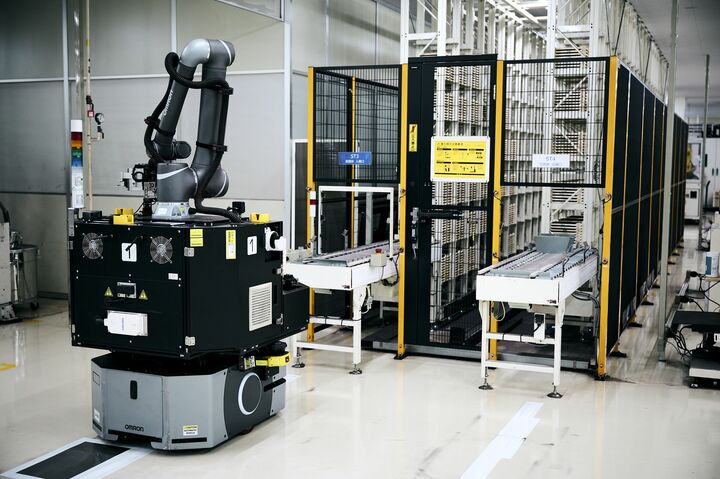
この地域でものづくりを続けるためには、DXが必須だった──。秋田県にかほ市にあるTDKの稲倉工場東サイトでは、移動型ロボットによる工程の自動化を進めている。壊れやすく取り扱いの難しいフェライト製品の製造に関する作業を機械で代替できるよう、2021年から試行錯誤を進めてきたという。その取り組みに追った。(前編/全2回)
モバイルマニピュレータを使った自動化に着手
1935年に設立された総合部品メーカーのTDK。その歴史は「フェライト」と呼ばれる磁性材料の事業化から始まっており、会社のロゴにも結晶化したフェライトの模様が表現されている。
現在、この創業製品のマザー工場に位置付けられているのが、稲倉工場東サイト(以下、稲倉東)である。同拠点では、数年がかりで抜本的なDXに取り組んでおり、その背景には「秋田の地でものづくりを続けたい」という思いがあったという。工場長の須田和博氏が説明する。
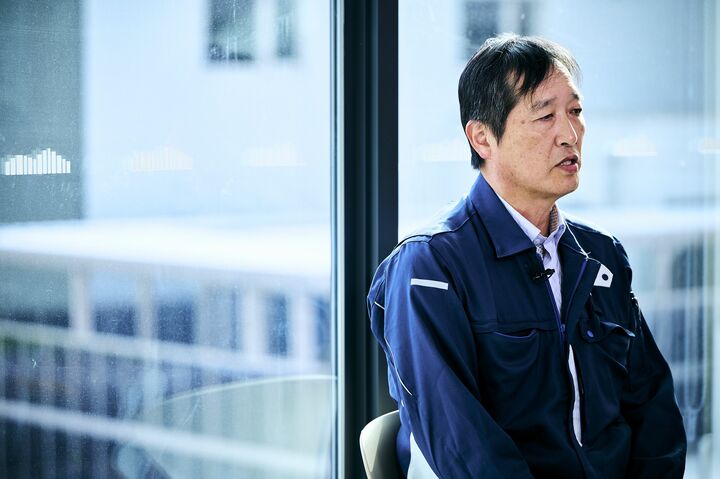
「ここ秋田県は、TDKを創業した齋藤憲三の出身地であり、当社の工場を数多く有する一大生産拠点です。しかし近年は少子高齢化が進み、人というリソースが希少になってきました。その中で、運ぶ・並べるといった単純作業は機械に置き換え、人はクリエイティブな仕事に集中してもらいたいと考えたのです」
フェライト製造の工程は手作業が中心であり、重い荷物を持つことも多いため、性別や身体的な問題によって作業が制限されるという実情があった。その制約をなくし、さまざまな人が活躍できる工場を目指すためにDXは必要だった。
加えて、センシング技術などによる設備の故障予知・保全を通して生産効率を上げること、機械化により人の作業で生まれるばらつきを抑制して品質安定を図ることも狙いにあったという。
象徴的なDXの取り組みが、ロボットを使った自動化だ。稲倉東では、2021年より人が行ってきた作業をロボットで代替する取り組みを進めてきた。
「私たちはモバイルマニピュレータを活用し、自動化を行っています」。そう話すのは、このプロジェクトを現場で進めてきたTDK 電子部品ビジネスカンパニー マグネティクスB.Grp 生産技術部 フェライト生産技術課工法技術係の小番保氏である。
モバイルマニピュレータとは、自律走行をしながら人と共に働くロボットであり、プログラムなどで設定された場所にロボットが移動してさまざまな作業を行う。「この工場では、ロボットと人が共同で作業を行う“ロボットアシストファクトリー”を目指しています」と小番氏は話す。
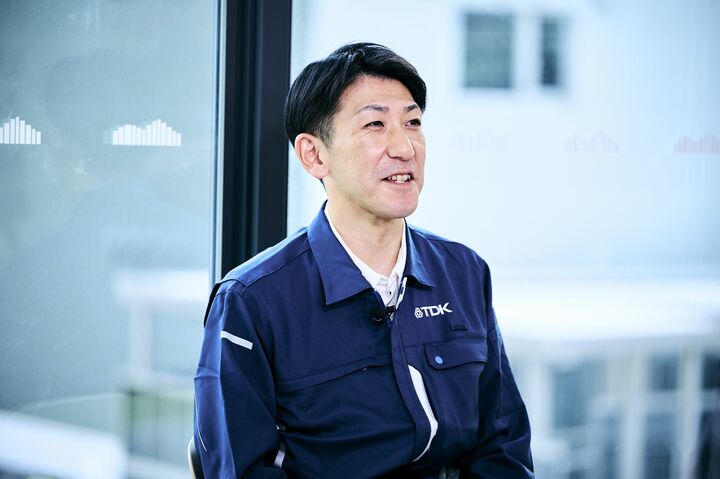
簡単に崩れるフェライトをロボットがどう扱うか
フェライトの製造工程には、顆粒(かりゅう)状のフェライト粉末を押し固める「成形」と、次にそれらを専用の容器に入れ、焼いて強度を上げる「焼成」がある。ロボットの活用でまず着手したのは、成形工程だった。従来は人が成形機を巡回・移動し、フェライト成形体を所定数の容器へ移し替えた後、人がその容器をハンドリフトで運搬するという一連を担っていたが、これら全ての自動化に成功しているという。
実際に成形機が所定数の成形を終えると、呼び出しを受けたロボットが待機場所から動き出し、自動倉庫から容器を受け取って成形機へ移動。成形機でフェライト成形体を容器へ移し替え、自動倉庫へ運んでいく光景があった。一気に全ラインで導入するのではなく、スモールスタートで実験的に運用を開始し、現在は2台のロボットが稼働している。
「難しかったのは、人のようにきめ細やかな動きをロボットで再現できるか、という点です。私たちが扱うフェライトは、指輪ほどの小さいものもあり、触れたら簡単に崩れるほど脆く柔らかい材質です。極めて取り扱いがシビアなのです。ここがハードルであり、これまで自動化が進まなかった要因の一つでもあるでしょう」(須田氏)
この点については、何度もロボットで動作検証を繰り返しながら改良していったという。例えば、ロボットがフェライト成形体の載ったトレイを傾けて焼成用の容器に移し替える作業がある。「傾きの角度はもちろん、移し替える際にロボットがトレイを引くスピードについても、人間の感覚的動作を数値化し、1秒あたりに何mm移動させるかというレベルで調整しました」(小番氏)。
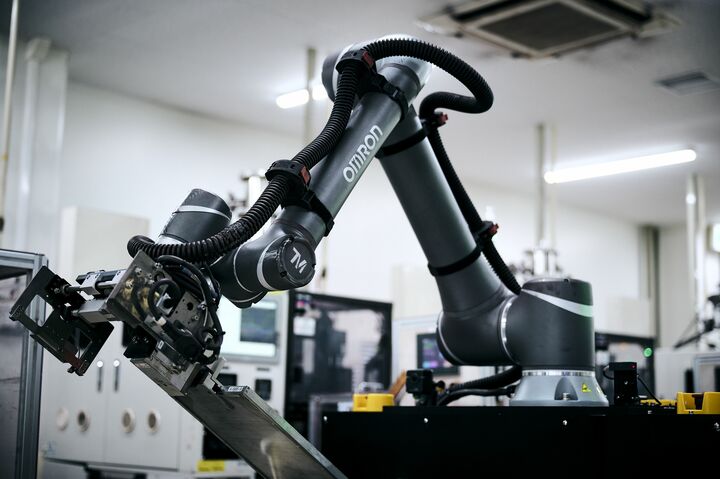
併せて工夫を重ねたのが、ロボットが決められた位置に的確に止まれるかという精度の向上だ。小さなフェライトを扱う分、わずかなズレがあれば成形機からの取り出しなどに不具合が生じる。導入したロボットは、もともと重量物を搬送するために作られたものであり、初期機能だけでは微細な停止位置の調整に限界があったという。
「そこで成形機にマークをつけ、ロボットはそのマークを基準点として相対的な位置を把握し、自ら調整するようにしました」(小番氏)
ロボットが人と協働する上でのリスク管理も細かく行っていった。工場内でロボットの立ち入りを禁止するエリアや低速移動エリアの設定に加え、どのくらいまで人に近づいて作業をしても良いかといったルールも区域ごと細かく決め、プログラムに反映していったという。
また、ロボットにはドライブレコーダーのようなカメラを装着し、エラーやバグが起きた際の動画をメーカーやSIer(システムインテグレーター)と検証し、改善していったという。
「難しい作業から自動化」で投資承認がスムーズに
このプロジェクトはステップ1~3の3段階で計画されており、ここまでに触れた成形工程の自動化はステップ1に該当する。すでに成功したことから、2023年以降はステップ2である焼成工程の自動化検証を行っている。
ステップ2は焼成炉の前半(2-1)と後半(2-2)の作業に分かれており、ステップ2-1でロボットが担うのは、自動倉庫からの製品の回収、運搬、焼成炉へのフェライト成形体投入である。ステップ1で行ったような、容器を傾けて移し替えるといった繊細な作業はなく、こちらの方が自動化の難易度は低いという。
一般的には難易度が低い工程から自動化に取り組む方が自然に思えるが、なぜあえて複雑な作業のある成形工程から先にチャレンジしたのか。理由として、この取り組みの意義や可能性を初期から経営層に理解してもらうためだったという。
「確かに焼成工程の方が難易度は低いのですが、一方で自動化の効果も小さくなります。事前に従業員の作業時間を調べたところ、焼成工程で自動化の対象となる作業は全体の10%もありませんでした。一方、成形工程は50%ほどになります。後者から始めて成功させた方が、自動化がもたらした効果を経営層に伝えやすく、今後このプロジェクトを進める上での信頼や期待につながるでしょう。投資承認もスムーズになるはずです」(小番氏)
ステップ2-1は2024年中に完成させ、翌年からはステップ2-2として、焼成工程後半までの自動化に着手し一連の工程の自動化完結を目指すという。ステップ3はこれら自動化の水平展開となる。
なお、移動型ロボットを適用しているのは、工場の中で品種も数量もそれほど多くない、いわゆる中品種中量生産のラインだという。その意図について、須田氏はこう説明する。
「このラインは、時期によって扱う材料や段取りが替わるため、フレキシビリティを持たせる必要があります。その点で、成形と焼成のラインを分け、その間のプログラムを柔軟に変えられる移動型ロボットで橋渡しするのが良いと考えました。一方、少品種大量生産のラインは、数カ月にわたって同じ内容で稼働し続けるのが一般的ですから、成形と焼成を分けず、設備一体でラインを連結した方が効率は良いでしょう」
数年がかりで行ってきた本プロジェクトだが、これらは同工場のDXの一部に過ぎない。後編記事では、その他の取り組みに触れながら、稲倉東が進めるDXの全体像を見ていく。
■【前編】「聖地・秋田で比類なき工場DXを」“TDKの原点”製造のマザー工場で人と共同作業を行うロボットの秘密 ※本稿
■【後編】作業の自動化を実現し2020年から故障ゼロ、TDKフェライト工場が掲げる「DXの次の目標」