好きではありません。良し悪しではなく、好きではないのです。
では、日本の改革のパターンがボトムアップかと言えば、そうではありません。日本は何を好むかというと、他の人が上手くやっているのを見ることです。つまり、成功事例が良いというコンセンサスが取れれば、一気に話が進むのです。反面、海外では成功事例を真似するのでは遅いと考える人が多いですね。さらに言えば、日本には成功事例を取り込み、ラストワンマイルで日本ならでは工夫を織り込んでオリジナルより良くする能力とマインドがあります。これも良し悪しの話ではなく、向き不向きの話であり、現場も含めて工夫して改良できるのが日本の勝ち筋だと思います。
海外では平日でも早く帰って子供とサッカーをするなど、いかにプライベートの時間を創るかという観点でのモチベーションが高く、それが生産性向上に結びついています。特に、ドイツはそれが顕著です。日本も変わってきてはいますが、早く家に帰るというモチベーションは総じて低かったと思います。必要に迫られるというのは変革にとって大事な要素ですが、今後の日本は労働力が減少することが明確なので、それもDXの強烈なドライバーになってくるでしょう。
Digital Twinの社会実装
日本のDXは、これから一気に進んでいくはずです。社会として真のDigital Twinを考えたときに、世界で最もその素養が高いのは日本だと思います。
言い換えると、サイバー空間でシミュレーションした結果を社会レベルで実践できるのは日本だけです。電車を遅らせないで運行できているのは、計画が優れているからだけではなく、運用が優れており、働く人やユーザーであるお客様のモラルが高いからです。仕事そのものに対してリスペクトが無い社会では、サイバーとフィジカルを生活レベルで融合させるのは難しいでしょう。しかし、一定レベルまでデジタルの活用が進めば、その先の世界を描けるのが日本だと信じています。