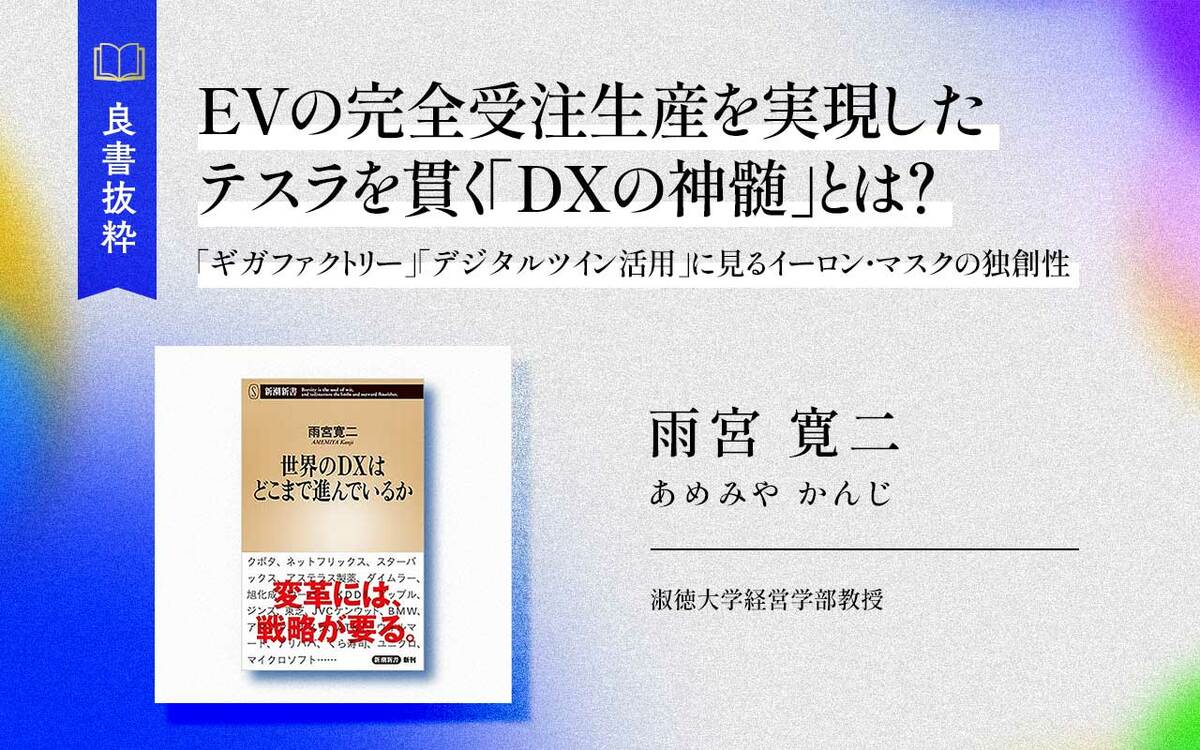
今、世界中の企業が取り組むDX。日本でも、新旧を問わず、多くの企業がDXと向き合うが、技術の導入や業務改善どまりのことも少なくない。産業、業種の垣根を超え、DXでビジネスモデルや組織全体を変革するカギはどこにあるのか。当連載は、国内外のDXの先進事例が多数収録された『世界のDXはどこまで進んでいるか』(雨宮 寛二著/新潮社)より、一部を抜粋・再編集。2030年代を見据えた「DX変革」の最前線をお届けする。
第2回目は、アメリカの電気自動車大手テスラのCEOイーロン・マスクが推し進めるDXの、先進性と独創性をひも解く。
<連載ラインアップ>
■第1回 GAFAM、ウーバー、ネットフリックス、ユニクロが実現するデジタル変革とは?
■第2回 EVの完全受注生産を実現したテスラを貫く「DXの神髄」とは?(本稿)
■第3回 AIと最先端テクノロジーでタクシー市場を変革したウーバーの革新性
■第4回 IoTとAIをフル活用、店舗を急速アップデートするウォルマートのデジタル変革
<著者フォロー機能のご案内>
●無料会員に登録すれば、本記事の下部にある著者プロフィール欄から著者をフォローできます。
●フォローした著者の記事は、マイページから簡単に確認できるようになります。
●会員登録(無料)はこちらから
2.テスラ:自動運転を見据えたDX
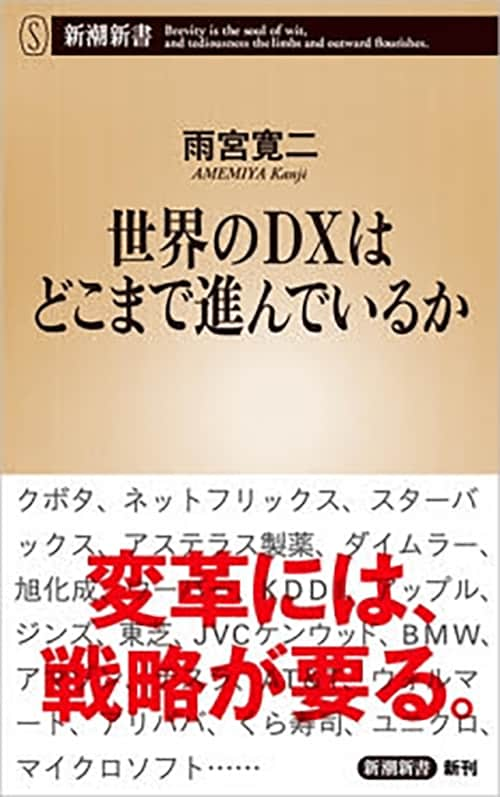
現在、電気自動車(EV:Electric Vehicle)の開発は、自動車業界においてニューノーマルとなりつつありますが、EVの存在をグローバルレベルで知らしめたのは、他でもないテスラです。
テスラが創業時に掲げた会社としてのコンセプトは、既存の自動車メーカーとは異なるものでした。自社のあるべき姿を「テクノロジー企業の側面を持つ自動車製造企業」とし、そのコアとなるのは、「バッテリー、ソフトウェア、独自のモーター」であるとしたのです。
この考え方は、従来の自動車メーカーが、自動車づくりの根幹に置くエンジンありきの発想を覆すものでした。イーロン・マスク氏は、2006年にテスラ最初の電気自動車となる「テスラ・ロードスター」のコンセプトを発表した際に、「炭化水素経済から太陽電池経済への移行を促進する」ためにテスラは存在すると述べましたが、この存在意義は、創業時に掲げたあるべき姿をより具現化するものとなりました。
実際にテスラ・ロードスターが販売開始となったのは2008年ですが、この時期の自動車業界は、トヨタのプリウスに見られるようにハイブリッド車中心の開発に留まるものでした。伝統的な自動車メーカーが、まだエンジンを主軸に考えた発想で自動車開発を進める時代に、既存のコンテクスト(文脈)に囚われず、異なる次元で発想してロードスターを完成させたところにテスラの革新性を読み取ることができます。
既存のコンテクストに縛られないとの発想は、独創的な販売形態や製造プロセスにも見て取れます。テスラは、伝統的な自動車メーカーとは異なり、「完全受注生産型」の形態を採っています。それを支えているのが、自社完結型の製造プロセスです。一般的に、自動車1台を組み立てるのに約3万個の部品が必要とされることから、自動車の組み立てには、各部品を製造するメーカーが多数存在します。日本では、これらの部品を自社で内製している率(部品内製率)が30%に留まり、70%は部品メーカーであるサプライヤーに依存しています。
日本の自動車メーカーが部品の供給の多くをサプライヤーに依存するのは、部品の開発や生産をアウトソーシングすることで、自動車メーカー自身の開発や生産に関わる業務量を節約し開発時間を短縮することが可能になるからです。
他方、米国では部品内製率が70%に達しており、日本とは対極的な状況にありますが、テスラは、これよりもさらに垂直統合度が進んでいます。座席からバッテリーセルに至るまでほぼ全ての部品が内製でまかなわれています。自前で多くのハードウェアを設計しソフトウェアを作成しているため、他の自動車メーカーが望めないほどの水準で車の製造プロセスをコントロールして完成度を高めることができるのです。
たとえば、2020年以降のコロナ禍で半導体の供給が困難に陥った際には、部品内製率の高さから、製造プロセスにおける臨機応変な軌道修正が可能となりました。テスラは自社で基板を設計しているため、パワーチップなど代替品を受け入れる形に即座に設計変更が可能であったことから、他の自動車メーカーにとって打撃が大きかったサプライチェーンの混乱をめぐる問題にもうまく対処することができたのです。
これに対して、日本の自動車メーカーや米国の一部の自動車メーカーは部品内製率が低いことから、リスクを伴う半導体の修正や、別の半導体工場の製品を使うことには慎重にならざるを得ませんでした。そのため、その対応には多くの時間が費やされることになったのです。
このように、テスラは、垂直統合度を高めた独自の製造プロセスを構築することにより、分業や組み立てコストを圧縮し、コストダウンを目的とした大量生産を図ることや余剰在庫を売り切る必要性を排除することで、「完全受注生産型」の自動車メーカーを貫いているのです。